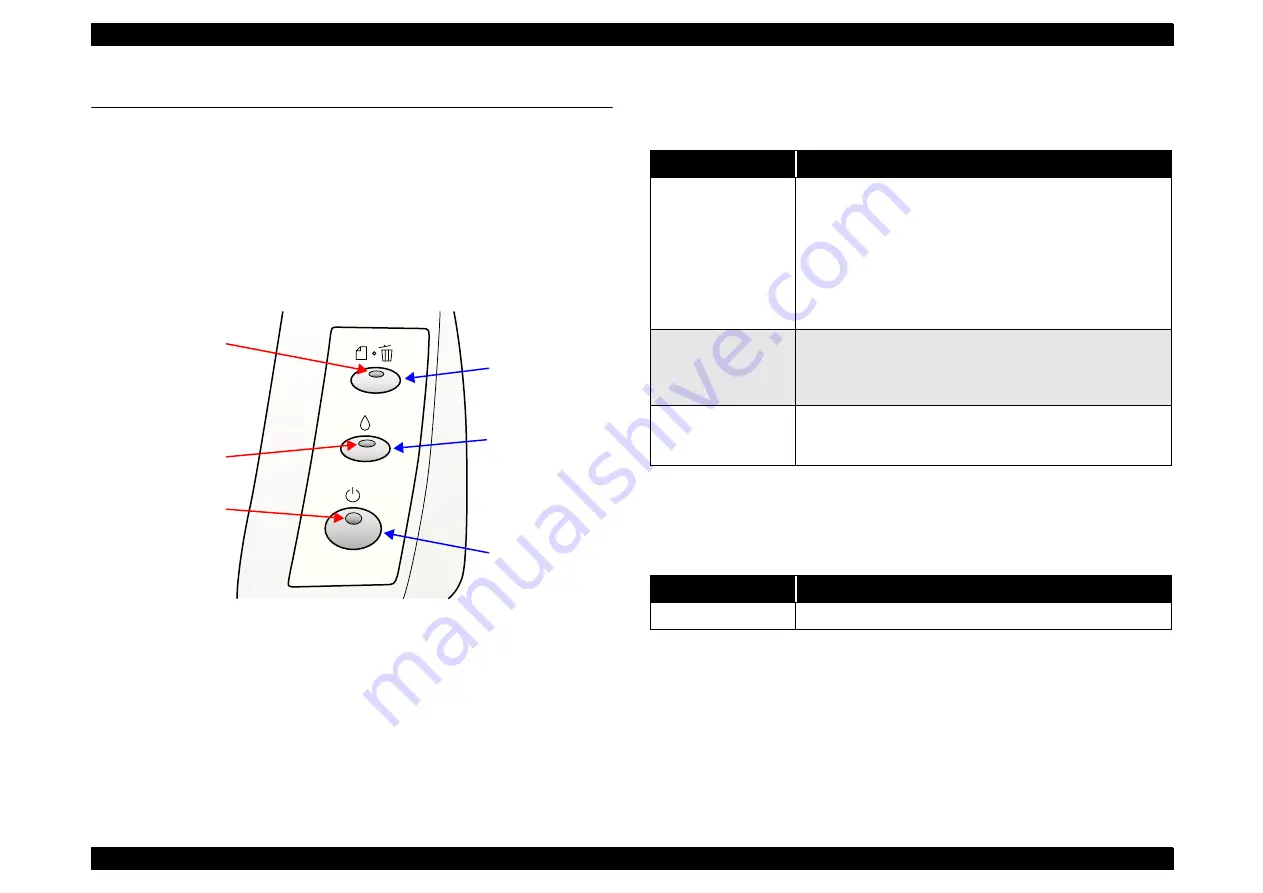
EPSON Stylus C82
Revision A
PRODUCT DESCRIPTION
Operator Controls
12
1.3 Operator Controls
1.3.1 Operate Switch
Operate switch is located on the control panel.
1.3.2 Control Panel
1.3.2.1 Switches
There are 3 non-lock type push switches, and 3 LEDs.
Figure 1-3. Control panel
1.3.2.2 Indicators
Power
Lights when the operate switch is “ON”, and AC power is supplied.
Paper Out
Lights during the paper-out condition, and blinks during the paper-jam condition.
Ink Out
Lights during no ink condition, and blinks during the ink low condition.
1.3.3 Panel Functions
NOTE:
(*1) 3 seconds is required at the user’s manual.
NOTE:
(*2) This function is not available in printing status.
NOTE:
(*) Status printings prints firmware version, ink counter and nozzle
check patterns.
NOTE:
The Stylus C82 cannot cancel a maintenance error from the control
panel. When a maintenance error is generated, use the Adjustment
Program to clear the counter value.
Ink SW
Paper SW
Power SW
Paper Out LED
Power LED
Ink Out LED
Table 1-4. Panel functions
Switch
Function
Paper
print cancel
• Loads or ejects the paper.
• When carriage is on the ink check position, move carriage to
next ink check position or cartridge change position.
• When carriage is on the ink cartridge change position, return
carriage from ink cartridge change position.
• In the condition of “Double feed error”, recovering from error
condition, printing is restarted.
• In the condition of printing, cancel the print job.
Ink
• Starts the ink cartridge change sequence.
(
*
2)
Move the carriage to cartridge change position.
• When carriage is on the ink change position, return carriage
from ink cartridge change position.
Ink
(Pushing for 2 seconds *
1
)
• Starts the cleaning of head.
• In the condition of “Ink low” or “Ink out” or “No ink cartridge”,
starts the ink cartridge change sequence.
Table 1-5. Panel functions with power on
Switch
Pressing with power on function
Paper
Start status printings.
(
*
1)
Summary of Contents for Stylus C82
Page 1: ...EPSONStylusC82 Color Inkjet Printer SEIJ02003 SERVICE MANUAL ...
Page 5: ...Revision Status Revision Issued Date Description A July 31 2002 First Release ...
Page 8: ...C H A P T E R 1 PRODUCTDESCRIPTION ...
Page 16: ...C H A P T E R 2 OPERATINGPRINCIPLES ...
Page 21: ...C H A P T E R 3 TROUBLESHOOTING ...
Page 24: ...C H A P T E R 4 DISASSEMBLYANDASSEMBLY ...
Page 43: ...C H A P T E R 5 ADJUSTMENT ...
Page 46: ...C H A P T E R 6 MAINTENANCE ...
Page 51: ...C H A P T E R 7 APPENDIX ...
Page 58: ...EPSON Stylus C82 Revision A APPENDIX Electrical Circuits 58 7 3 Electrical Circuits ...
Page 59: ...EPSON Stylus C82 Revision A APPENDIX Electrical Circuits 59 ...
Page 60: ...EPSON Stylus C82 Revision A APPENDIX Electrical Circuits 60 ...
Page 61: ...EPSON Stylus C82 Revision A APPENDIX Electrical Circuits 61 ...