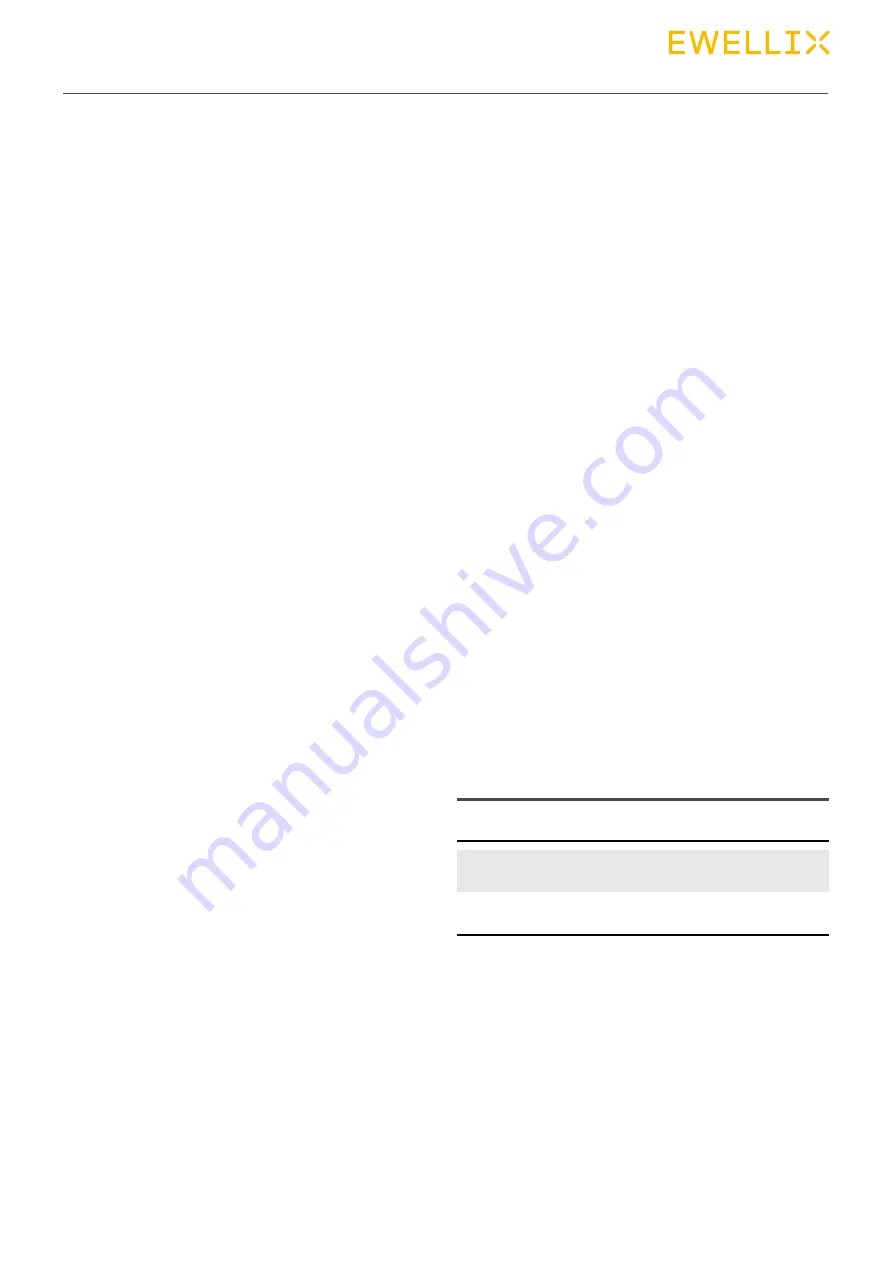
5
5
2 .0 S afety
2.0 Safety
This section provides safety aspects supplementary to the
safety aspects described in the relevant operating manuals
of the included devices. Failure to comply with the guide-
lines and safety instructions contained in this manual may
result in serious hazards that could cause possible serious
injury or death, or damage to the device or equipment.
The listed safety aspects must be reviewed and taken into
account in the final application risk assessment prior to the
use of LIFTKIT.
2.1 Intended use
LIFTKIT has been designed and built for the intended use as
described in the operating manual of the pillar, with addi-
tional intended use defined as
• Lifting of a robot to extend its operating range.
Any use that extends beyond the intended use or a use dif-
ferent than the one described above is deemed misuse.
Any type of claims resulting from damage caused by misuse
are excluded.
2.2 Safety elements
The LIFTKIT has a range of safety elements built in to allow
its integration into a robot application, including safety relay
certified according ISO 13849-1, allowing STO up to PLe,
Cat. 4
2.3 Application notes
• Integration with an emergency-stop is required for its in-
tended use.
• Install emergency stop functions for the pillar and integrate
them into the safety chain of the complete system prior to
operating LIFTKIT.
• The emergency stop function has to be connected in such
a way that a disruption of the power supply or the activa-
tion of the power supply after a power disruption cannot
cause a hazardous situation for persons and objects.
• The emergency-stop systems must always be freely ac-
cessible.
2.4 Potential risks
The following risks during LIFTKIT operation have to be con-
sidered in an application specific risk assessment
• The pillar does not detect an impact automatically and
does not stop movement upon impact. This can lead to:
-
Crushing of a person or an object in the path of the pillar,
causing serious injury or death or property damage.
-
Dynamic impact to a person or an object causing serious
injury or death or property damage.
• It is possible that the pillar movement does not stop at the
desired position
-
Movement of the robot can occur at a different position
than intended, causing significant serious injury or death
or property damage.
2.5 E-Stop setup and
behavior
The LIFTKIT has two e-stop mechanisms. One is integrated
into the SBOX, the other directly into the SCU. The SCU
mechanism is software controlled and is much faster, but
only the SBOX mechanism guarantees an STO up to PLe,
Cat.4. It is recommended to integrate both mechanism into
the safety system. See the following table for comparison:
E-Stop
mechanism
Performance level
ISO 13489-1
Stop distance Stop time
SCU
Not rated
18 mm
200 ms
SBOX
Up to PLe, Cat. 4
28 mm
750 ms