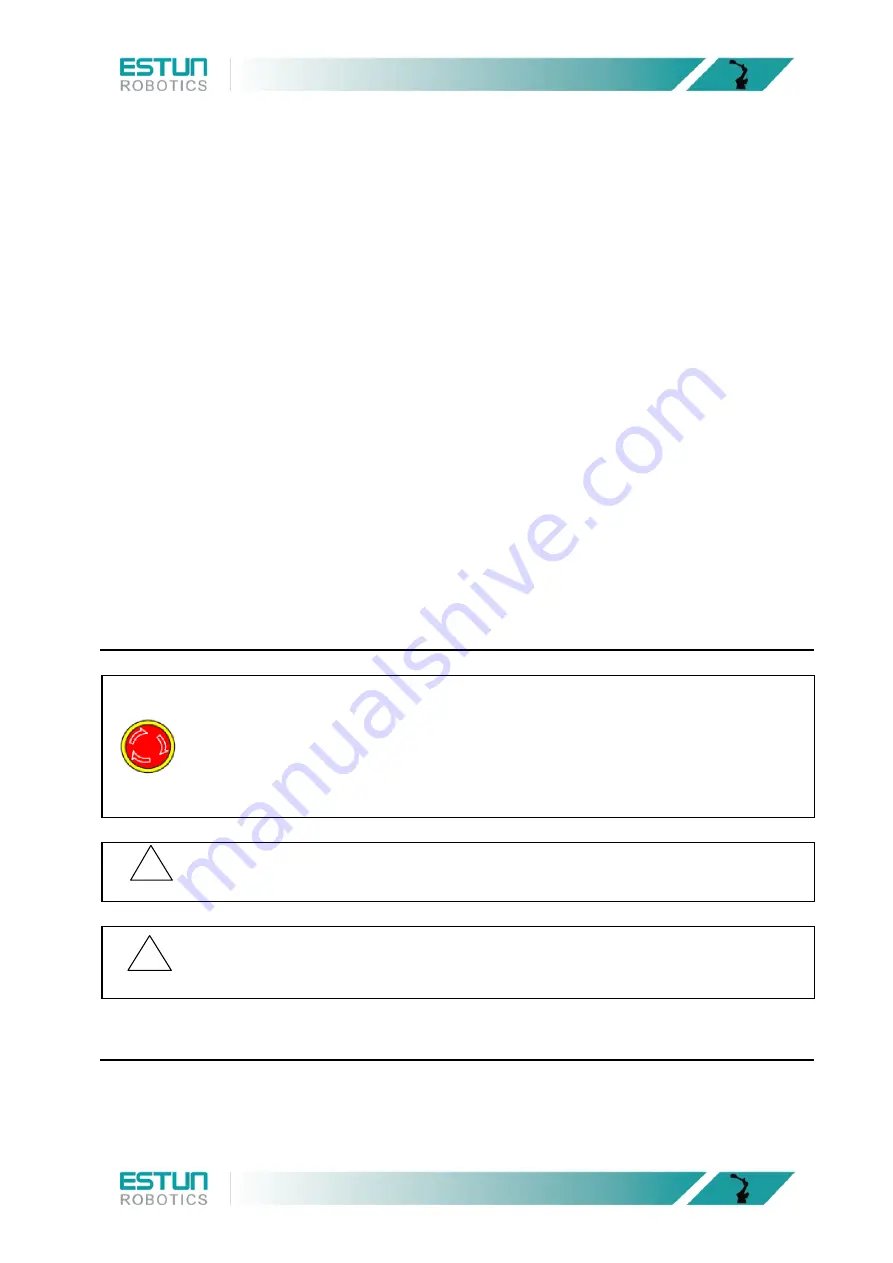
SAFETY
s-3
result in shortage bearing oil film and shorten the service life of joint. To avoid shortening the
service life of joint, please move the joint over 50 degrees for about 5 to 10 times per day
(10) Joint #3: if arm moving distance of up and down is shorter than 10mm, please move the joint over
half of the maximum motion range for about 50 times per day
(11) When the robot is operating at a low speed (about 5~20% of rated speed), continuous vibration (or
sympathetic vibration) may occur as the direction of arm and end effector load. The following
measures may reduce vibration caused by natural vibration frequency of arm.
Change operating speed
Change teaching point
Change the load of end effector
(12) Vibration of the front end of the arm may increase when J3-axis upper side or lower side is moving,
according to the weight and inertia of the grippers. This is due to an increased distance between
the end and head of the shaft, which leads to a change in inertia. Adjust speed etc. according to
item 11 when this vibration causes negative effect on robot operation.
(13) Do not touch Joint #3 and Joint #4 directly by hand during greasing and teaching. Touch Joint #3
and Joint #4 frequently may cause rust.
(14) When tear down the adhesive tape or seal on the oil paint surface of the robot and the cabinet, be
careful that damage to the paint may occur.
(15) The surface of the robot may be heated when operating with high payload or high speed. Pay
attention to second injury due to unintentionally touch of heated parts. Perform maintenance when
the robot is cooled down.
Emergency Stop
There may be several emergency stop buttons in a robot system to stop the robot
in case of emergencies. The red button, as shown in the left figure, shall be
mounted on the teach pendant. Certainly, the emergency buttons can be
mounted by your requirement.
Emergency stop button shall be located on the place where is easy to reach, so
that the buttons can be pressed down immediately in case of emergencies.
WARNING
!
Operators must be fully aware of the danger of electric shock from cables of
servo motor, gripper, chuck and other devices.
CAUTION
!
The Emergency Stop switch should be used to stop the Robot only in case of
emergencies. Avoid pressing the Emergency Stop switch unnecessarily while
the Robot is running normally.
Emergency Movement without Drive Power
When the system is placed in emergency mode, push the arm or joint of the Robot by hand as shown
below:
Arm #1 Push the arm by hand.
Arm #2 Push the arm by hand.
Summary of Contents for SCARA ER Series
Page 1: ......
Page 2: ...ESTUN SCARA Robot MECHANICAL UNIT OPERATOR S MANUAL M 0601EN 03...
Page 61: ...49...