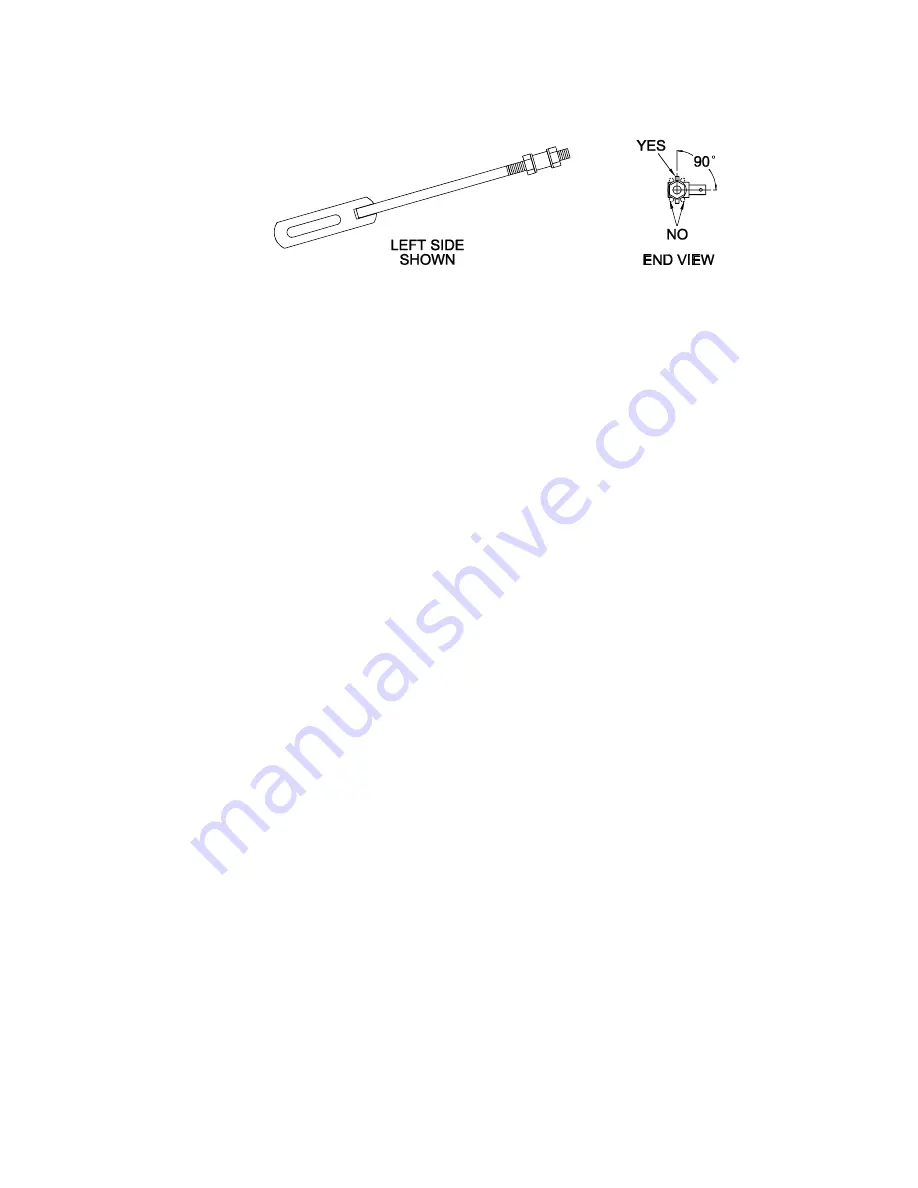
- 36 -
neutral, until left wheel stops rotating forward. Turn the rear nut an
additional 1/2 turn and tighten the front nut making sure not to put a bind
on the linkage. Make sure flat part of linkage is perpendicular to pin part
of swivel. See Figure 15.
FIGURE 15
HYDRO CONTROL LINK/SWIVEL ADJUSTMENT
After adjusting the left hydro control linkage, move the speed control lever
to the mid-speed position and then back to the neutral position. Recheck
the left drive wheel rotation to see if further adjustment is necessary - be
sure the speed control lever is in the neutral position.
If inconsistent neutral occurs, check to be sure both springs are
properly tightened on the speed control lever under the console -
especially the rear pivot spring.
Repeat above adjustments if necessary.
3. Place the speed control lever in neutral. Adjust the right side linkage by
turning the quick track knob counter-clockwise until the tire begins to
rotate forward. Begin to retighten the knob clockwise about 1/4 turn at a
time, stopping to move the speed control forward and back to neutral.
Recheck the drive wheel rotation to see if further adjustment is necessary.
4. The spring that keeps tension on the knob should normally not need
adjustment. However if adjustment is needed, adjust to where length of
spring is about 1” between the washers. Adjust spring length by turning
nut at front of spring.
d)
Drive Lever Linkage Adjustment
1. With rear of machine still on jack stands and engine running at full
throttle, move the speed control lever to the midway position. Move the
respective drive lever upward until it reaches the
neutral
position and
engage neutral lock latches. See Figure 16. If the tire rotates in either
direction, the length of the drive lever link will need to be adjusted.
2.
For Standard Pistol Grip Handles:
Adjust the linkage length by
releasing the drive lever and removing clevis pin and rotating the linkage
in the lower swivel. Lengthen the linkage if the tire is turning in reverse
and shorten the linkage if the tire is creeping forward. Rotate the linkage
several turns if the tire is rotating fairly fast. But as the adjustment gets
closer, adjust the linkage in 1/2 turn increments. Release and re-engage
neutral lock latch checking that the tire stops. Continue this process until
the tire is at a dead stop. Replace the hairpin back into each clevis pin.
For ECS Handles:
Adjust the linkage length by loosening the jam nuts at
both ends of the linkage and rotating the linkage in the ball joints.
Lengthen the linkage if the tire is turning in reverse and shorten the
linkage if the tire is creeping forward. Tighten the jam nuts at both ends.
Release and re-engage the neutral lock latch checking that the tire stops.
Continue this process until the tire is at a dead stop.
Summary of Contents for Turf Tracer HP TT3615KA
Page 1: ......
Page 45: ... 40 8 WIRING DIAGRAMS ...
Page 46: ... 41 9 HYDRAULIC DIAGRAM ...
Page 49: ... 44 NOTES ...
Page 50: ... 45 SERVICE RECORD Date Description of Work Done Service Done By ...