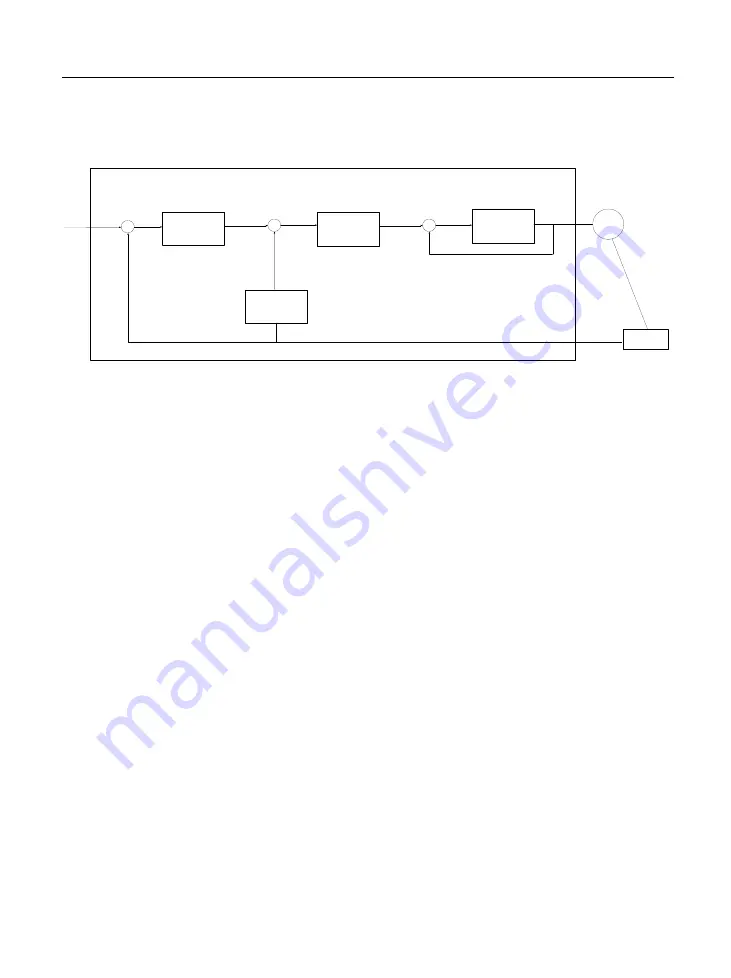
SD20-G Series
94
VI Run
Servo system includes servo drive, servo motor and encoder.
Position loop
control
Speed loop
control
Speed
calculation
X
Servo drive
Command
input
+
X
+
-
Speed
feedback
-
Position feedback
X
+
-
M
Motor
Encoder
Current
feedback
Current loop
control
Based on the command modes and running characteristics, servo drives supports three running mode, position
control, speed control and torque control.
In the position control mode, motor target position is confirmed by position command total numbers. The
position control mode strictly controls the position and speed, and is often used in the positioning device. It is
the most commonly used mode of the servo drive, applicable to the mechanical arm, mounter, engraving and
milling machine, and computer numerical control (CNC) machine tool.
In the speed control mode, the speed is controlled by AI setting, DI setting, or communication setting. It is often
used in scenarios with constant speed. For example, for the analog engraving and milling machine, the host
controller uses the position mode, and the servo drive uses the speed control mode.
In the torque control mode, the torque is changed by changing the analog setting or the address value by means
of communication. This mode is mainly applied to the winding and unwinding devices with strict tension
requirements.
Summary of Contents for SD20-G Series
Page 35: ...SD20 G Series 35 M3 structure Fig 3 1 5 Servo drive structure 3...
Page 36: ...SD20 G Series 36 ML3 structure 118 5 5 7 5 93 297 8 223 118 93 0 5 12 5 7 5 4 M4...
Page 38: ...SD20 G Series 38 M4 structure Approx mass 10 365 kg Fig 3 1 7 Servo drive structure 5...
Page 39: ...SD20 G Series 39 M5 structure Approx msaa 11 1Kg Fig 3 1 8 Servo drive structure 6...
Page 40: ...SD20 G Series 40 M6 structure Approx mass 17 4Kg Fig 3 1 9 Servo drive structure 7...
Page 182: ...SD20 G Series 182 Fig 6 4 44SD20E Cam internal frameworkdiagram...