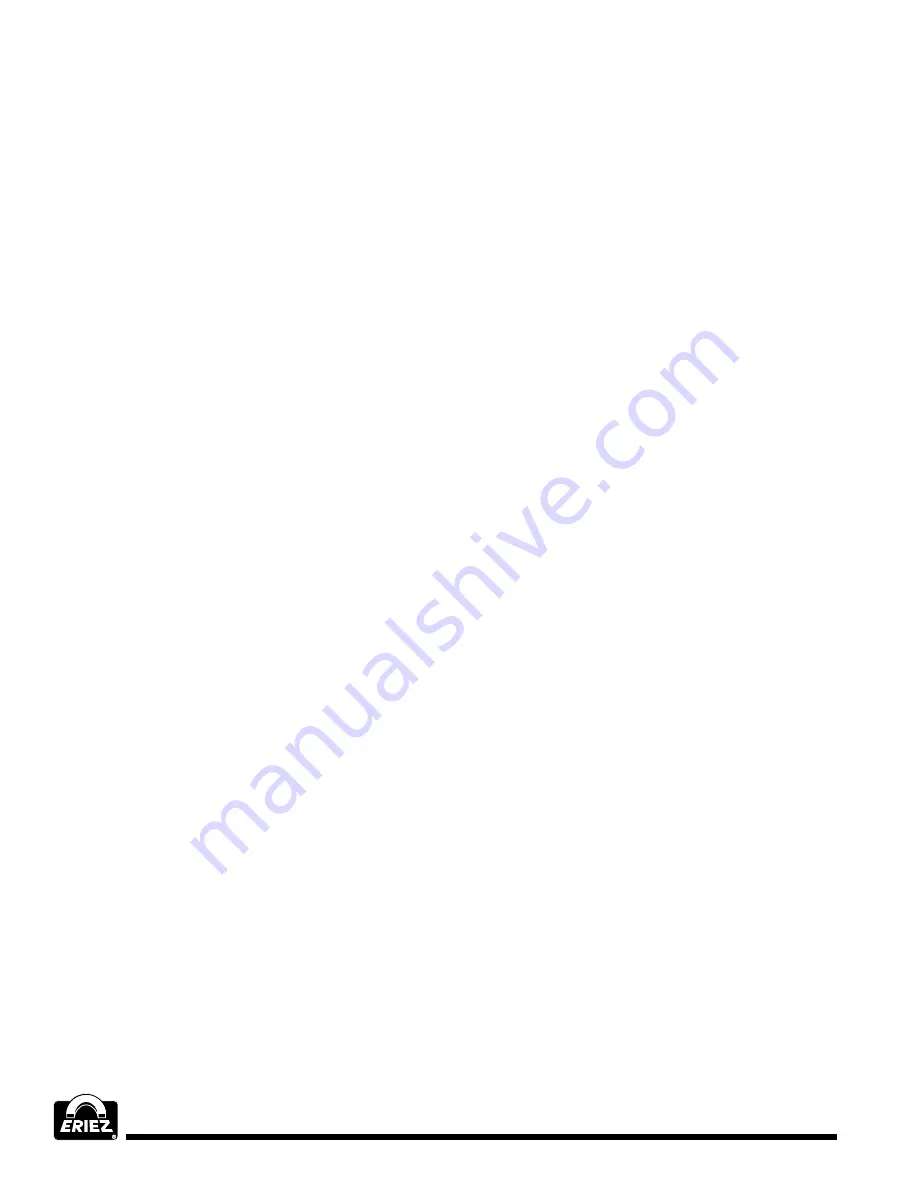
12
D. Vacuum new fluid into the sump cleaner.
E. As soon as fluid stops passing through
the hose, stop the engine by turning the
IGNITION switch OFF. Close the gas bottle
valve. This valve must always be closed
when engine is not running.
The tank’s maximum capacity is, at most, 10%
above the rated capacity. A float switch in the
tank and wired into the engine ignition circuit
will shut down the engine if overfilling starts
to occur. If this happens, place the IGNITION
switch in the OFF position, and close the
gas bottle valve. Follow instructions for the
discharge operation in Paragraph 10.
8. To discharge clean fluid:
close the suction
inlet ball valve V1, attach the 1-½" hose to the
discharge port on the clean side of the unit.
Move the 4-way valve control lever to the
vertical (DISCHARGE) position. Open the
gas bottle valve and press the electric primer
button for at least two seconds. Turn the
IGNITION KEY SWITCH ON. Depress the
discharge hose nozzle valve.
A. THE SUCTION/DISCHARGE lever must
be turned its full quarter turn to the vertical
(DISCHARGE) position in order to close a
limit switch beneath the lever (FIGURE II-F).
This limit switch bypasses the float switch
needed to prevent overfilling during the
suction operation, but is not required for
discharge operation. The engine won’t start
in the discharge mode if sump cleaner tank
is full and the limit switch is not closed.
B. Be sure the suction inlet ball valve V1
is fully closed before operating in the
discharge mode!
C. IMPORTANT! Be sure the suction inlet
ball valve V1 is fully closed or fully open,
depending on the desired operation (closed-
discharge, open-suction). Failure to do so
will allow particulates to enter the valve
seat and seize the valve.
D As soon as fluid stops passing through
the hose, release pressure by shifting the
SUCTION/DISCHARGE lever to the
horizontal (SUCTION) position. This must
be done before opening the inlet ball valve
or removing tank lid, cleanout door or drain
plug. The engine will momentarily “SPEED
UP” and then “SLOW DOWN” and begin to
“labor”. Once the engine has begun to
labor, the engine may be switched OFF.
Open the ball valve and turn OFF the
gas bottle valve.
The sump cleaner will discharge all but about
an inch of fluid in the bottom of the compart-
ment. This is unimportant if the compartment
is used for one type of coolant only. If different
coolants are involved, remove the compart-
ment’s drain plug to empty it completely.
Replace drain plug after emptying.
Summary of Contents for FJ-310A
Page 27: ...Sump Cleaner 27...