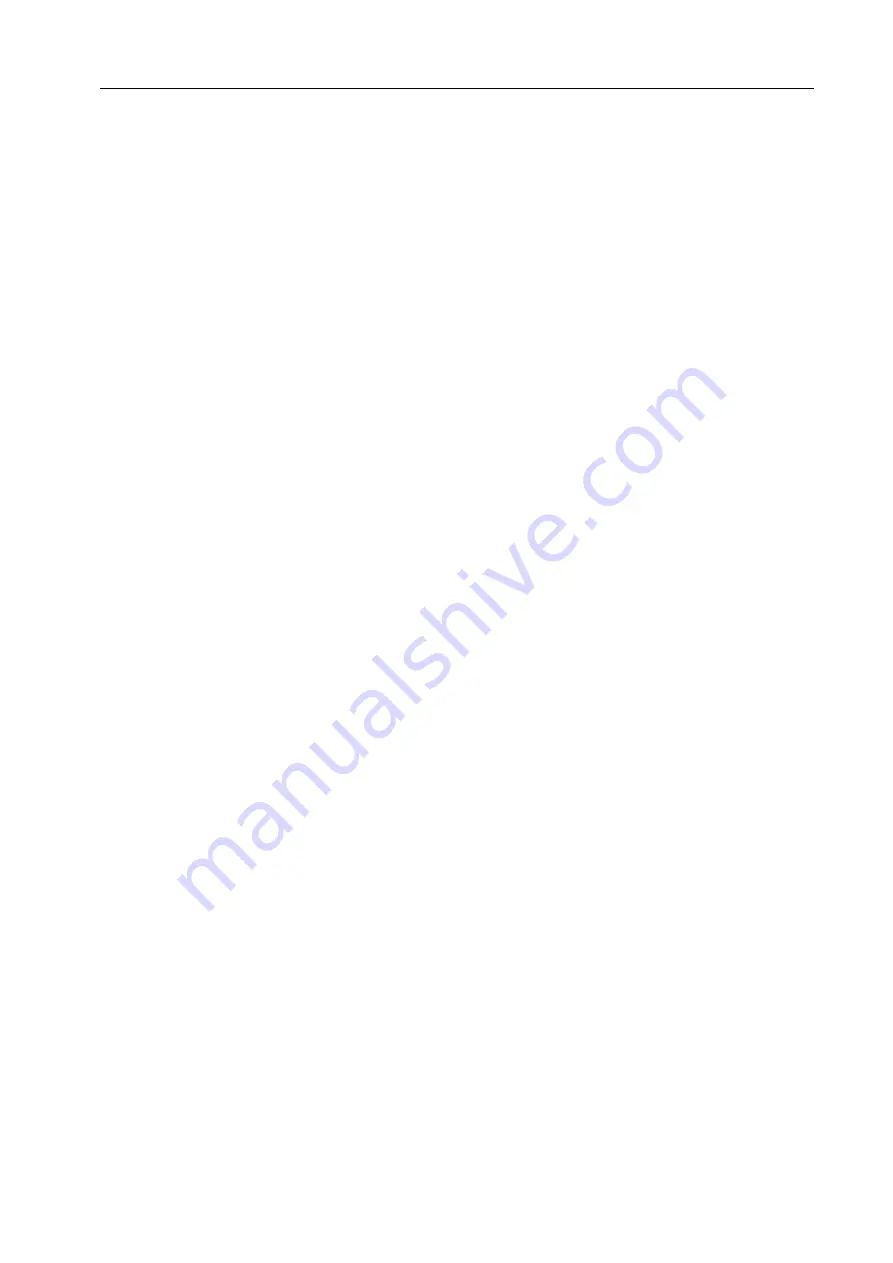
TRIO SCARA Robot Mechanical Unit Operator's Manual
Document Version: V1.8
© 2022 TRIO MOTION TECHNOLOGY
All right reserved.
31
3.1.3.
Layouts
When you operate the robot with an end effector, the end effector may interfere with the Robot
because of the outer diameter of the end effector, the size of the work piece, or the position of the
arms. When designing your system layout, pay attention to the interference area of the end effector.