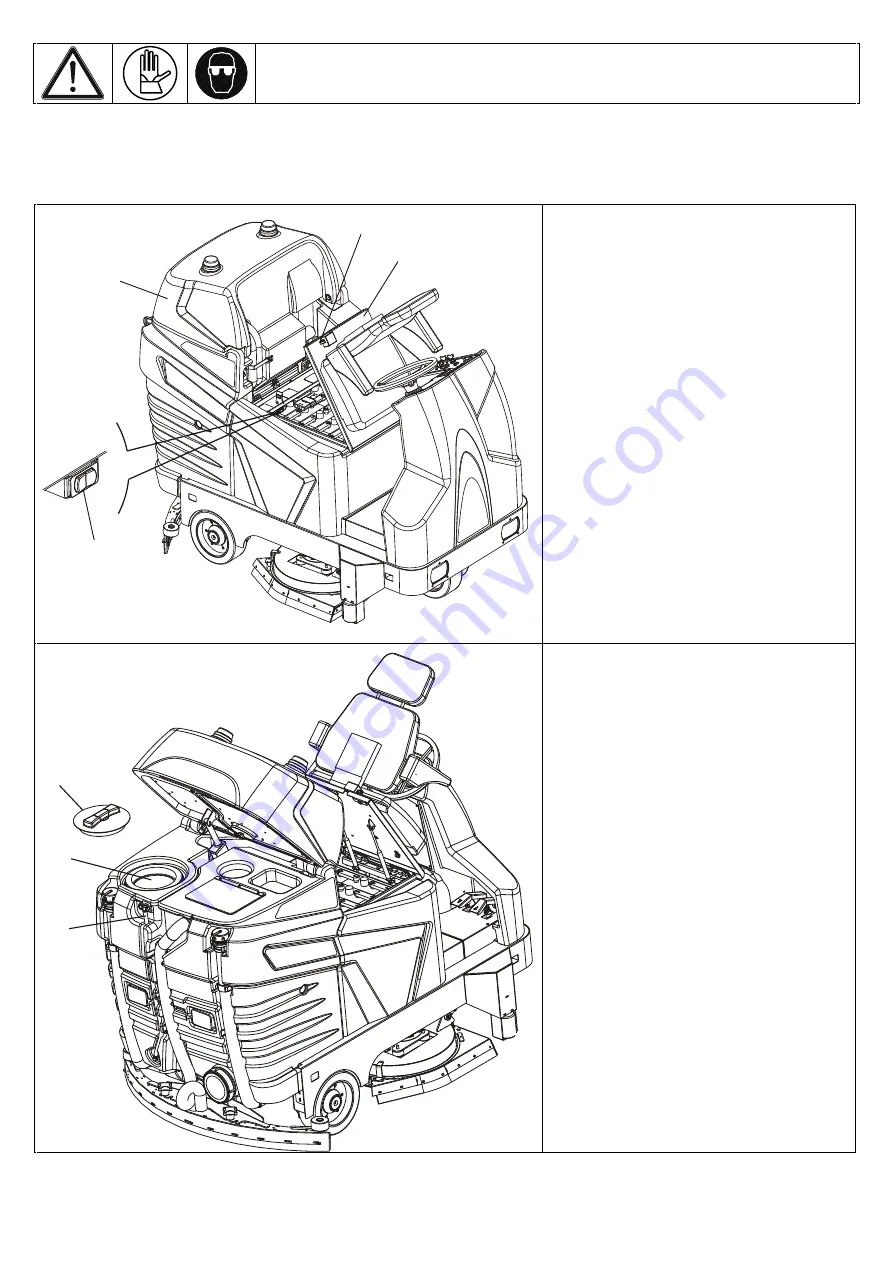
21
FILLING THE DETERGENT SOLUTION TANK
The solution tank can only be filled with clean water when the detergent dosing system is used, or with a mix of water
and detergent suited to the type of floor and to the conditions of dirt to be washed and a product suitable for reducing
foam.
1
2
3
4
Stop the machine on a flat floor area,
turn off the ignition key and engage the
brake;
Open the seat hood (pos. 2) by releasing
the safety catch (pos.6);
Open the tank lid (pos.4) by means of
the button (pos.3) which controls an
electric actuator.
1
2
3
Loosen the cap (pos. 1) and remove it;
Only fill the tank with clean water, with
a temperature below 40°C, in the event
of the detergent dosing system being
used.
In the event of the detergent dosing
device not being used:
• Pour the detergent solution into the
tank directly. Look at the instructions on
the package to determine how much
detergent solution to use, how to mix the
solution and what safety precautions to
take before using the product. Make sure
to use low-foaming liquid detergents or
appropriate products to cut-down foam.
• After pouring the detergent solution,
fill the tank with water. Make use the
water used to fill the tank does not
exceed 40°C.
WARNING:
DO
NOT
POUR
INFLAMMABLE LIQUIDS INTO
THE TANK
• After filling the tank, place the
device (pos 1) The level of the water or
of the solution in the tank can be seen
through the level pipe (pos. 3).