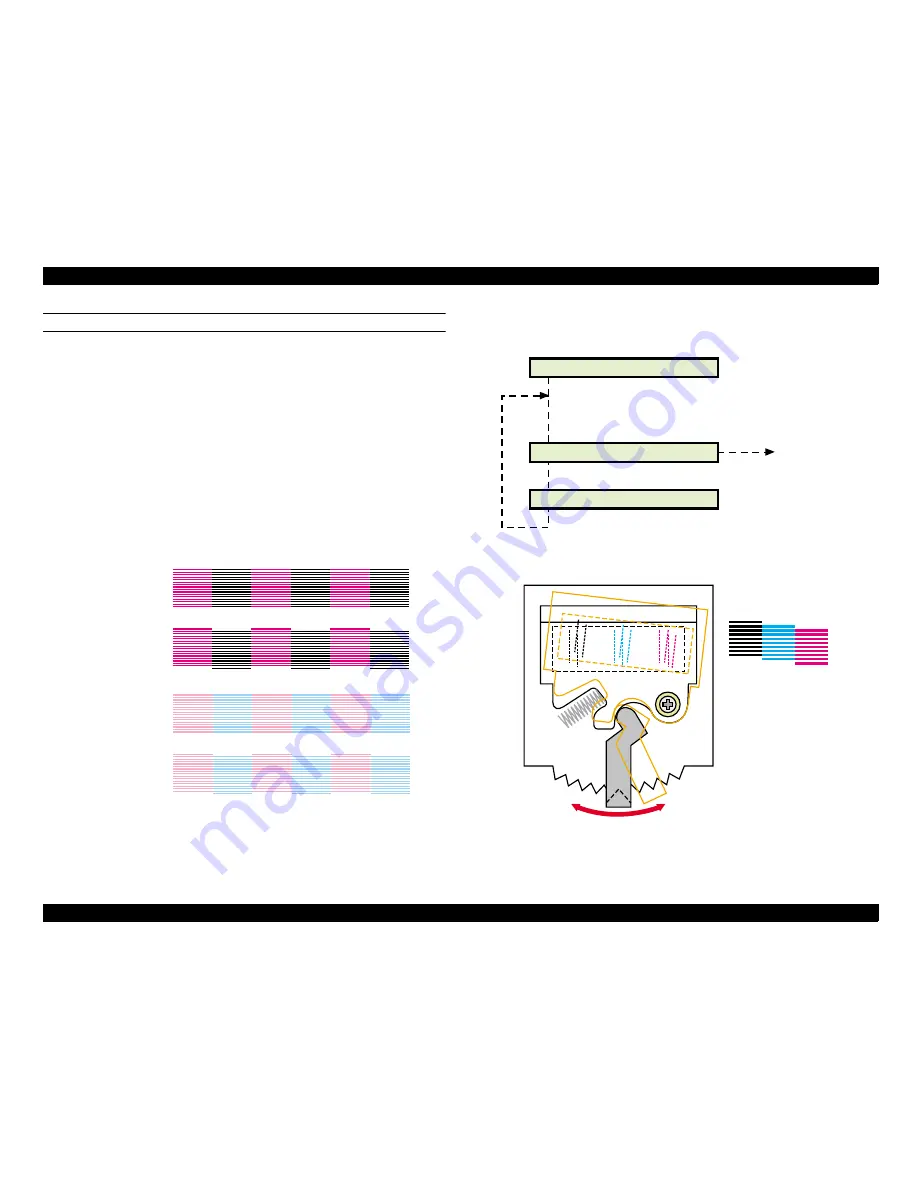
EPSON Stylus Pro 7000
Revision A
Adjustment
Self-Diagnostic Mode Menus
176
ADJ X HEAD SLANT (B/C HEADS)
This function prints a check pattern (one-at-a-time for each head) to make
sure the printheads are installed straight up-and-down. Use the patterns to
determine whether one or both printheads need adjustment. To correct any
slant, use "Head Adjust Lever A" as described below.
1.
Make sure "Adj: x Head Slant" appears in the LCD, and press the Enter
button. (x = B or C depending on the printhead) After the check pattern
prints, "x Slant Check End" (x = B or C head) appears in the LCD.
2.
Compare the printed pattern with the illustration below. Press Enter if the
lines are parallel, as shown in the “OK” examples below. If there is a
slant, open the front cover, release the carriage lock by hand, and move
the carriage away from the carriage cap position. Next, loosen the screw
securing the head that is printing at a slant, and move the Head Adjust
Lever A left or right depending on the slant direction. See Figure 5-21 for
reference. Tighten the screw.
Figure 5-19. Head Slant Check Printout
3.
After making sure both heads are correctly installed, move the carriage
back to the capping position by hand and close the front cover.
4.
Select “Print Adj Pattern” with the SelecType or Item button, and print the
pattern again to make sure there is no slant. Adjust again if necessary. If
there is no slant, press Enter.
Figure 5-20. Head Slant Check Operation
Figure 5-21. B/C Head Skew Adjust Lever
OK
Bad
Magenta
Black
OK
Bad
Light
Magenta
Light
Cyan
B head check pattern
C head check pattern
Printing Pattern
Check the pattern for offset lines or
segments and change the adjust
lever position if necessary.
x Slant Check End
Print Adj. Pattern
[Enter]
[SelecType]/[Item]
Check other
head/end
adjustment
Head Adjust Lever A
(in front of B/C heads)
Summary of Contents for StylusPRO 7000
Page 1: ...EPSONStylusPRO7000 Color Large Format Inkjet Printer SEIJ99017 SERVICE MANUAL ...
Page 6: ...Revision Status Revision Issued Date Description Rev A February 17 2000 First Release ...
Page 11: ...C H A P T E R 1 PRODUCTDESCRIPTION ...
Page 55: ...C H A P T E R 2 OPERATINGPRINCIPLES ...
Page 80: ...C H A P T E R 3 TROUBLESHOOTING ...
Page 106: ...C H A P T E R 4 DISASSEMBLY ASSEMBLY ...
Page 153: ...C H A P T E R 5 ADJUSTMENT ...
Page 195: ...C H A P T E R 6 MAINTENANCE SETUP ...
Page 199: ...C H A P T E R 7 APPENDIX ...
Page 223: ......
Page 224: ......
Page 225: ......