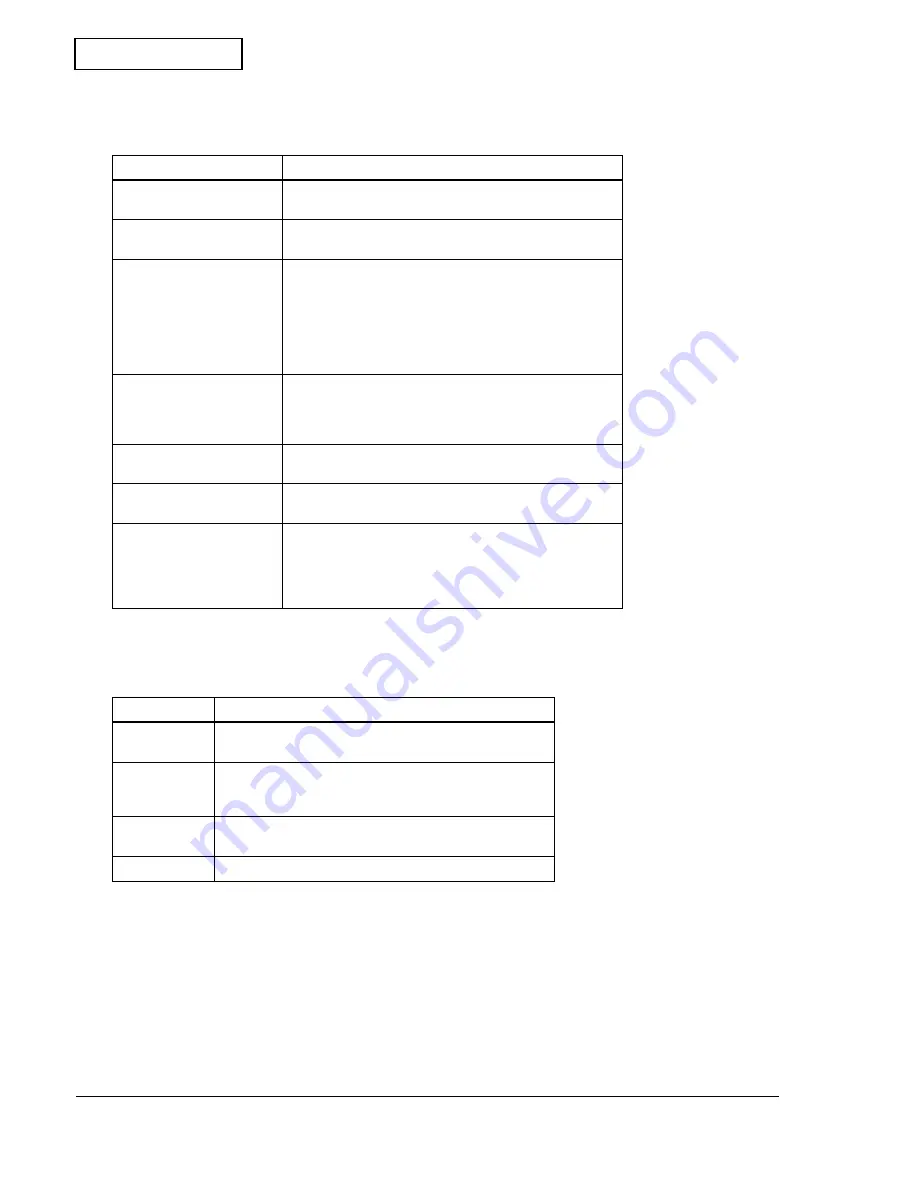
6-16
Installation
Rev.B
Confidential
Customized Values
Table 6-9 Customized values
Serial Communication Conditions
Table 6-10 Serial communication conditions
Function
Selection
Select NV user memory
capacity
1KB 64KB 128KB 192KB
Select NV bit image
memory capacity
None 64KB 128KB 192KB 256KB 320KB 384KB
Select paper width
38 mm
39 mm
•
•
•
80 mm (43 steps in increment of 1 mm, except for the size
from 71 mm to 79 mm)
Select number of division
for head energizing
Undivided energizing
Two-part energizing
Three-part energizing
Four-part energizing
Select print density
×
0.7,
×
0.75,
×
0.8,
×
0.85,
×
0.9,
×
0.95,
×
1.0,
×
1.05,
×
1.1,
×
1.15,
×
1.2,
×
1.25,
×
1.3,
×
1.35,
×
1.4
Select paper type (mono
or color)
Single color
Two colors
Select print speed
Print speed level 1
•
•
•
Print speed level 9
Function
Selection
Baud rate
2400 bps, 4800 bps, 9600 bps, 19200 bps,
38400 bps, 57600 bps, 115200 bps
Parity
None
Odd
Even
Flow control
DTR/DSR control
XON/XOFF control
Data length
7 bits, 8 bits