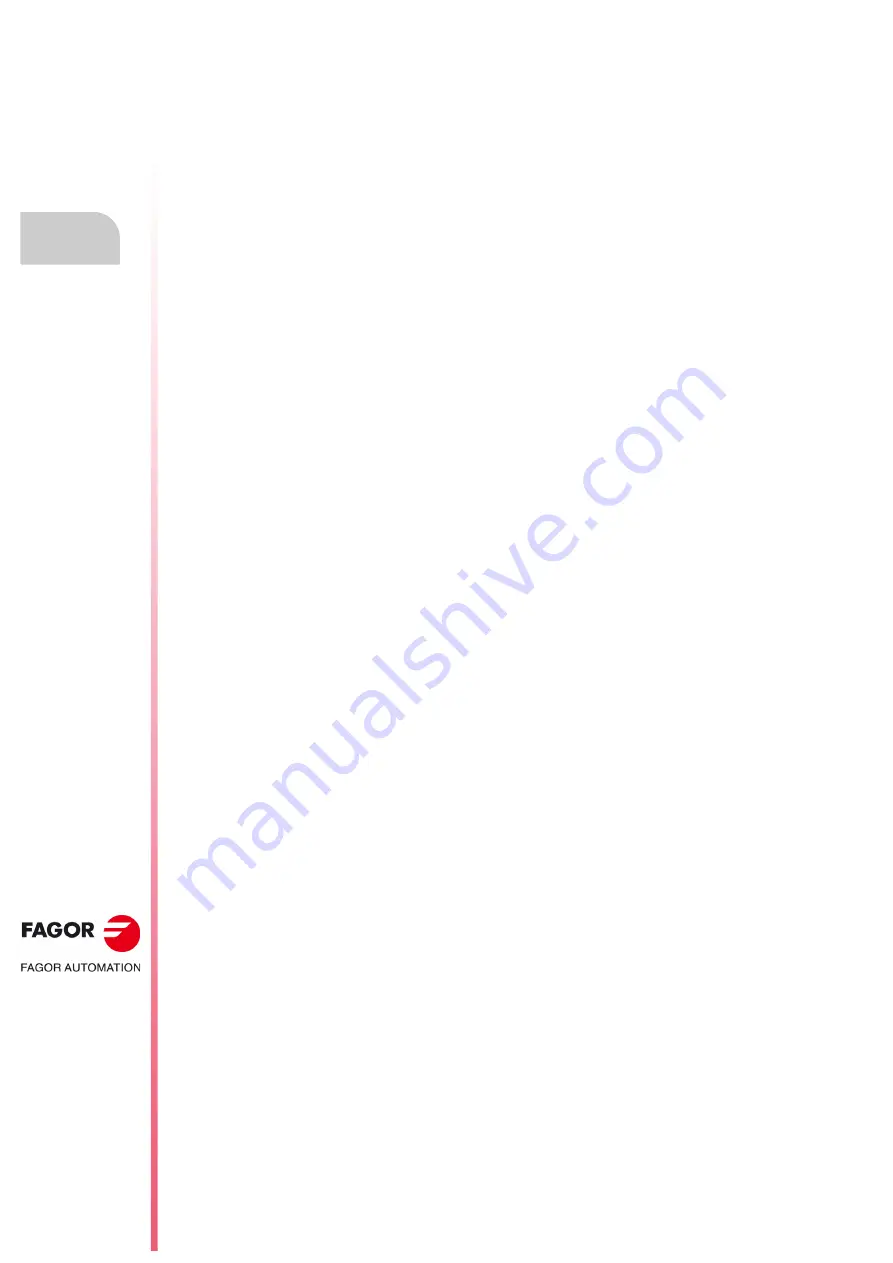
·100·
Programming manual
CNC 8055
CNC 8055i
6.
PATH
CONTROL
·M· & ·EN· M
ODELS
S
OFT
: V02.2
X
Th
readi
ng (G3
3
)
6.12
Threading (G33)
If the machine spindle is equipped with a rotary encoder, you can thread with a tool tip via function
G33.
