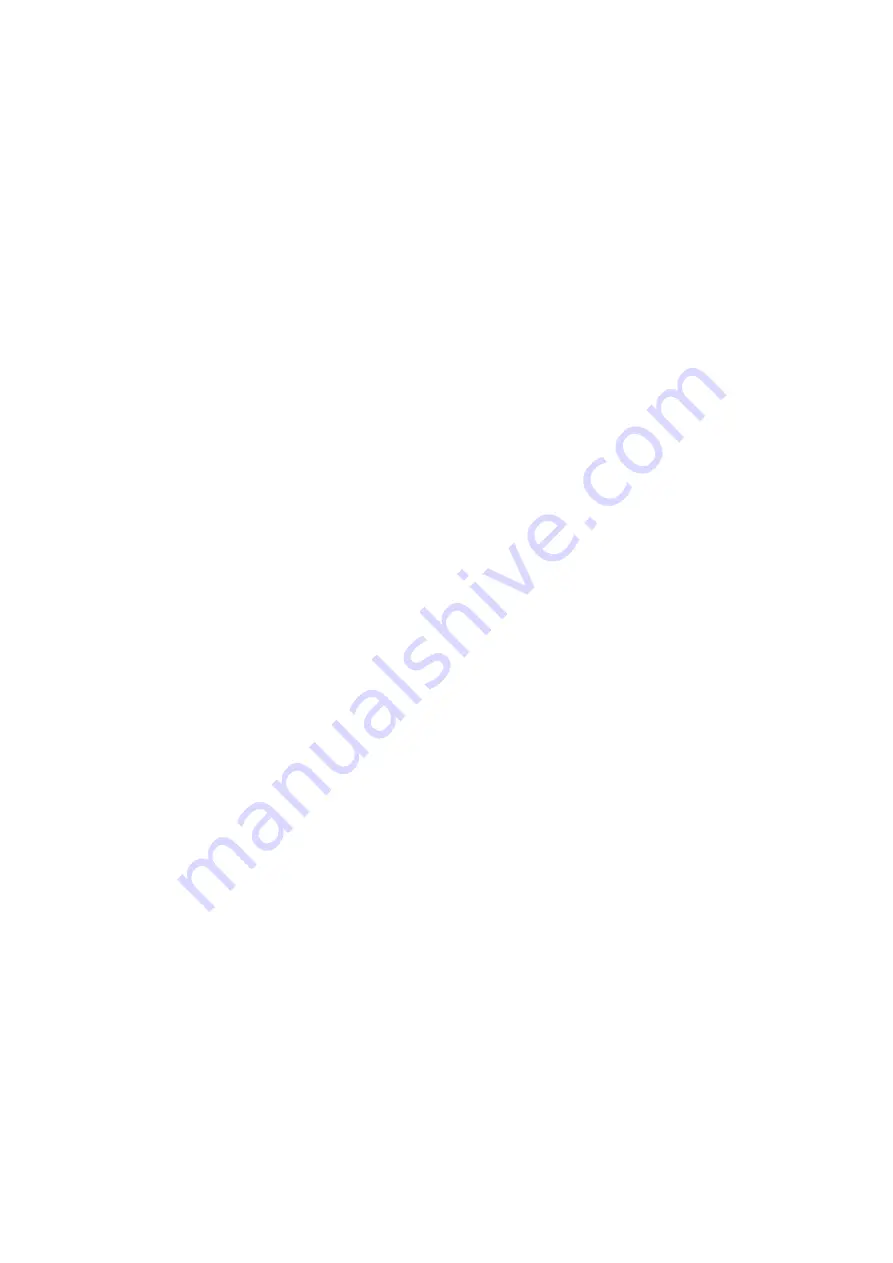
28
8.
Apply a regular pressure while drilling. The drilling performance does not improve by putting
more pressure on the machine. Too much pressure will overload the motor and your annular
cutter will be worn sooner;
A continuous, non-discoloured iron swarf is a sign of correct drilling speed and a well-
cooled, sharp cutter. Let the cutter do the job and give it time to cut the metal!
9.
Adjust the oil supply when necessary;
10.
Apply less pressure when the drill cuts through the material. The slug will be pushed out of
the cutter by the pilot pin;
11.
Move the ratchet feed handle back until the output shaft is in its highest position and switch
off the motor unit;
12.
Remove the burrs, metal chips and clean the cutter and surface without getting injuries;
13.
To remove the annular cutter, hold the cutter while turning the lock ring in counter clockwise
direction, and pull down the cutter. After drilling the cutter can be hot, resulting in a tighter
fitment inside the output shaft. If this makes the cutter hard to remove, wait a few minutes
for the cutter to cool down and try again.
Caution
: The metal slug can be sharp and very hot!
5.2 Twist drills
1.
Only use Weldon shank twist drills.
For fitment and removal, follow instructions as provided in paragraph 5.1 Annular cutters.
Summary of Contents for ECO.36+
Page 15: ...15 image 3 6...
Page 33: ...33 8 Exploded views spare parts list 8 1 Exploded views...
Page 34: ...34...
Page 35: ...35...
Page 38: ...38 8 3 Wiring diagram...