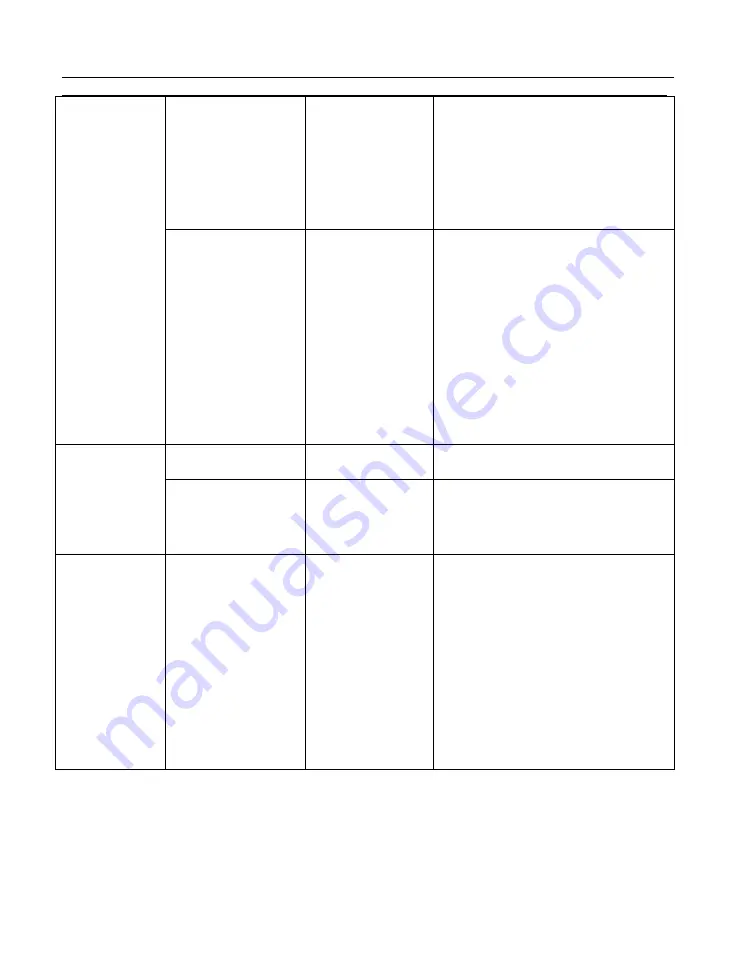
SD20 series
331
to chapter 4.
No position command is input
1. Whether DI function 2 ( forward
torque limit) or DI function 3 (reverse
torque limit) is used.
2. Whether DI function 11 (common
pulse prohibited) is used.
3. Check whether Po374 is set correctly.
Servo motor is
galloping.
Encoder cable fault
1.
Check whether Lo-04 value is
correct when motor rotates 1
revolution.
2.
Check whether servo drive trips into
AL-17
U/V/W motor cable fault.
1.
Check whether U/V/W wiring is
correct.
2.
If wiring is correct, please study
motor angle referring to chapter 7.2.
Rotation is not
smooth at low
speed.
Low speed rotation is
not smooth.
Gain is not set
properly.
Adjust gain according to chapter 7.
Motor shaft vibrates
side to side.
Rotation inertia ratio
(Po013) is too high.
If servo drive runs safely, please
recognize inertia again according to
chapter 7.3.
Adjust gain according chapter 7.
Normally
running
Location is not
accurate.
There is position
error.
Pulse received by Lo-08 is not same
as the one sent by PC/PLC..
1.
Check
whether
servo
drive
grounding is reliable.
2.
Check whether signal cable is
twisted-pair shield cable, whether
shielding layer is connected to
housing correctly.
Check whether motor shaft coupler
is locked tightly.
Check whether device has
vibration. Adjust the gain according
to chapter 7.
Summary of Contents for SD20-G Series
Page 35: ...SD20 G Series 35 M3 structure Fig 3 1 5 Servo drive structure 3...
Page 36: ...SD20 G Series 36 ML3 structure 118 5 5 7 5 93 297 8 223 118 93 0 5 12 5 7 5 4 M4...
Page 38: ...SD20 G Series 38 M4 structure Approx mass 10 365 kg Fig 3 1 7 Servo drive structure 5...
Page 39: ...SD20 G Series 39 M5 structure Approx msaa 11 1Kg Fig 3 1 8 Servo drive structure 6...
Page 40: ...SD20 G Series 40 M6 structure Approx mass 17 4Kg Fig 3 1 9 Servo drive structure 7...
Page 182: ...SD20 G Series 182 Fig 6 4 44SD20E Cam internal frameworkdiagram...