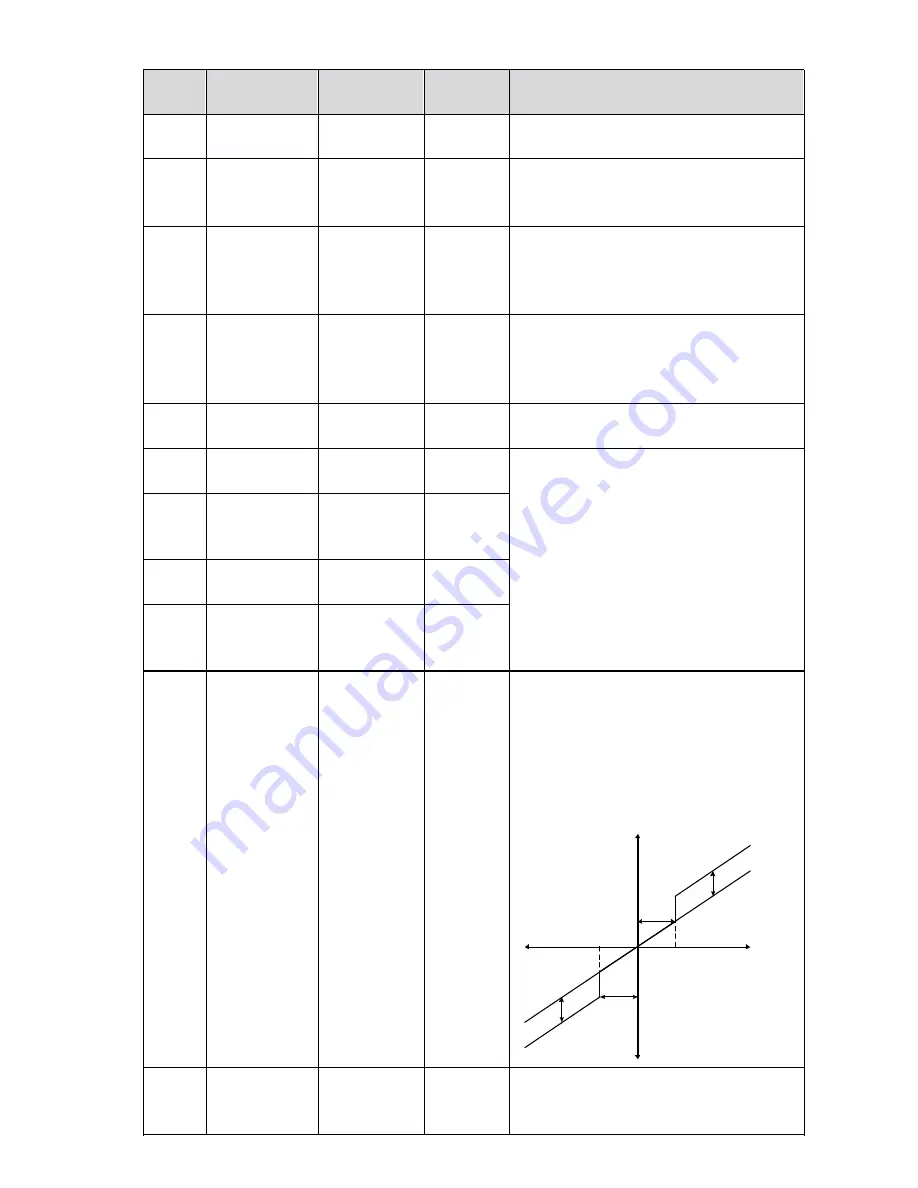
ProNet series AC servo system User’s manual V.1.08
- 140 -
Para
Para
Para
Para....
No.
No.
No.
No.
Description
Description
Description
Description
Setting
Setting
Setting
Setting
Validation
Validation
Validation
Validation
Control
Control
Control
Control
Mode
Mode
Mode
Mode
Func tion
Func tion
Func tion
Func tion and
and
and
and Meaning
Meaning
Meaning
Meaning
Pn102
Speed loop gain
Immediately
P
,
S
This parameter determines speed loop gain.
Unit: Hz
Pn103
Speed
loop
integral
time
constant
Immediately
P
,
S
Decreases the value of this parameter to shorten
positioning time and enhance speed response.
Unit: 0.1ms
Pn104
Position
loop
gain
Immediately
P
This parameter determines position loop gain.
Decreases this value to enhance servo rigidity,
but vibration will occur if the value is too large.
Unit: 1/s
Pn105
Torque reference
filter
time
constant
Immediately
P
,
S
,
T
Torque reference filter can eliminate or lighten
mechanical vibration. But incorrect setting will
result to mechanical vibration.
Unit:0.1ms
Pn106
Load inertia
percentage
Immediately
P
,
S
Setting value=(load inertia/rotor inertia)
100
×
Unit: %
Pn107
2nd speed loop
gain
Immediately
P
,
S
The meanings of these parameters are the same
as Pn102~Pn105.
These parameters are only needed to set when
two types of gain function are enabled.
Pn108
2nd speed loop
integral
time
constant
Immediately
P
,
S
Pn109
2nd position loop
gain
Immediately
P
Pn110
2nd
torque
reference
filter
time constant
Immediately
P
,
S
,
T
Pn111
Speed bias
Immediately
P
This parameter setting can shorten positioning
time. However, if it is too large or does not
cooperate with Pn111 correctly, vibration will
occur.
The relationship with speed reference, error
counter, positioning
error
is shown
in
the
following chart.
Spe e d re fe re nc e
Error c ounte r
P n 5 0 0
P n 5 0 0
P n 1 1 1
P n 1 1 1
Pn112
Feedforward
Immediately
P
It is used to set position feedforward. The
response speed is faster and position error is
less when this parameter setting is higher. Vibrati