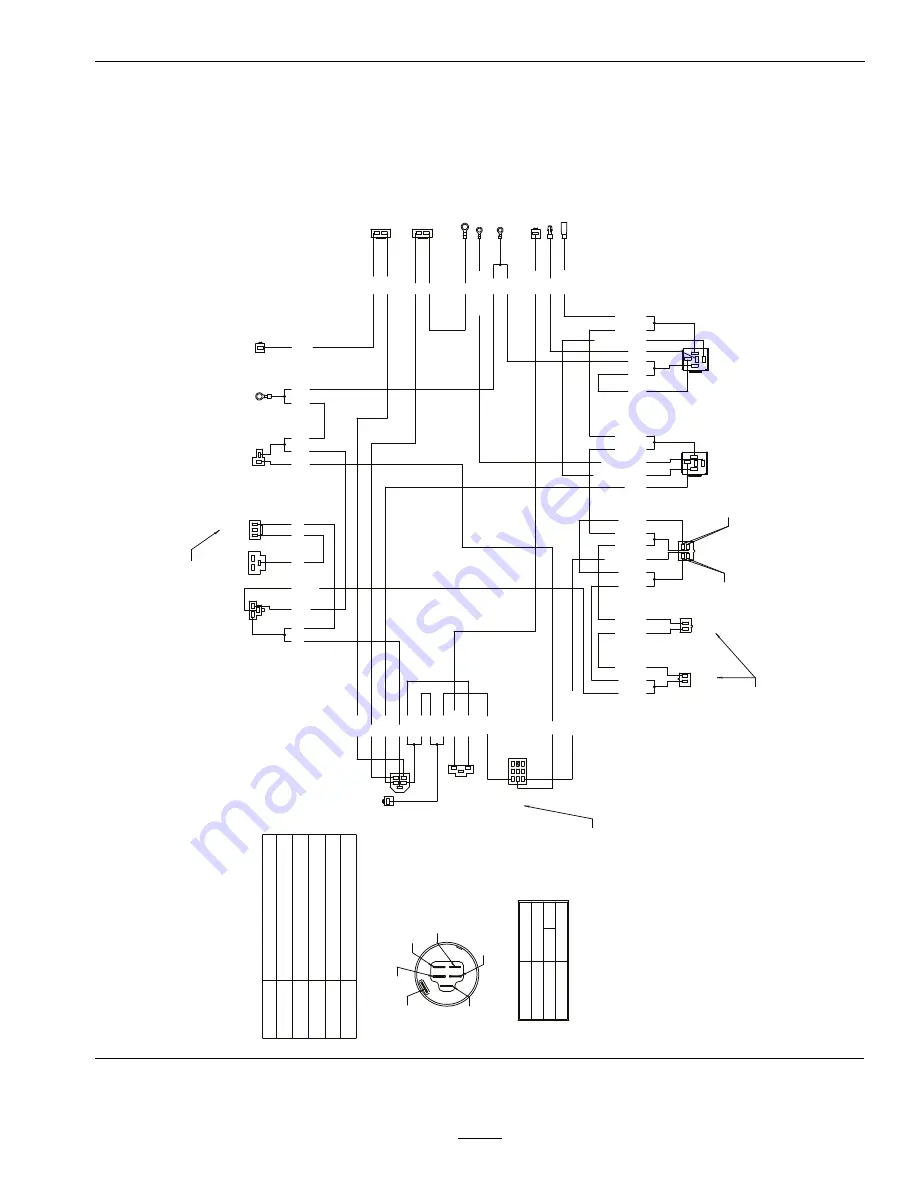
Schematics
Schematics
Electrical Diagram
TAN
TAN
BL
AC
K
DK. G
REE
N
BLACK
GREY
ORANGE
ORANGE
ORANGE
ORANGE
TAN
YELL
OW
RED
VIOLET
ORANGE
PINK/BL
ACK STRIPE
ORANGE
DK BLUE
BLAC
K
N
O
TE
:
CONNEC
TORS
VIEWED F
ROM
WIRE EN
D.
TERMINAL CONNECTIONS
IGNITION SWITCH
B + I + A
NONE
X +
Y
CIRCUIT "MAKE"
B + I + S
2.
R
UN
1.
O
FF
POSITION
3.
S
TA
RT
ORANGE/BLK STIPE
WHITE
BLACK
BLACK
ORANGE/BLK STRIPE
DK. G
REE
N/W
HT
STR
IPE
DK. G
REE
N/W
HT
STR
IPE
YELLOW
DK. G
REE
N
DK. G
REE
N
DK. G
REE
N
DK. G
REE
N
DK. G
REE
N
PINK/BLK STRIPE
DK. G
REE
N
LT. GREEN
LT. GREEN
LT. BLUE
LT. BLUE
LT. BLUE
LT. BLUE
LT. BLUE
VIOLET
GREY
TAN
LT. BLUE
TAN
TAN
BLAC
K
BLAC
K
BLAC
K
BLAC
K
VIOLET
VIOLET
RED
RED
RED
BL
AC
K
DK
. B
LU
E
WHITE
DK GREEN
SE
AT DEL
AY
MODULE CONT
ROL
SE
AT
SWITCH
ELECTRIC
CLUTCH
(P
TO)
G
ROUND
FUSE
FUSE
ST
A
RTER
SOLENOID
LH M
O
TI
O
N
CONT
ROL
RH M
O
TI
O
N
CONT
ROL
BRAKE
ST
A
RT
REL
AY
IGNITION
SWITCH
HOUR
METER
P
TO
SWITCH
SE
AT
D
EL
AY
MODULE INPUT
KILL
REL
AY
ENGINE KILL
FUEL SOLENOID
OIL PRESSURE
RECTIFIER/
REGUL
AT
OR
TERMINAL A
V
O
LT
A
GE REGUL
AT
OR
TERMINAL B
B
ATTE
R
Y
TERMINAL I HOUR METER
, P
TO SWITCH
TERMINAL S S
TA
R
T REL
AY
TERMINAL X SE
AT DEL
AY
TERMINAL
Y HOUR METER
, P
TO SWITCH
TERMINAL X
TERMINAL
Y
TERMINAL A
TERMINAL B
TERMINAL S
TERMINAL I
SWITCH IN - ORANGE
TO PINK/BL
AC
K
SWITCH OUT - ORANGE
TO GREY
OPEN
W
IT
H
BRAKE ENG
AGED
CLOSED
W
IT
H
BRAKE ENG
AG
ED
BO
TH M
OTION CONT
ROL SWITCHES
ARE CLOSED
WITH CONT
ROL LEVERS
IN NEUTRAL LOCK POSITION
SWITCHES ARE CLOSED
W
IT
H
O
PE
R
AT
OR
IN SE
AT
A
N
D
M
AC
H
IN
E
LE
VE
L
G007567
33
Summary of Contents for Phazer PHZ19KA343
Page 1: ...PHAZER For Serial Nos 790 000 Higher Part No 4500 335 Rev A ...
Page 11: ...Safety 109 2463 109 2465 109 2467 109 2490 109 2539 109 2862 109 2992 116 0950 11 ...
Page 12: ...Safety 109 2494 12 ...
Page 36: ...Notes 36 ...
Page 37: ...Service Record Date Description of Work Done Service Done By 37 ...
Page 38: ...38 ...
Page 39: ...39 ...