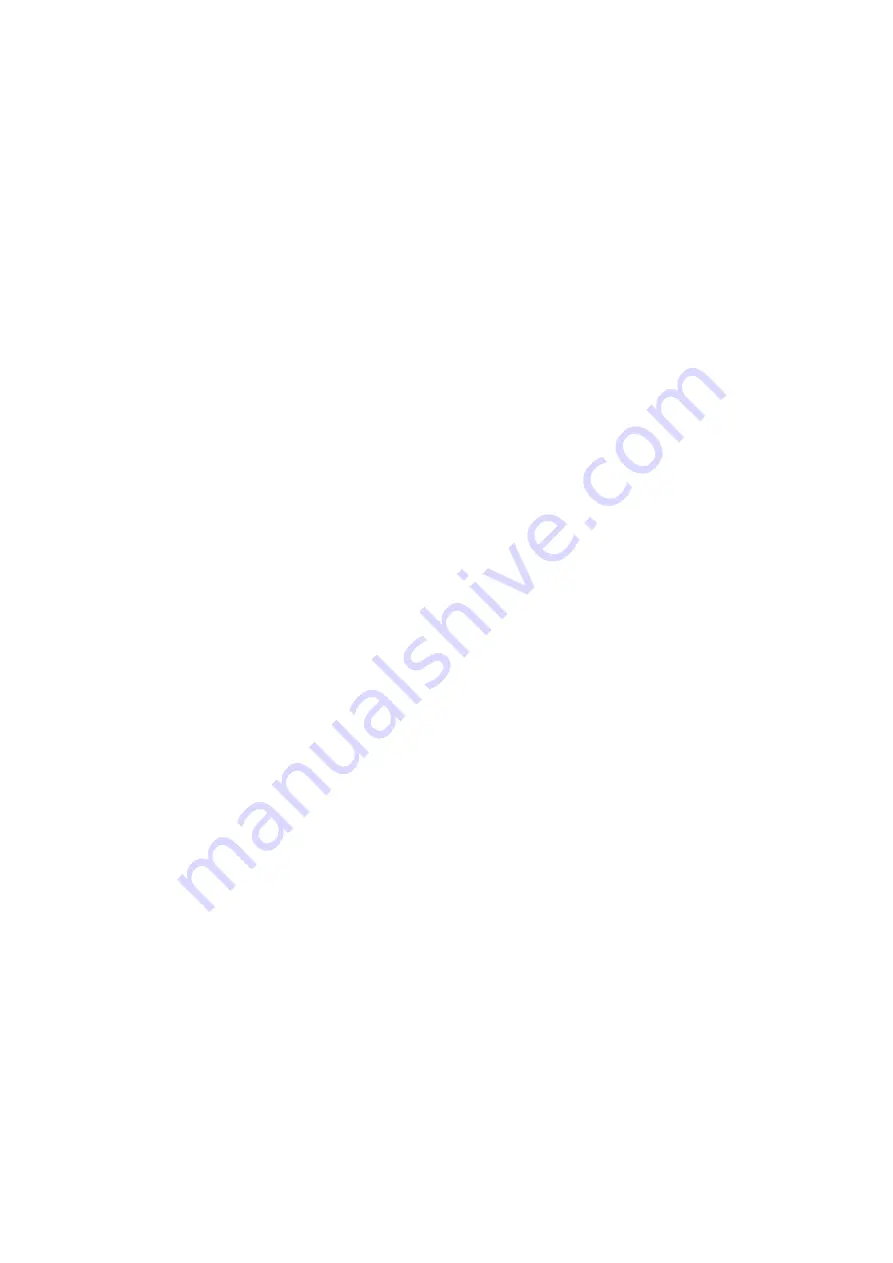
EZTouchPLC
63 / 64
Troubleshooting
If you encounter difficulties while using the
EZTouchPLC
device, please consult the list
below which outlines common troubleshooting issues and their solutions. Additional
assistance is also available within the
EZ
Touch I/O
Software Help
. Alternatively, you
may
also find answers to your questions in the operator interface section of our website @
www.
ezautomation.net.
Issue
: Panel won't power up
Solution
:
Apply power and observe the LED in the back of the panel
a) LED does not turn on: No power to the unit or power supply failed, check the
power supply.
b) LED turns RED and stays RED: Unit has failed, Please return the panel for repair.
c) LED flashes RED and turns GREEN: Unit is OK, Display might have gone bad. Return
panel for repair.
Issue
: Can't program the unit using USB Programming cable
Solution
:
Disconnect and then reconnect the programming cable
Please unplug the USB programming cable from the computer and close the
programming software.
Plug the USB cable back in, wait for 10 – 15 seconds and launch the Programming
software.
Our programming software reads the com ports directly from the device manager of
the computer and it has auto detect feature.
Issue
: USB Flash drive is not recognized
Solution
:
Using a different USB Flash drive, ensure the USB function is enabled
Using a low memory capacity USB Flash drive, preferably less than 2 GB, press and
hold the upper left corner of the Touch screen for about 6 seconds to reach the
Setup
menu on the panel. Click on
English
. Check the 2 pre-programmed buttons to ensure
USB is enabled and “Log to SD (Now USB)” buton is enabled. Restart / power cycle
your panel.
Issue
: Touch cells not responding
Solution
:
Initiate a TouchPad Test
Press and hold the upper left corner of the Touch screen for about 6 seconds to reach
the
Setup
menu on the panel. Click on
English
. Click on the
Touchpad Test
button and
press all Touch cells to see if it responds to Touch. If all buttons respond, then there is
no problem with the Touch screen. If some or all of the touch cells don't respond to
touch, then the unit needs to come back to the factory for repair.
Issue
: Ethernet not responding
Solution
:
Set the IP Address
1.
Please set the IP address for the panel using our programming software and going
to
Setup
>
Ethernet Setup
.
a.
Please match the first 3 octets of the IP address to your network and also
enter subnet mask.
b.
If your network has a gateway, then enter the gateway address.
2.
Please use a straight Ethernet cable and connect it through a hub.
Summary of Contents for EZTouch I/O Flex
Page 1: ...Copyright 2015 by AVG Automation All Rights Reserved EZTouchPLC ...
Page 21: ...EZTouchPLC 21 64 Touch I O with Micro Terminal Layout ...
Page 22: ...EZTouchPLC 22 64 Terminal Pinouts ...
Page 23: ...EZTouchPLC 23 64 ...
Page 26: ...EZTouchPLC 26 64 Analog I O Specifications ...
Page 27: ...EZTouchPLC 27 64 ...
Page 28: ...EZTouchPLC 28 64 Touch I O with Nano Terminal Layout ...