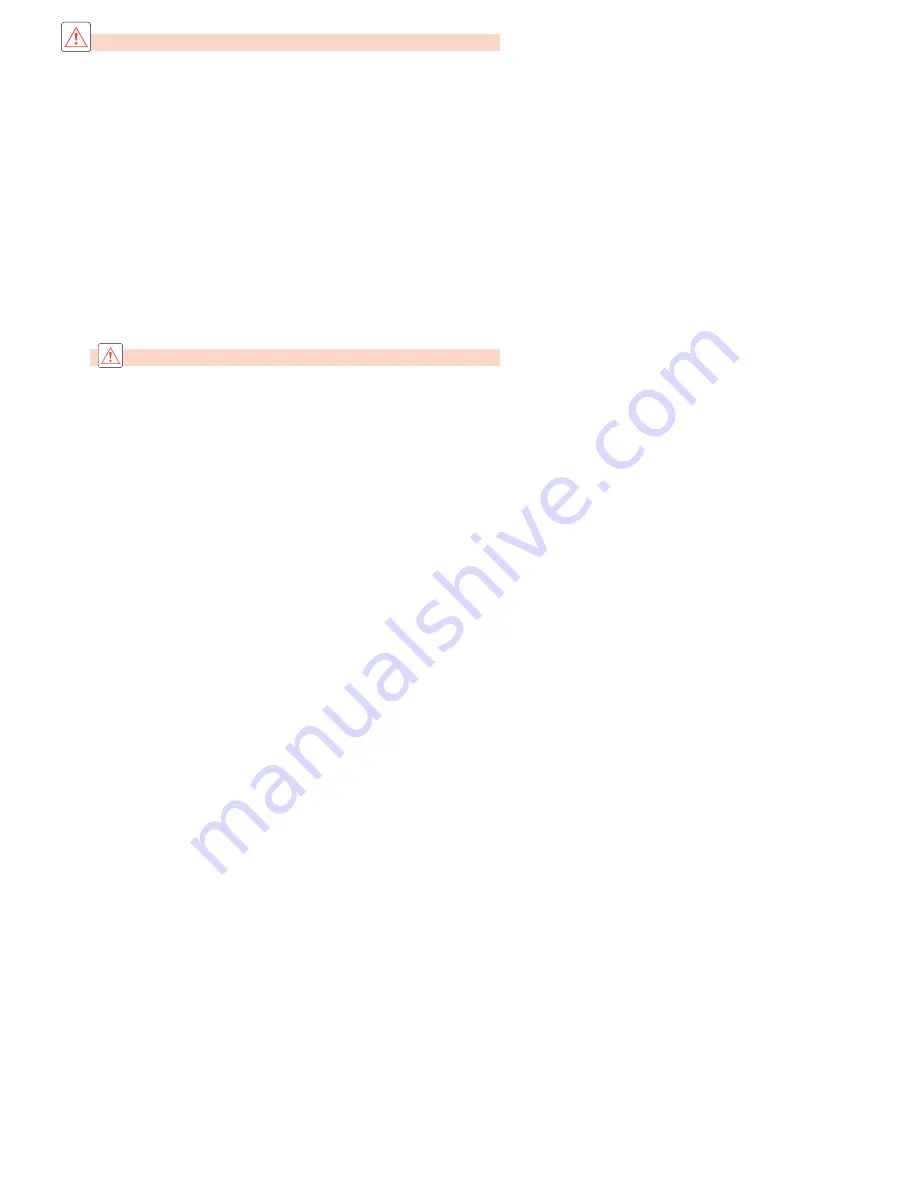
ASSEMBLY, USE AND OPERATION
1. Before operating the jack, a small assembly operation is required, consisting of: Removing the upper cover (
A
), removing the metal rod (2) and connecting the blue plastic tube which is provided disconnected from the
factory (A, B, C) . Place the jack handle in position (4) and secure the bolt (26) and its washer (27), which are included in a kit as indicated (Fig. 3). Replace the cover (1).
2. The handle has four positions: Foldable for transportation and packing (1). Out of operation (2). Movement (3). In operation or horizontal (4). Each position is achieved by disengaging the trigger lever (1, (
B
)). The purpose of
the handle is to position the jack or simplify its movement. Do not exert any pressure on the handle.
3. Should the jack need to be packaged for transportation, remove the screw (26) and the washer (27) and move the handle to position (
A
).
4. It is essential that an air fi lter-lubricator unit is installed (
7
), which is drained daily.
5. Drain the compressor daily. Poor air quality damages essential parts for the proper operation of the jack.
6. Prior to connecting the air supply hose (3 (
B
)), it is necessary to check that the control lever (2) is in the OFF position (
B
). The air hose should not have a section inferior to that of the air entry connector (3). If unusually long
hoses are used, the air pressure should be increased.
7. Ensure that the same air pressure is going to be maintained during operation. Optimum performance of this jack is obtained with a pressure of 7-10 bar and a minimum air fl ow of 280 l/min.
8. A fi nal operation to be performed prior to using the jack is the elimination of any air that may have entered the hydraulic system during transportation. With the air hose connected (3), push the control lever (2, (
B
))
towards the DOWN position, holding it there for some seconds. Move the control lever to the UP position to complete a load free lifting cycle. Move the control lever (2) to the DOWN position to retract the pistons and
hence check that the lowering action is performed steadily without any jerking movements. If the lowering action is unsteady, repeat the cycle until the lowering of the pistons is completed in a steady and uniform way.
This will show that the draining operation has been successfully completed.
