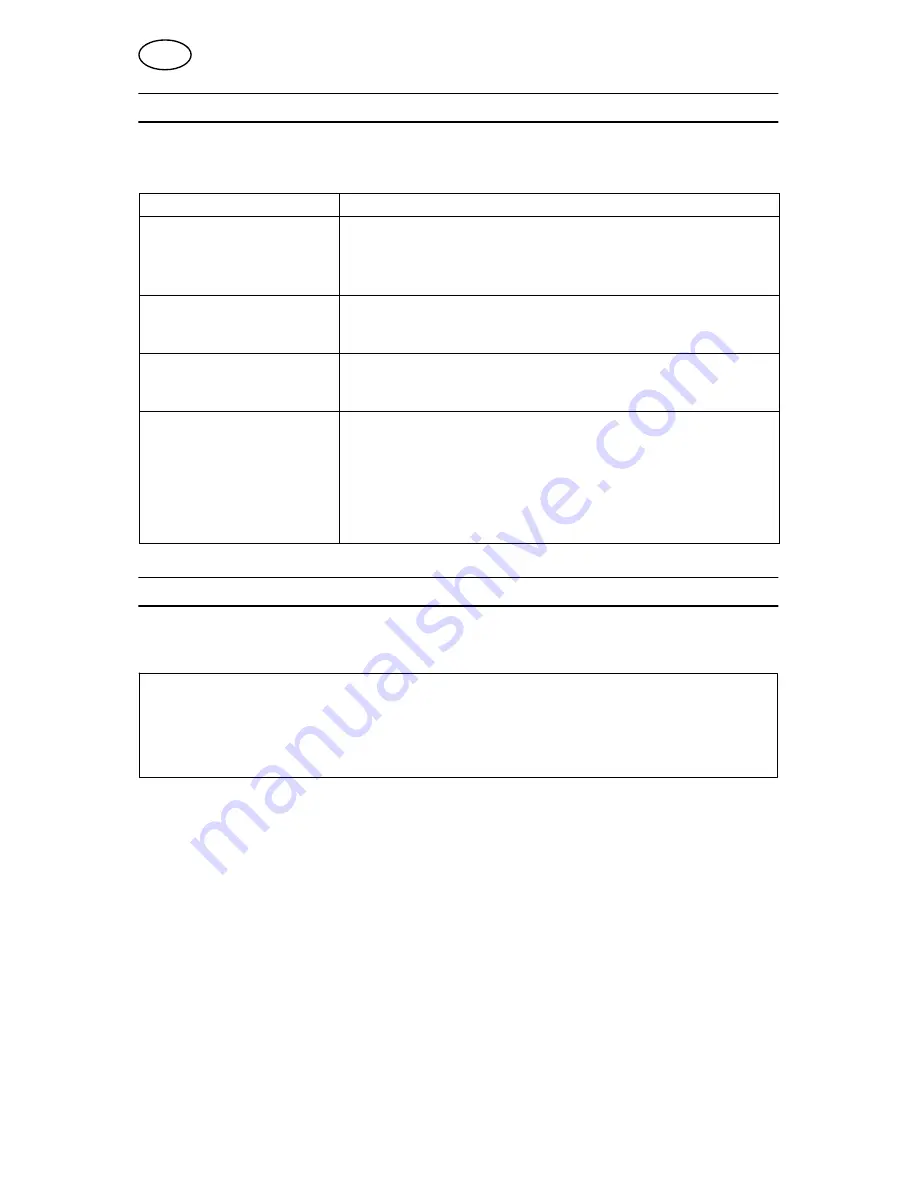
© ESAB AB 2011
- 15 -
bc23de
7
FAULT TRACING
Try these recommended checks and inspections before sending for an authorised
service technican.
Type of fault
Actions
No arc
S
Check that the mains power supply switch is turned on.
S
Check that the welding current supply and return cables are
correctly connected.
S
Check that correct current value is set.
Welding current is interrupted
during welding
S
Check whether the thermal overload trip has operated
(indicated by the orange lamp on the front).
S
Check the main power supply fuses.
Thermal overload trips
operate frequently
S
Check to see whether the air filters are clogged.
S
Make sure that you are not exceeding the rated data for the
power source (i.e. that the unit is not being overloaded).
Poor welding performance
S
Check that the welding current supply and return cables are
correctly connected.
S
Check that the correct current value is set.
S
Check that the correct welding wires are being used.
S
Check the main power supply fuses.
S
Check the wire feed unit - if proper rolls are applied and
properly set the pressure of the wire feeder's pressure rollers
8
ORDERING OF SPARE PARTS
Repair and electrical work should be performed by an authorised ESAB service
technician. Use only ESAB original spare and wear parts.
Mig C280 PRO, Mig C340 PRO is designed and tested in accordance with the interna
tional and European standards 60974-1, 60974-5 and 60974-10 . It is the obligation of
the service unit which has carried out the service or repair work to make sure that the
product still conforms to the said standard.
Spare parts may be ordered through your nearest ESAB dealer, see the last page of
this publication.
GB
Summary of Contents for ORIGO Mig C280 PRO
Page 2: ... 2 ...
Page 16: ... ESAB AB 2011 Diagram 16 bc23e Mig C280 380 415V ...
Page 17: ... ESAB AB 2011 17 bc23e Mig C280 380 415V ...
Page 18: ... ESAB AB 2011 18 bc23e Mig C280 230 500V ...
Page 19: ... ESAB AB 2011 19 bc23e Mig C280 230 500V ...
Page 20: ... ESAB AB 2011 20 bc23e Mig C340 380 415V ...
Page 21: ... ESAB AB 2011 21 bc23e Mig C340 380 415V ...
Page 22: ... ESAB AB 2011 22 bc23e Mig C340 230 500V ...
Page 23: ... ESAB AB 2011 23 bc23e Mig C340 230 500V ...
Page 24: ... ESAB AB 2011 Connection instruction 24 bc23c 230V 380 415V 440 460V 500V ...
Page 30: ... 30 notes NOTES ...
Page 31: ... 31 notes NOTES ...