Although this threading is often done along the entire length of an axis, the CNC enables threading
to be done interpolating more than one axis at a time.
Programming format:
G33 X.....C L Q
Considerations:
Whenever G33 is executed, if s.m.p. M19TYPE (P43) =0, and before making the servo-driven
thread, the CNC references the spindle (home search).
Spindle machine parameter M19TYPE (P43) must be set to "1" in order to be able to program
parameter Q (angular spindle position).
When executing function G33 Q (s.m.p. M19TYPE (P43) =1), and before executing the thread, a
home search must be made for the spindle after the last power-up.
When executing function G33 Q (s.m.p. M19TYPE (P43) =1), and the s.m.p. DECINPUT (P31) =NO,
a home search is not needed for the spindle, since the CNC will be homed automatically after power-
up when turning the spindle in M3 or in M4 for the first time.
This search will be carried out at the feedrate set by s.m.p. REFEED2 (P35). After finding home,
the spindle will speed up or slow down to the programmed speed without stopping.
If the spindle has motor feedback with a SINCOS encoder (without reference mark), the home
search will be done directly at the programmed S speed without going through the speed set by
s.m.p. REFEED2.
If after power-up, an M19 is executed before an M3 or M4, that M19 will be executed without homing
the spindle when executing the first M3 or M4.
If the feedback device does not have the reference mark synchronized, the home search in M3 might
not coincide with the home search in M4. This does not happen with FAGOR feedback.
If the threads are blended together in round corner, only the first one can have an entry angle (Q).
While function G33 is active, neither the programmed feedrate "F" nor the programmed Spindle
speed "S" can be varied. They will both be set to 100%.
Function G33 is modal and incompatible with G00, G01, G02, G03, G34 and G75.
On power-up, after executing M02, M30 or after EMERGENCY or RESET, the CNC assumes code
G00 or G01, depending on how general machine parameter "IMOVE" has been set.
X...C ±5.5
End point of the thread
L 5.5
Thread pitch
Q ±3.5
Optional. It indicates the spindle angular position (±359.9999) of the thread's starting
point. If not programmed, a value of 0 is assumed.
Summary of Contents for 8055 EN
Page 1: ...CNC 8055 M EN Programming manual Ref 1711 Soft V02 2x...
Page 8: ...8 Programming manual CNC 8055 CNC 8055i SOFT V02 2X...
Page 12: ...12 CNC 8055 CNC 8055i Declaration of conformity and Warranty conditions...
Page 16: ...16 CNC 8055 CNC 8055i Version history...
Page 22: ...22 CNC 8055 CNC 8055i Returning conditions...
Page 24: ...24 CNC 8055 CNC 8055i Additional notes...
Page 26: ...26 CNC 8055 CNC 8055i Fagor documentation...
Page 448: ......
Page 464: ...464 Programming manual CNC 8055 CNC 8055i D M EN MODELS SOFT V02 2X Key code...
Page 466: ...466 Programming manual CNC 8055 CNC 8055i D M EN MODELS SOFT V02 2X Key code MC operator panel...
Page 467: ...Programming manual CNC 8055 CNC 8055i D M EN MODELS SOFT V02 2X 467 Key code...
Page 468: ...468 Programming manual CNC 8055 CNC 8055i D M EN MODELS SOFT V02 2X Key code...
Page 471: ...Programming manual CNC 8055 CNC 8055i D M EN MODELS SOFT V02 2X 471 Key code 11 LCD Monitor...
Page 472: ...472 Programming manual CNC 8055 CNC 8055i D M EN MODELS SOFT V02 2X Key code...
Page 478: ...478 Programming manual CNC 8055 CNC 8055i F M EN MODELS SOFT V02 2X Maintenance...
Page 479: ...Programming manual CNC 8055 CNC 8055i F SOFT V02 2X 479...
Page 480: ...480 Programming manual CNC 8055 CNC 8055i F SOFT V02 2X...
Page 481: ......