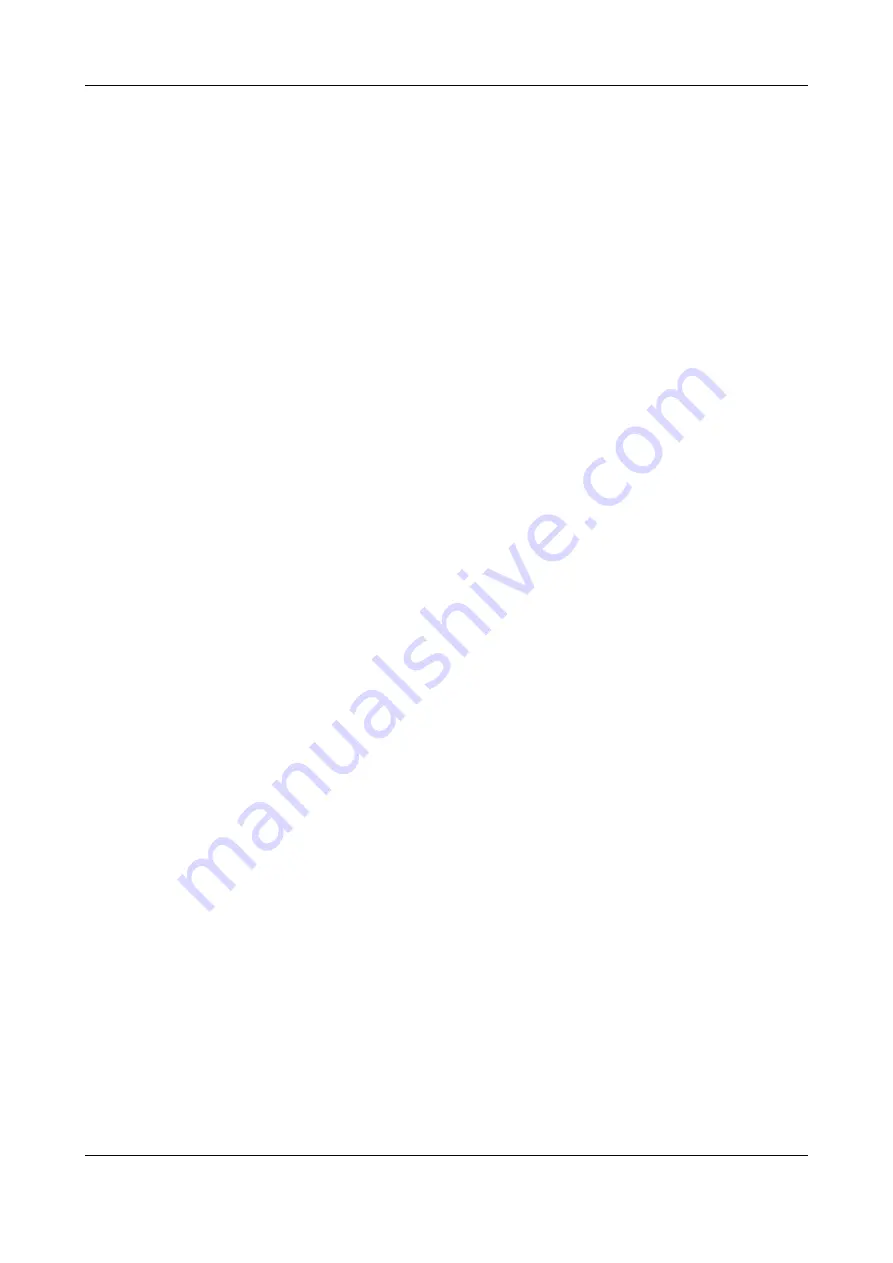
Functionality of the local Firmware
CAN-CBM-DP
Software Manual Rev. 2.0
8
2.2 User Data
The CAN-CBM-DP-module simulates a total of up to 300 bytes for the input direction and the output
direction in the current software implementation. From these 300 bytes a maximum of 244 bytes can
be selected for one data direction, otherwise the division into input bytes and output bytes is entirely
up to the user. (Examples: 150 input bytes and 150 output bytes, or 244 input bytes and 56 output
bytes).
One to eight bytes (16 bytes when using the communication window, see page 31) each are assigned
to a Tx-or Rx-identifier. The same identifier cannot be used as Tx-
and
Rx-identifier. The automatic
response to remote requests (RTR) on the CAN bus cannot be used, therefore.
2.3 Watchdog (Reaction Control)
The firmware can be run with activated or deactivated reaction control. It is recommendable, though,
to run it with activated reaction control.
2.4 Diagnose
The status of the LED displays and the DP-slave diagnose can be used for diagnose. The module
supports five module-specific diagnose bytes. The diagnose will be described in more detail on page
12.
2.5 Parameter Telegram (CAN Bit Rate)
In addition to the seven standard bytes of the configuration, the CAN-CBM-DP module supports three
module-specific bytes. Here, the DP master can change the CAN bit rate. Setting the bit rate by means
of the parameter telegram is described on page 23.
2.6 Global-Control Services (FREEZE, SYNC, UNSYNC)
The Global-Control services have not yet been implemented.
2.7 PROFIBUS-DP Profiles
The PROFIBUS-DP profiles are not being supported yet.