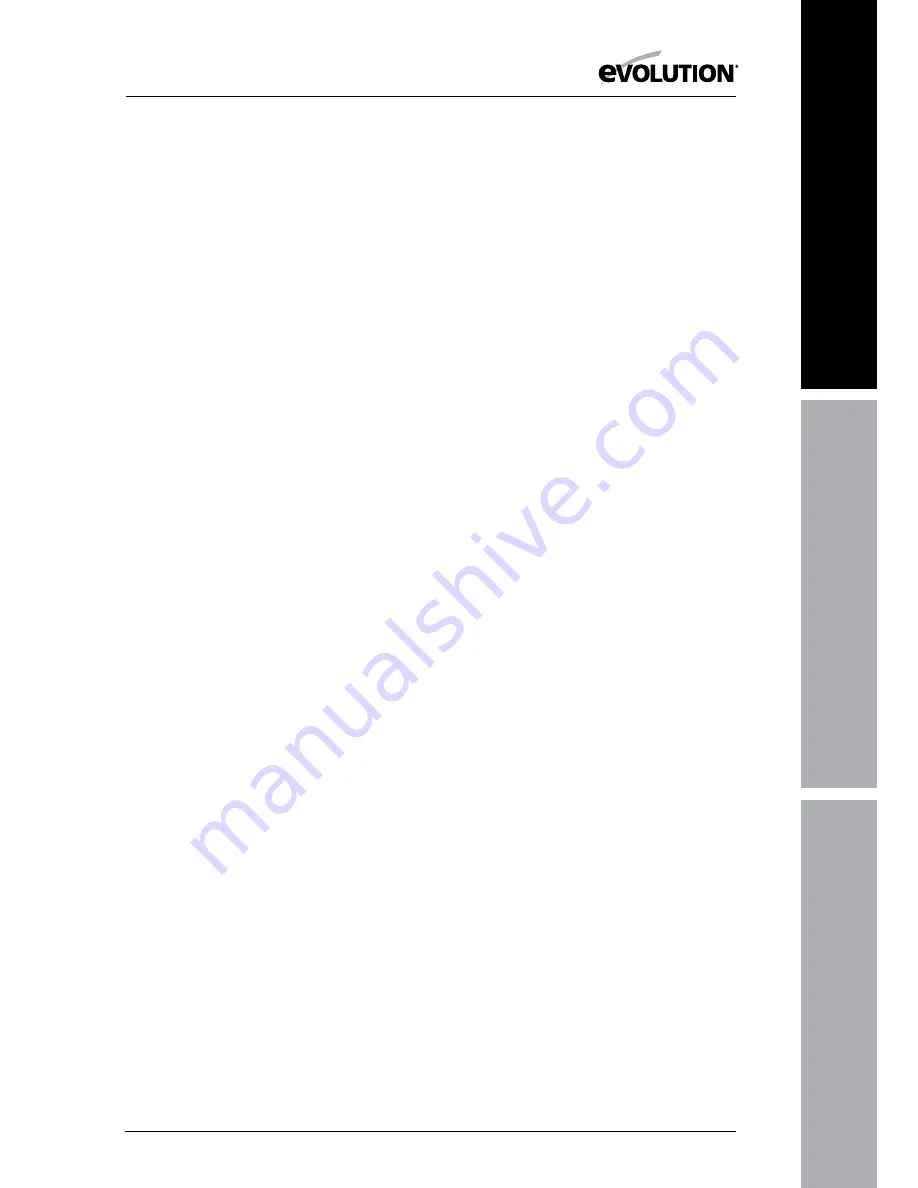
7
www.evolutionpowertools.com
EN
ES
FR
Note:
The vibration measurement was made
under standard conditions in accordance with:
BS EN 61029-1:2009
The declared vibration total value has been
measured in accordance with a standard test
method and may be used for comparing one
tool with another.
The declared vibration total value may also be
used in a preliminary assessment of exposure.
VIBrATION
wArNING:
When using this machine
the operator can be exposed to high levels of
vibration transmitted to the hand and arm. It
is possible that the operator could develop
“Vibration white finger disease” (Raynaud
syndrome). This condition can reduce the
sensitivity of the hand to temperature as well
as producing general numbness. Prolonged
or regular users of this machine should
monitor the condition of their hands and
fingers closely. If any of the symptoms become
evident, seek immediate medical advice.
• The measurement and assessment of
human exposure to hand-transmitted
vibration in the workplace is given in:
BS EN ISO 5349-1:2001 and
BS EN ISO 5349-2:2002
• Many factors can influence the actual
vibration level during operation e.g. the
work surfaces condition and orientation
and the type and condition of the machine
being used. Before each use, such factors
should be assessed, and where possible
appropriate working practices adopted.
Managing these factors can help reduce
the effects of vibration:
handling
• Handle the machine with care, allowing
the machine to do the work.
• Avoid using excessive physical effort on
any of the machine’s controls.
• Consider your security and stability, and
the orientation of the machine during use.
work Surface
• Consider the work surface material;
its condition, density, strength,
rigidity and orientation.
wArNING:
The vibration emission during
actual use of the power tool can differ from the
declared total value depending on the ways
in which the tool is used. The need to identify
safety measures and to protect the operator
are based on an estimation of exposure in the
actual conditions of use (taking account of all
parts of the operating cycle, such as the times
the tool is switched off, when it is running idle,
in addition to trigger time).
LABELS & SYMBOLS
wArNING:
Do not operate this machine
if warning and/or instruction labels are
missing or damaged. Contact Evolution
Power Tools for replacement labels.
Note:
All or some of the following symbols
may appear in the manual or on the product.