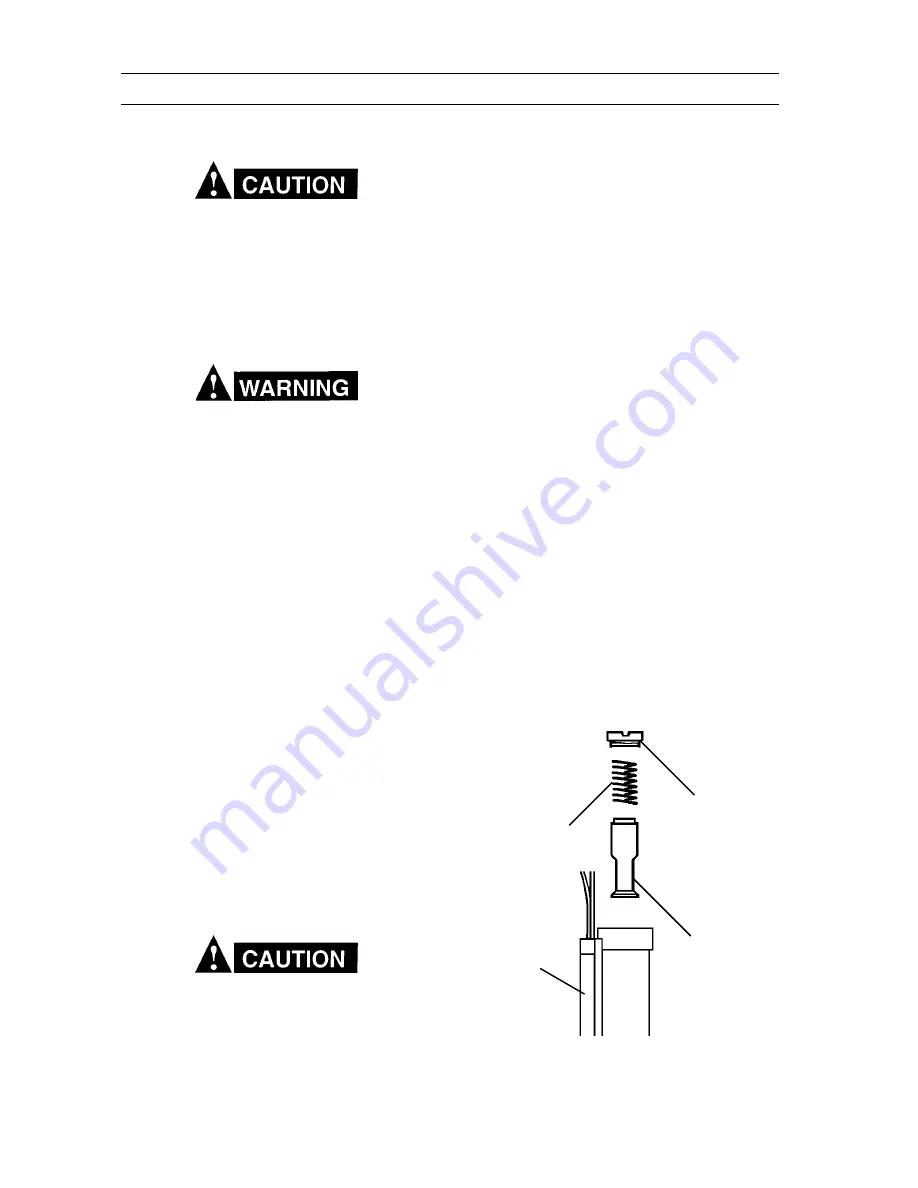
18
SECTION 4
MAINTENANCE
4.1 GENERAL
If this equipment does not operate properly,
stop work immediately and investigate the cause
of the malfunction. Maintenance work must be
performed by an experienced person, and elec-
trical work by a trained electrician. Do not permit
untrained persons to inspect, clean, or repair
this equipment. Use only recommended re-
placement parts.
Be sure that the wall disconnect switch or wall
circuit breaker is open before attempting any
inspection or work inside of the PowerCut-
550.
4.2 INSPECTION AND CLEANING
Frequent inspection and cleaning of the PowerCut-
550 is recommended for safety and proper opera-
tion. Some suggestions for inspecting and cleaning
are as follows:
A.
Check work cable to workpiece connection.
B.
Check safety earth ground at workpiece and at
power source chassis.
C.
Check heat shield on torch. It should be
replaced if damaged.
D.
Check the torch electrode and cutting nozzle
for wear on a daily basis. Remove spatter or
replace if necessary.
E.
Make sure cable and hoses are not damaged
or kinked.
F.
Make sure all fittings and ground connections
are tight.
Water or oil occasionally accumulates in com-
pressed air lines. Be sure to direct the first blast
of air away from the equipment to avoid damage
to the PowerCut-550.
PISTON PLUG
PISTON
SPRING
FLOW SWITCH
H.
With all input power disconnected, and wear-
ing proper eye and face protection, blow out
the inside of the PowerCut-550 using low-
pressure dry compressed air.
4.3 FLOW SWITCH (FIGURE 4-1)
When excessive contamination is found in the air,
the flow switch (FS) should be removed, disas-
sembled and cleaned as follows:
A.
Ensure the system is shut down and there is no
trapped air under pressure in the piping.
B.
Remove the piston plug.
C.
Remove the spring (FS-4 only). Use care when
handling spring to prevent distortion.
D.
Remove the piston.
E.
Clean all parts with cleaning agent.
NOTE
Ensure cleaning agent does not contain sol-
vents which can degrade polysulfone. Warm
water and detergent is recommended for clean-
ing. Allow all parts to dry thoroughly before
reassembly.
Reassemble the flow switch in reverse order.
Figure 4-1. Disassembly / Assembly of Flow Switch