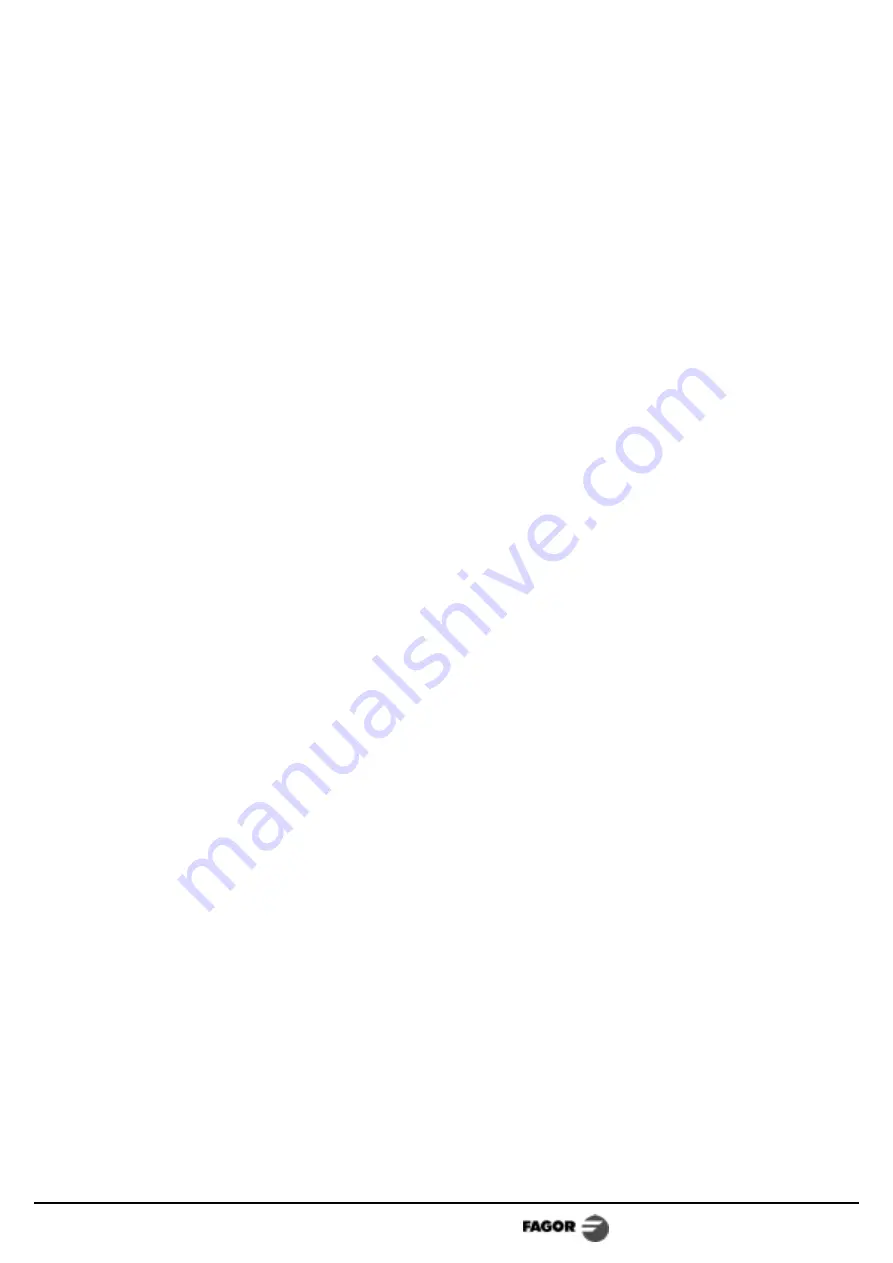
DC Servo Drive System Manual Ver: 0009
DC - 27/32
5.4
INITIALIZATION AND SETUP
Verify that the identity card IM is the right one. The name of the card itself (page 20) indicates
which motor and drive combination it has been designed for.
Verify that the type of feedback selected with jumper J1 matches the feedback device installed on
the motor. Encoder (J1-bc). Tacho (J1-de).
Select whether Ramps are to be generated or not using jumper J2.
Yes (J2-ab). No (J2-bc).
To cancel the control of excessive acceleration, change the jumper J3 position. Active (J3-ab).
Verify that jumper J4 selects the type of command to govern the motor and that it is applied at the
right pins. Current (J4-ab). Velocity (J4-bc).
Somehow, measure the motor speed (with the CNC when using encoder feedback or with a
voltmeter when using a tacho). Apply the maximum velocity command.
Then, turn the Max.Speed potentiometer until reaching the desired speed for that command. For
10V of velocity command with the motor turning at the maximum speed which the RTV1 has been
calculated for, the monitoring output (pins 10 and 11) will provide 10V.
Use the Max.Current.Limit potentiometer to adjust the maximum peak current (maximum motor
torque). To monitor the peak current, the motor may be turned back and forth at full torque and
without generating ramps.
Adjust the gain of the velocity PI with the PI.Gain potentiometer until the desired behavior is
obtained.
Adjust the velocity offset.
Send to the drive an analog voltage of 0 Volts (by jumpering pins 4,5 and 6 of Control-Signals
connector). Measure somehow the motor speed (with the CNC when using encoder feedback
or a voltmeter when using a tacho). Turn the Offset potentiometer on the identity card until the
motor stops. But, CAREFUL, by this method, only the drive offset is eliminated, the CNC may
have an offset of its own. Now the CNC offset should be adjusted.
To adjust the offset in the complete control loop, set the CNC in DRO mode, but with the
“Drive_Enable” and “Speed_Enable” signals actives. Turn the offset potentiometer until
stopping the motor. Another way could be to set a position for the axis with the CNC and turn
this potentiometer until a symmetrical following error is obtained.
Adjust the ramp value. If the generation of ramps has been activated with J2, turn the Acc/Dec
Ramps potentiometer until obtaining the desired behavior.