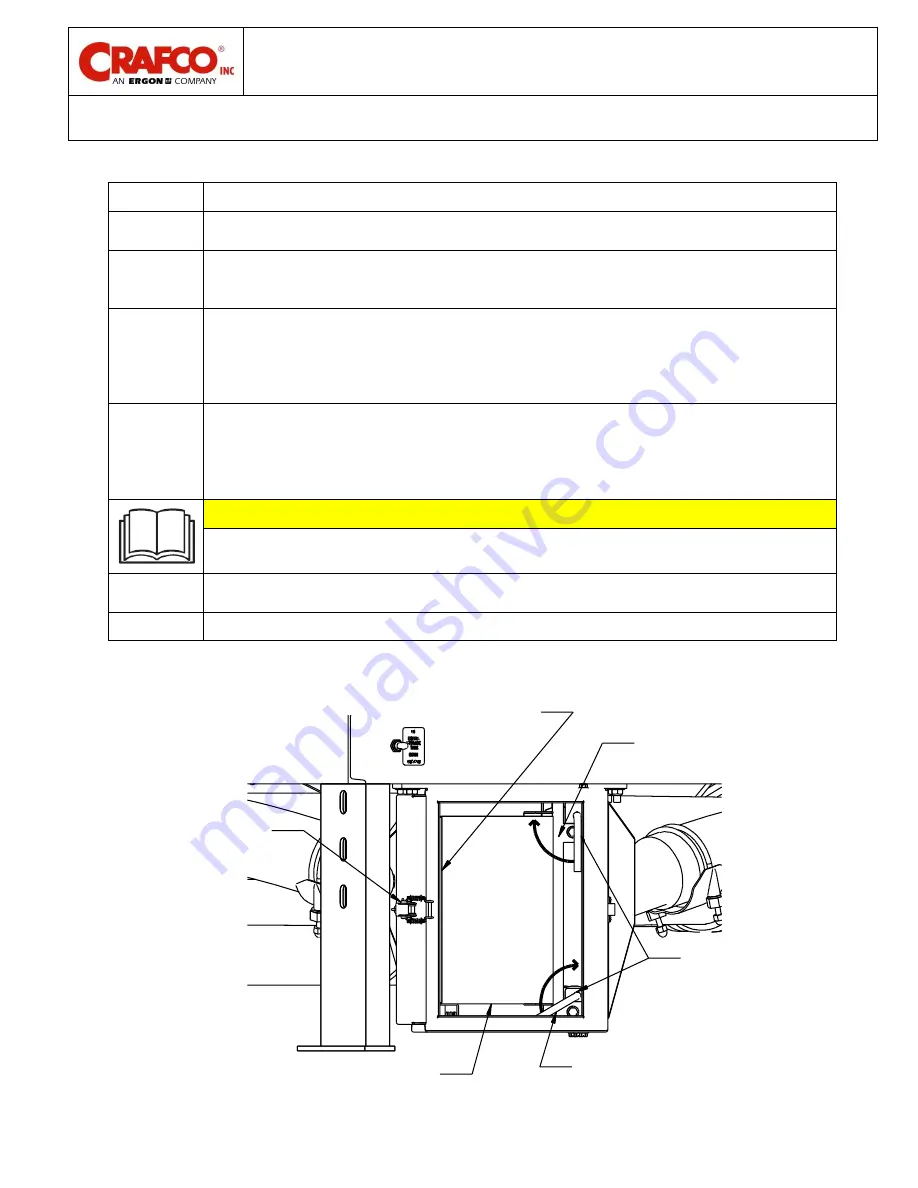
Crack-Vac Model 100G Manual
Chapter 5 Operating Instructions
©2020 by Crafco, Inc. All Rights Reserved
Operating Instructions 5-13
Step
Action
2
Rotate the cam lever handles counterclockwise to disengage the filter push bar
assembly. This will relieve pressure on the filter seal.
3
Reach beneath the HEPA panel filter and lift and wiggle the filter from side to side to
make sure the filter push bar assembly has retracted and relieved pressure on the
filter seal.
4
Once pressure on the seal has been released, the filter can be pulled outward to
remove the filter from the housing. Make sure the upper cam lever is rotated
completely upward to prevent it blocking the filter from being removed.
Note:
make sure the filter seal has disengaged from the sealing lip to prevent
damaging the filter seal when pulling filter outward.
5
To insert the filter; make sure the filter push bar assembly is in the rearward position.
Place the leading edge of the filter on the support brackets and push the filter into
the housing until it hits the stop brackets.
Note:
it may be necessary to slightly lift the trailing edge of the filter to allow it to go
all the way into the filter housing.
CAUTION
Make sure the filter seal is in the correct orientation to create a proper seal.
6
Rotate the cam lever handles counterclockwise to push the filter forward and
compress the filter seal on the sealing lip of the filter housing.
7
Close the filter housing door and engage the latch.
DISENGAGE BY ROTATING
CAM LEVER HANDLES CLOCKWISE
SEAL EDGE ON
THIS SIDE
LIFT AND PULL FILTER
FROM THIS EDGE
CAM LEVER
HANDLES
FILTER PUSH BAR
ASSEMBLY
FILTER HOUSING
DOOR AND LATCH
Table 5-14 HEPA Filter Access (continued)
Figure 5-6 HEPA Filter & Housing
Summary of Contents for 60800N
Page 1: ...CRACK VAC MODEL 100G Operator Parts Manual 26627N Revision O ...
Page 3: ...Crack Vac Model 100G Manual Revisions Revision Date ...
Page 4: ...CRACK VAC MODEL 100G with COMPRESSOR P N 60900N CRACK VAC MODEL 100G P N 60800N ...
Page 10: ......
Page 12: ......
Page 18: ......
Page 22: ......
Page 40: ......
Page 77: ......
Page 78: ... 2020 Crafco Inc ...