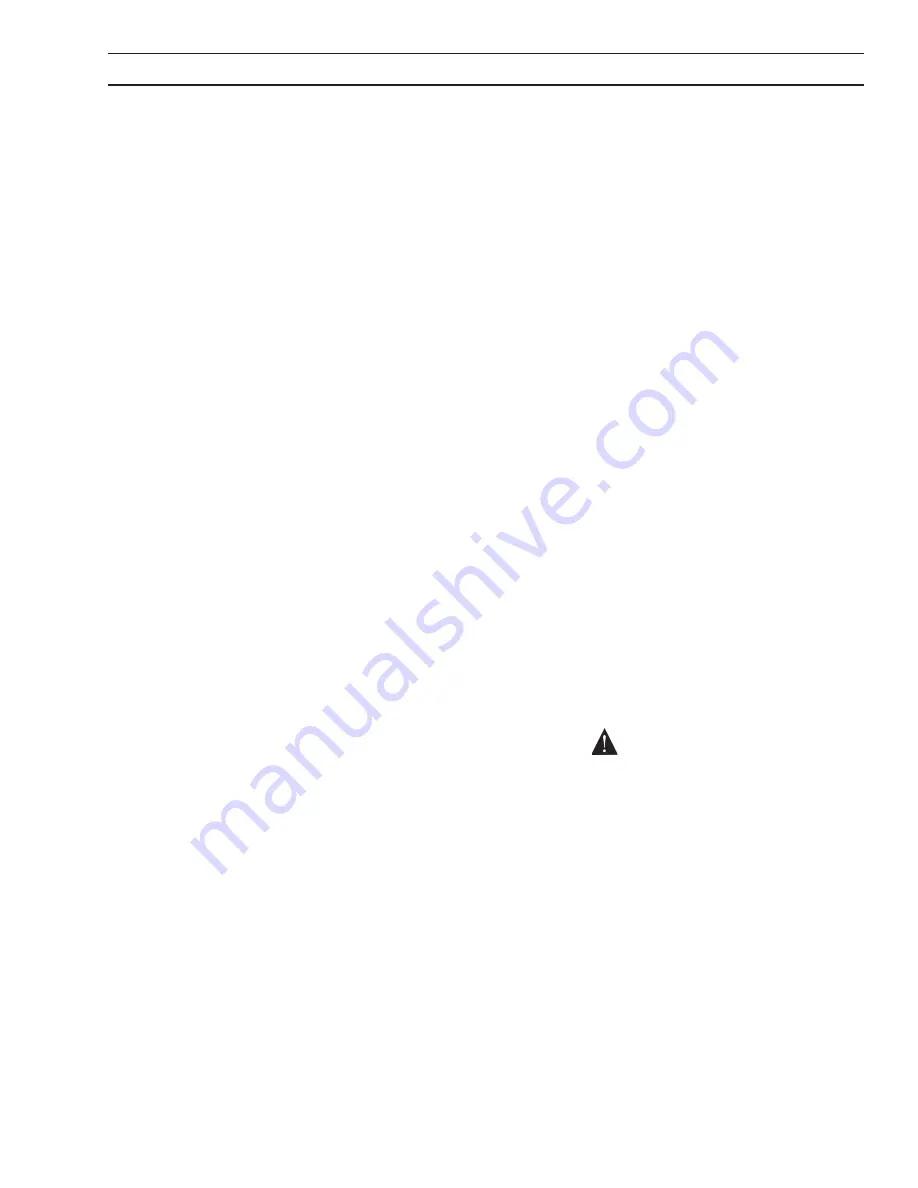
7
SECTION 1
DESCRIPTION
gun torch designed for the mig welding process. It is
completely portable (up to 30-ft.), air-cooled and hand
operated, and weighs less than three (3) pounds which
allows for great maneuverability and operator conve-
nience. The gun is equipped with three thirty (30) foot
service lines; control cable with amphenol plug, power
cable with twist-lock connector, gas hose for direct
connection to gas cylinder.
1.4.2 ST-23A SPOOL-ON-GUN TORCH, P/N 19164;
ADAPTOR KIT ST-23A TO 251cv P/N 37301
The ST-23A Spool-On-Gun torch can also be used with
the 251cv but the adaptor kit, P/N 37301, will be required.
The adaptor is equipped with a gas hose for hooking up
to a flowmeter.
1.4.3 TR-24 SINGLE CYLINDER TRUCK KIT, P/N
37300 or TR-251cv DUAL CYLINDER TRUCK
KIT, P/N 36700
Provides complete mobility for power source. Each kit
includes handle, 4 castors, and 1 or 2 gas cylinder
brackets.
1.4.4 METER KIT, P/N 36699
LCD meter has volt/amp selector switch to display actual
welding voltage or current. Mounts easily to the front
control panels of 251cv power source.
1.5 SAFETY
Before the equipment is put into operation, the safety
section at the front of this manual should be read com-
pletely. This will help avoid possible injury due to misuse
or improper welding applications.
The symbol
which precedes safety notes appear-
ing throughout this manual means “Attention! Be Alert!
Your safety is involved.” The definitions relating to the
DANGER, WARNING and CAUTION safety notations
are described at the end of the Safety Section in the front
of this manual -- read them and their specific text refer-
ences carefully.
1.6 DUTY CYCLE AND CURVES (Figure 1.1)
The duty cycle of the equipment is the percentage of a 10
minute period which it can operate at a given output
current without overheating. The 251cv Power Source is
rated at 40% duty cycle. This means that the equipment
can be operated at 250 amperes for four minutes out of
every 10. This cycle can be repeated indefinitely (See
Figure 1.1).
1.1 GENERAL
This manual has been prepared especially for use in
familiarizing personnel with the design, installation, op-
eration, maintenance, and troubleshooting of this equip-
ment. All information presented here in should be given
careful consideration to assure optimum performance of
this equipment.
1.2 RECEIVING-HANDLING
Prior to installing this equipment, clean all packing mate-
rial from around the unit and carefully inspect for any
damage that may have occurred during shipment. Any
claims for loss or damage that may have occurred in
transit must be filed by the purchaser with the carrier. A
copy of the bill of lading and freight bill will be furnished
by the carrier on request if occasion to file claim arises.
When requesting information concerning this equip-
ment, it is essential that Part, Serial and Model Numbers
of the equipment be supplied.
1.3 DESCRIPTION
The 251cv Power Source has been designed for fine
wire, (0.023, 0.030, 0.035 and 0.045 in.) welding using
the short arc method, as well as for spray arc aluminum,
short arc and spray arc stainless steel and spray arc
cored wires. It also has a built-in control for operating an
optional spool-on-gun and has provisions for an optional
undercarriage with single cylinder rack or a dual cylinder
rack.
1.3.1 251cv POWER SOURCE
The power source consists of a single phase trans-
former, single phase full wave controlled rectifier, stabi-
lizing reactor, filtering capacitors and internal output
connections for polarity reversal. See front cover for list
of available 251cv power sources.
1.3.2 OPTIONAL CONTROLS
The 251cv can be used to weld hard and aluminum wire
with an optional MT-250SG spool-on-gun torch. The
optional spool-on-gun adaptors and control, when used
in conjunction with the optional MT-250SG torch, permits
aluminum wire welding with the machine.
1.4 OPTIONAL ACCESSORIES
1.4.1 MT-250SG SPOOL-ON-GUN TORCH, P/N 36779
The 251CV unit is equipped with a control for the MT-
250SG Spool-On-Gun welding torch. This is a high
performance, 250 ampere continuous duty spool-on-