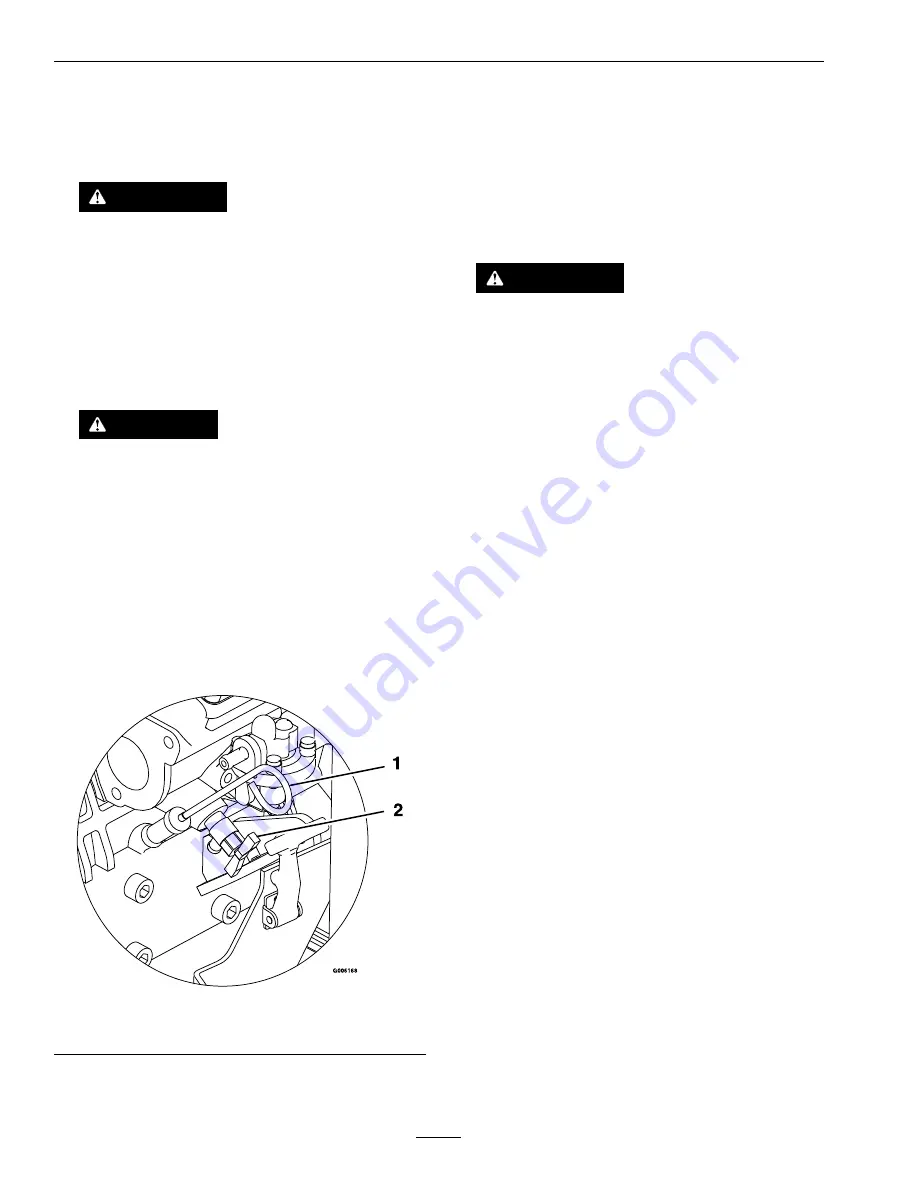
Maintenance
2. Unhook seat latch, tilt seat up and tilt hood
forward to gain access to the cooling area. Do
Not raise radiator, as it may not fully drain in that
position.
WARNING
Engine coolant is hot and pressurized and
radiator and surrounding parts are hot. Spray
or steam from hot, pressurized liquid in the
engine cooling system and touching a hot
radiator may cause severe burns.
Allow the engine to cool completely before
removing the radiator cap or servicing any
component of the cooling system.
CAUTION
Engine coolant is toxic. Swallowing coolant
can cause poisoning.
•
Do Not swallow.
•
Keep out of reach of children and pets.
3. Drain coolant when engine is cool. Coolant may
be drained from the radiator by removing the
drain plug in the right rear corner. The engine
block may be drained by removing the rear
radiator hose and/or by opening the drain cock
on the right-hand side of the engine block (see
Figure 22).
Figure 22
1.
Oil dipstick
2.
Drain cock
4. Reinstall all drain plugs and hoses and tighten
drain cock.
5. Fill radiator with a 50/50 mix of water and
Havoline
™
coolant as specified in the
Check
Engine Coolant Level
Section, allowing some
room (approximately 1/2 inch (12.7 mm)) for
expansion. Add 50/50 coolant mix to overflow
bottle on the left side of the engine as required
to bring the level up to the indicator line on the
bottle.
WARNING
Engine compartment contains open belt
drives, fans, and other rotating components
that can cause injury. Fingers, hands, loose
clothing, or jewelry can get caught by the
rotating fan and drive shaft.
•
Do Not operate machine without the
covers in place.
•
Keep fingers, hands, and clothing clear of
rotating components.
•
Shut off engine, wait for moving parts to
stop, engage parking brake and remove
key, before performing maintenance.
6. With the cap off the radiator, tilt hood closed and
put the seat down. Start the engine as stated in
the Operating Instructions Section. Return the
seat up and hood forward to the open position.
7. Operate engine until the engine thermostat opens
and coolant is circulating through the radiator
core. As air is purged from the engine block and
the coolant level drops, add additional coolant to
the radiator.
8. When the radiator is completely full and no
additional coolant can be added, continue running
and install the radiator cap. Make sure that the
cap is completely seated by pressing down firmly
while turning until the cap stops. Once the cap is
installed, the engine may be stopped.
Check Spark Arrester
(if equipped)
Service Interval: Every 50 hours
44