9. Now the jack is ready for operation.
10. Lifting Positioning the jack under the lifting point of the vehicle, and following all of the safety instructions described, the lifting operation is performed by moving the to lever control (2, (
8
)) to the UP position and
holding it there until the vehicle has been lifted to the desired height. Immediately place metal stands or another appropriate method to support the elevated vehicle.
11. Lowering Check that there are no obstacles or people underneath the vehicle. Once the operation is completed, remove the mechanical support stands by lifting the vehicle slightly in order to simplify their removal. Lowering is
performed by moving the handle (2, (
9
)) to the DOWN position and maintaining it until the operation is completed.
12. Proceed to retract the pistons by pushing and holding the handle (2, (
9
)) in the DOWN position until they are fully introduced.
13. If the jack is not going to be in use, close the air supply and disconnect the supply hose.
14. After each use, check the components of the jack. If any anomaly is detected, rectify it.
MAINTENANCE
1. Both the maintenance and repair of this jack may only be carried out by qualifi ed and authorized personnel.
2. Before performing any maintenance operation, disconnect the air supply hose from the connection (3, Fig.
7
) located in the handle.
3. Clean and lubricate the moving parts of the jack at regular intervals and introduce a small amount of lubricant in the air inlet connection. The whole jack should be kept clean and protected from aggressive conditions at all times.
4. Oil Level The pistons should be fully retracted prior to proceeding to check or refi ll the oil level. The oil level is correct whet it is between the two marks on the rod. Refi ll as required in accordance with the volume indicated in the table.
5. If all of the oil needs to be replaced, position the jack between two supports so that the connecting tube can be removed (1, Fig.6) (
C
) through which the oil will fl ow and be collected in a container which will be handed over to
an authorised agent. Other methods may also be used to remove the oil: Using a pneumatic oil extractor, positioning the jack in a slanted lateral position, removing the tank etc.
6. IMPORTANT An excess of oil may affect the operation of the jack.
7. Only use hydraulic oil, HL or HM type, with an ISO grade of cinematic viscosity of 20cSt at 40ºC or of an Engler viscosity of 2 at 50ºC.
8. Always use original parts. The use of non-original components may damage the jack and will invalidate the guarantee.
9. Whenever the jack is not in use, the pistons should be fully retracted so as to reduce the risk of corrosion.
GUARANTEE
Type D = 2 years. See the general conditions in the FACOM catalogue or the FACOM price list.
Subject to compliance with all of the above instructions
EN
USER
LIABILITY
Before using the jack, read the following instructions and precautions.
The non-application of these precautions may result in damaging the jack, and may even hurt users.
Inform appropriately the workers in charge of using and maintaining the work equipment, and notably on the conditions of use of work equipment, instructions, or guidelines concerning them.
Check the lifting devices:
- Check when initiating a task, upon fi rst use of the device, whether new or second-hand, in the workshop
- Check upon start-up, to be performed upon dismounting and refi tting, modifi cation, major repair or accident caused by a device failure.
- General periodical checks, performed on a regular basis, aiming at timely detection of any damage likely to create a hazard.
These checks concern devices powered mechanically as well as devices powered by human force. The result of these checks must be recorded in the safety log opened by the site manager.
When devices are faulty, forbid their use or repair immediately.
For manual handling, provide the staff with the individual protections required: safety shoes, preferably in materials resistant to hydrocarbons, protection gloves, etc.
In mechanical handling, unless during tests or proofi ng, never lift a load exceeding that specifi ed on the device.
When using jacks, the following must be ensured: 1. the maximum operating load must be mentioned on the jack,
2. each jack must be checked: - every year in the case of normal use,
- every 6 months in the case of heavy use,
- immediately after use in special conditions, notably after an accidental overload.
Jacks must be used only to lift or lower a vehicle.
Never use a rolling jack to move a vehicle or a load.
When working under a raised vehicle:
- set a block to protect the staff from any untimely lowering of the vehicle, as well as any horizontal displacement
(3)
,
- place a device signalling worker presence,
- if required, wear protection glasses and a cap,
- use an inspection trolley (FACOM
DTS.1A
or
DTS.2
)
WARNINGS
!
1.
Before lifting a vehicle, ensure it is on a stable, fl at, horizontal and clean surface (no grease nor oil)
(1)
.
2.
Check the vehicle to lift is perfectly immobilised
(2)
.
3.
To support the vehicle, use another appropriate means, e.g. a prop
(3)
.
4.
To prevent the assembly from slipping, always centre the load on the jack properly.
5.
Never use extensions
(4)
.
6.
When using the jack, no person must be inside the vehicle or lean on it.
7.
Check the oil level regularly
(5)
. Conversely, too much oil can damage or alter the adjustment of the devices (see « instructions before use» ).
8.
When changing the oil, never use brake fl uid, alcohol, glycerine, detergents, motor oil or used oil. Using dirty oil can cause major internal damage to your equipment. For more information, contact your FACOM
distributor directly. FACOM recommends using the oil reference
WA.20
(5) .
9.
Check the precaution label is legible at all times.When retrofi tting your equipment, these labels are available
(6)
as well as the operating instructions (
Q.NU-DLPLHP/1008
).
INSTRUCTIONS FOR PERFECT USE
1.
Before each use, check the jack. You must particularly check for oil leaks, damaged or missing parts.
2.
Faulty parts must be replaced by skilled staff with FACOM original parts.
3.
Each part in the jack must be checked in case of load considered abnormal or following a shock.
Summary of Contents for 799115
Page 15: ...NOTES...