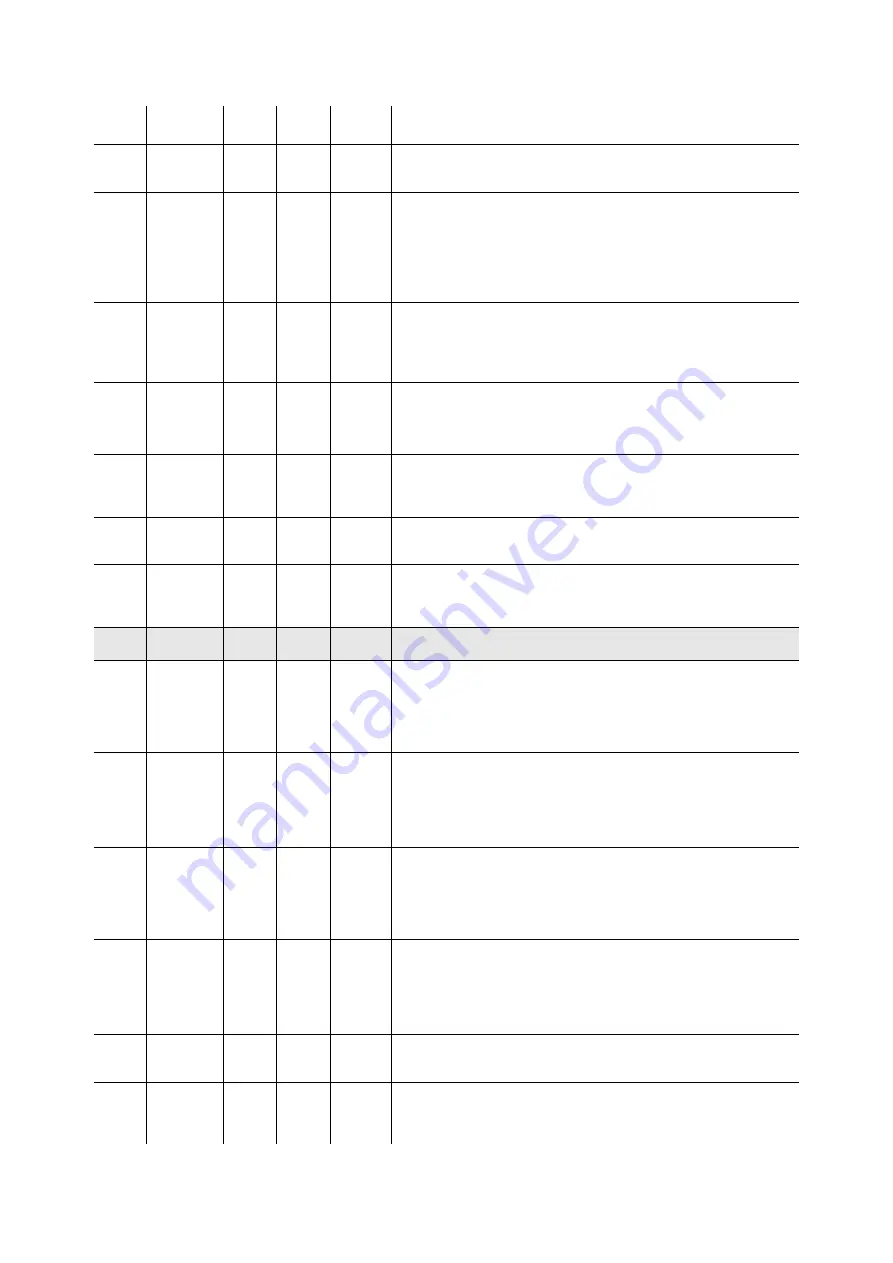
EVCO S.p.A.
Vcolor 869/879
| Installer manual ver. 2.2 | Code 144VC869E214
page 73 of 94
or provided the door switch input is on and that parameter
i0 is set to a value other than 0).
d2
2
-50
99
°C/°F
(1)
Evaporator temperature to end defrosting. See also parameter
d3
d3
30
0
99
min
If the evaporator probe is not present (P4=0), it sets the defrost
duration.
If the evaporator probe is present (P4=1), it sets the maximum
defrost duration. See also parameter d2
0 = defrost is never activated.
d4
0
0
1
- - - -
Enable defrost at the start of blast chilling and of blast-freezing
0 = no
1 = yes
d5
30
0
99
min
Defrost delay from the beginning of conservation
0 = defrost will be activated once the time set by d0 has
elapsed.
d7
2
0
15
min
Drip time after a defrost, in which the compressor and the
evaporator fan are switched off and the defrost output is
deactivated.
d15
0
0
99
min
Minimum consecutive compressor-on duration for starting hot
gas defrost, if d1 is set to 1
d16
0
0
99
min
Pre-drip time if d1 is set to 1 (hot gas defrost), in which the
compressor and the evaporator fan are off and the defrost output
remains activate.
PAR.
DEFAULT
MIN.
MAX.
U.M.
TEMPERATURE ALARMS
A1
10
0
99
°C/°F
(1)
Cabinet temperature below which the minimum temperature
alarm is activated (in relation to the working set point, i.e. “r10–
A1” during conservation after blast chilling and “r11–A1” during
conservation after blast-freezing; (“
LOW TEMPERATURE
”
code). See also parameter A11
A2
1
0
1
- - - -
Enable minimum temperature alarm (“
LOW TEMPERATURE
”
code):
0 = no
1 = yes
A4
10
0
99
°C/°F
(1)
Cabinet temperature above which the maximum temperature
alarm is activated (relating to the working set point, i.e. “r10+A4”
during conservation after blast chilling and “r11+A4” during
conservation after blast-freezing (“
HIGH TEMPERATURE
”
code). See also parameter A11 (4)
A5
1
0
1
- - - -
Enable maximum temperature alarm (“
HIGH TEMPERATURE
”
code):
0
=
no
1
=
yes
A7
15
0
240
min
Temperature alarm delay (“
HIGH TEMPERATURE
” code and
“
LOW TEMPERATURE
” code)
A8
15
0
240
min
Maximum temperature alarm delay (“
HIGH TEMPERATURE
”
code) from the end of the evaporator fan-off time and from the
beginning of conservation.