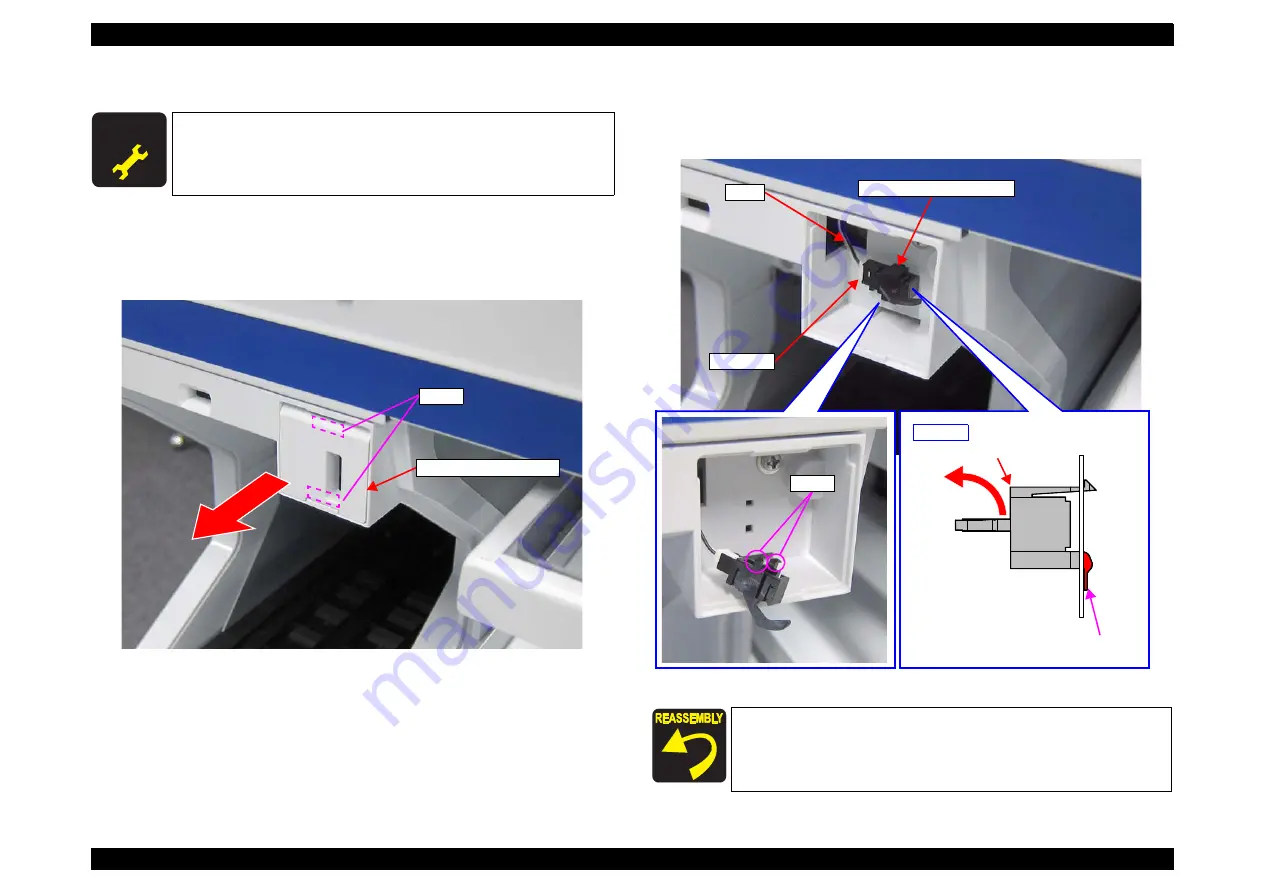
SC-F2000
Revision C
DISASSEMBLY & ASSEMBLY
Disassembly and Assembly Procedure
90
Confidential
3.4.3.16 LEFT IC COVER SENSOR
1.
Open the LEFT IC COVER.
2.
Disengage the two hooks using flat-blade screwdriver or a similar tool, and
remove the LEFT SENSOR COVER.
Figure 3-33. Removing the LEFT SENSOR COVER
3.
Disengage the two hooks, and remove the LEFT IC COVER SENSOR in the
direction of the arrow.
4.
Disconnect the cable from the connector of the sensor.
Figure 3-34. Removing the LEFT IC COVER SENSOR
A D J U S T M E N T
R E Q U I R E D
When replacing/removing this part, refer to
Items and the Order by Repaired Part”
perform the specified operations including required adjustment.
LEFT SENSOR COVER
Hooks
Engage the lower hook first when attaching the LEFT IC COVER
SENSOR
).
Hooks
LEFT IC COVER SENSOR
Connector
Cable
Side view
Hook (lower)
LEFT IC COVER SENSOR
Summary of Contents for SC-F2000 Series
Page 1: ...SC F2000 Direct To Garment Printer SERVICE MANUAL SECP13002 Confidential ...
Page 10: ...Confidential C H A P T E R 1 PRODUCTDESCRIPTION ...
Page 29: ...Confidential C H A P T E R 2 TROUBLESHOOTING ...
Page 52: ...Confidential C H A P T E R 3 DISASSEMBLY ASSEMBLY ...
Page 192: ...Confidential C H A P T E R 4 ADJUSTMENT ...
Page 285: ...Confidential C H A P T E R 5 MAINTENANCE ...