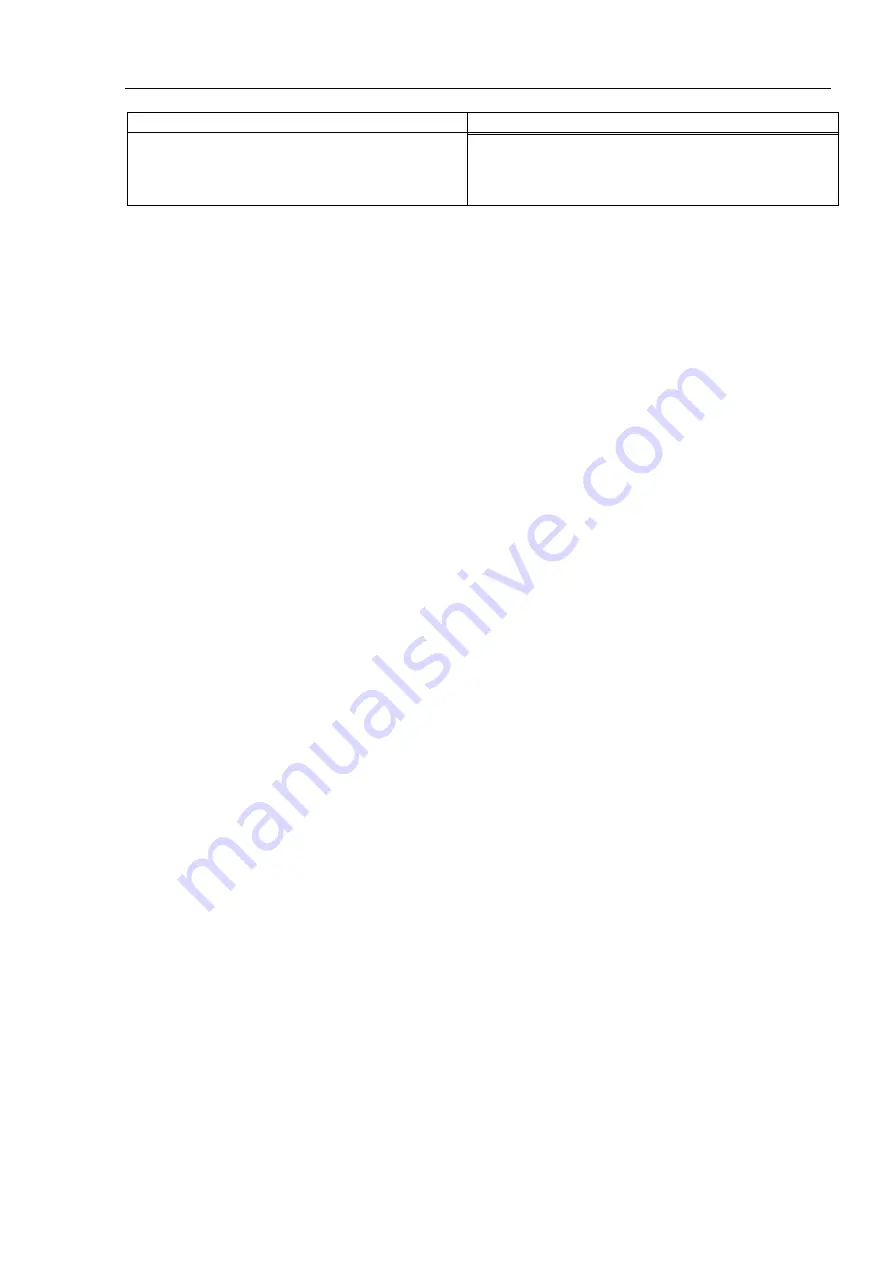
Appendix A: Specifications - GX4 Specifications
GX series Rev.2
195
Item
GX4-A*****
Safety standard
CE Marking, UKCA Marking:
EMC Directive, Machinery Directive, RoHS
Directive
KC Marking, KCs Marking
*1: The exhaust system in the Cleanroom & ESD model Manipulator (GX4-A**1C*) draws air from the base
interior and arm cover interior together.
A crack or other opening in the base unit can cause loss of negative air pressure in the outer part of the arm,
which can cause increased dust emission. Do not remove the maintenance cover on the front of the base.
Connect an exhaust tube to the exhaust port on the back of the base (or bottom of the base).
If the exhaust flow is not sufficient, dust particle emission may exceed the specified maximum level.
Cleanliness level : Class ISO 3 (ISO14644-1)
Exhaust System : Exhaust port diameter : Inner diameter: ø6 mm
Exhaust tube : Polyurethane tube
Outer diameter: ø6 mm (Inner diameter: ø4 mm)
Recommended exhaust flow rate : approx. 1000 cm
3
/s (Normal)
ESD model Manipulator (GX4-A**1E*) uses resin materials with antistatic treatment. This model
controls adhesion of dust due to electrification.
*2: In the case of PTP command. Maximum operating speed for CP command is 2000 mm/s on horizontal
plane.
*3: In the case where the center of gravity is at the center of Joint #4.
If the center of gravity is not at the center of Joint #4, set the parameter using Inertia command.
*4: When the product is used in a low temperature environment around the minimum temperature of the product
specification, or when the product is suspended for a long time on holidays or at night, a collision detection
error may occur due to the large resistance of the drive unit immediately after the start of operation. In such
a case, it is recommended to warm up for about 10 minutes.
*5: Conditions of Manipulator during measurement as follows:
Operating conditions : Under rated load, 4-joints simultaneous motion, maximum speed, and maximum
acceleration/deceleration.
Measurement point : Rear of the Manipulator, 1000 mm apart from the motion range, 50 mm above the
base-installed surface.
*6: In general use, Accel setting 100 is the optimum setting that maintains the balance of acceleration and
vibration when positioning.
Summary of Contents for SCARA GX Series
Page 1: ...Original instructions Rev 2 EM221R5129F SCARA Robots GX series Manual ...
Page 2: ...GX series Manual Rev 2 ...
Page 12: ......
Page 86: ...GX4 Manipulator 5 Motion Range 76 GX series Rev 2 ...
Page 88: ......
Page 188: ......
Page 202: ......