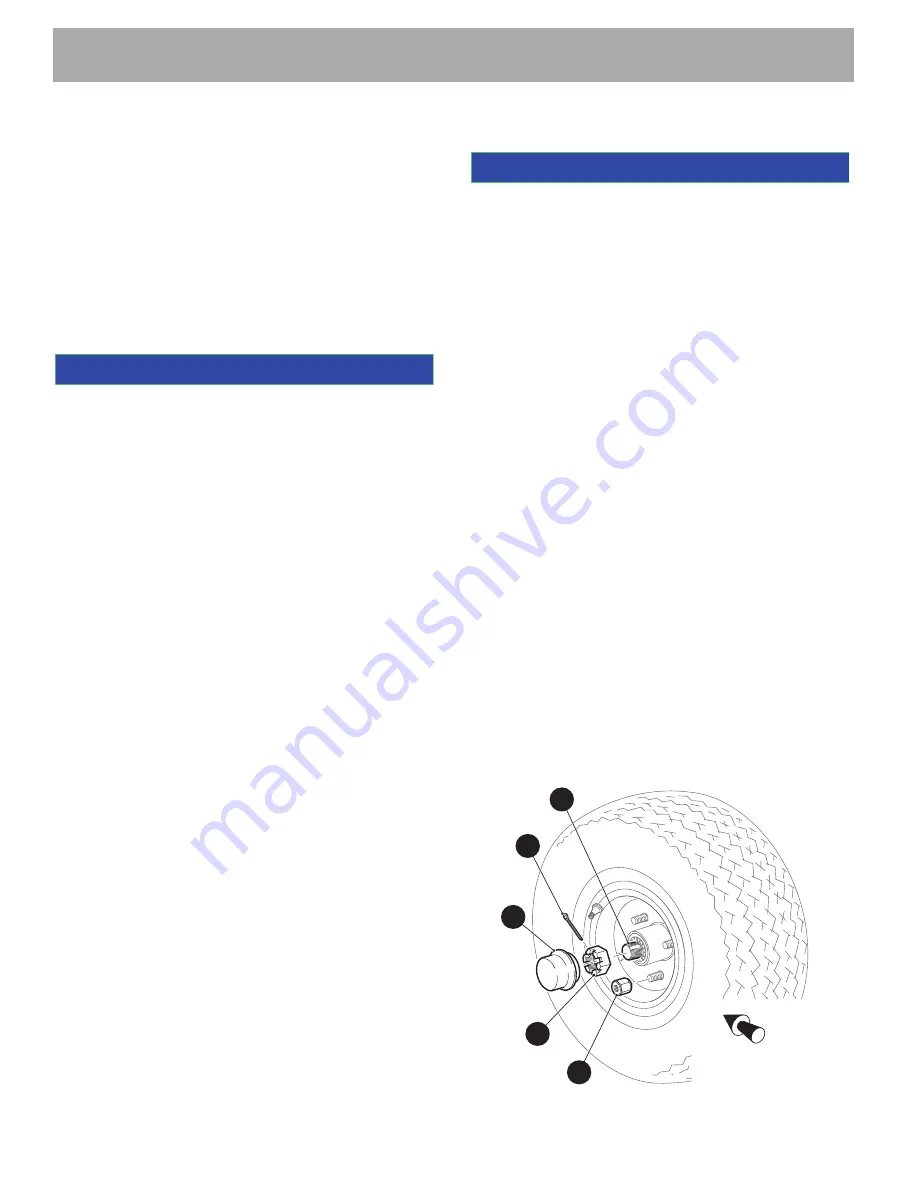
Page E-4
Repair and Service Manual
B
FRONT SUSPENSION AND STEERING
Read all of Section B and this section before attempting any procedure. Pay particular attention to Notices, Cautions, Warnings and Dangers.
vehicle on stands before starting any repair
procedure. Always place chocks in front and
behind wheels not being raised. Use extreme
care since the vehicle is extremely unstable
during the lifting process.
Lift the front of the vehicle and support on jack stands as
per SAFETY section. Rotate the front wheel and feel for
any roughness. While holding spindle with one hand,
grasp bottom of tire with other hand and rock tire back
and forth on spindle.
Some minor rocking movement of tire is normal.
If excess movement is detected, the wheel bearing may
require repacking and adjusting or replacement. See
“Wheel Bearing Packing” on page E-4 and See “Wheel
Bearing Adjustment” on page E-4.
If the wheel bearing is satisfactory, a worn spindle
bearing, which is not a serviceable item, is indicated and
the spindle must be replaced. See “Spindle Replacement”
on page E-16.
Wheel Bearing Packing
Tool List
Qty.
Grease Gun ................................................................. 1
Bearing Packer (Recommended) ................................ 1
Remove hub from spindle and disassemble. See “Wheel
Bearing and Race Replacement” on page E-10.
Clean all bearings, grease seal, hub and dust cap in
solvent and dry thoroughly. Inspect for signs of damage.
Pitting or a blue coloration of the rollers will require
replacement of the bearing. If the roller portion of the
bearing is to be replaced, the race must also be
replaced. See “Wheel Bearing and Race Replacement”
on page E-10.
The front wheel bearings are tapered roller type and
must be packed with grease at installation or any time
the bearing is removed for inspection. It is recom-
mended that a bearing packer attached to a grease gun
be used; however, manual packing is acceptable if done
correctly. To pack a bearing manually requires that a dab
of grease be placed in the palm of the hand and the
bearing be dipped in the grease. Force the grease up
through and around all of the rollers until the entire bear-
ing is saturated in grease.
Assemble hub and install on spindle. See “Hub Replace-
ment” on page E - 9.
Once hub is placed onto spindle and before outer wheel bear-
ing is installed, fill the area between the inner and outer wheel
bearings about 1/2 - 3/4 full with grease.
Wheel Bearing Adjustment
Tool List
Qty.
Socket, 1 1/2”...............................................................1
Ratchet ........................................................................1
If performing a wheel bearing adjustment only, lift and
support front of vehicle per SAFETY section. Remove
dust cap (1) and cotter pin (2) and loosen castellated nut
(3).
If performing a wheel bearing adjustment as part of
another procedure, make sure wheel is mounted to hub
hand tight with lug nuts (4) and hub is loosely retained
on spindle (5) with castellated nut (Ref Fig. 4).
Seat bearings by rotating wheel while tightening castel-
lated nut until slight resistance is felt.
Rotate the wheel 2 - 3 more turns to displace excess
grease. If required, tighten castellated nut (3) again until
slight resistance is felt. If the cotter pin hole in the spin-
dle (5) aligns with a slot in the castellated nut, insert a
new cotter pin (2). If the hole does not align, the castel-
lated nut must be
loosened
to align with the
closest
available
slot in the nut.
Check for smooth and free rotation of the wheel and an
absence of play when the wheel is grasped by the out-
side of the tire. Bend the cotter pin (2) against the flats of
the castellated nut (3).
Replace the dust cap (1) and lower vehicle per SAFETY
section.
Fig. 4 Bearing Adjustment
NOTICE
NOTICE
Front of Vehicle
1
2
5
3
4
Summary of Contents for EXPRESS L6 2012
Page 6: ...Page iv Repair and Service Manual NOTES TABLE OF CONTENTS...
Page 201: ......