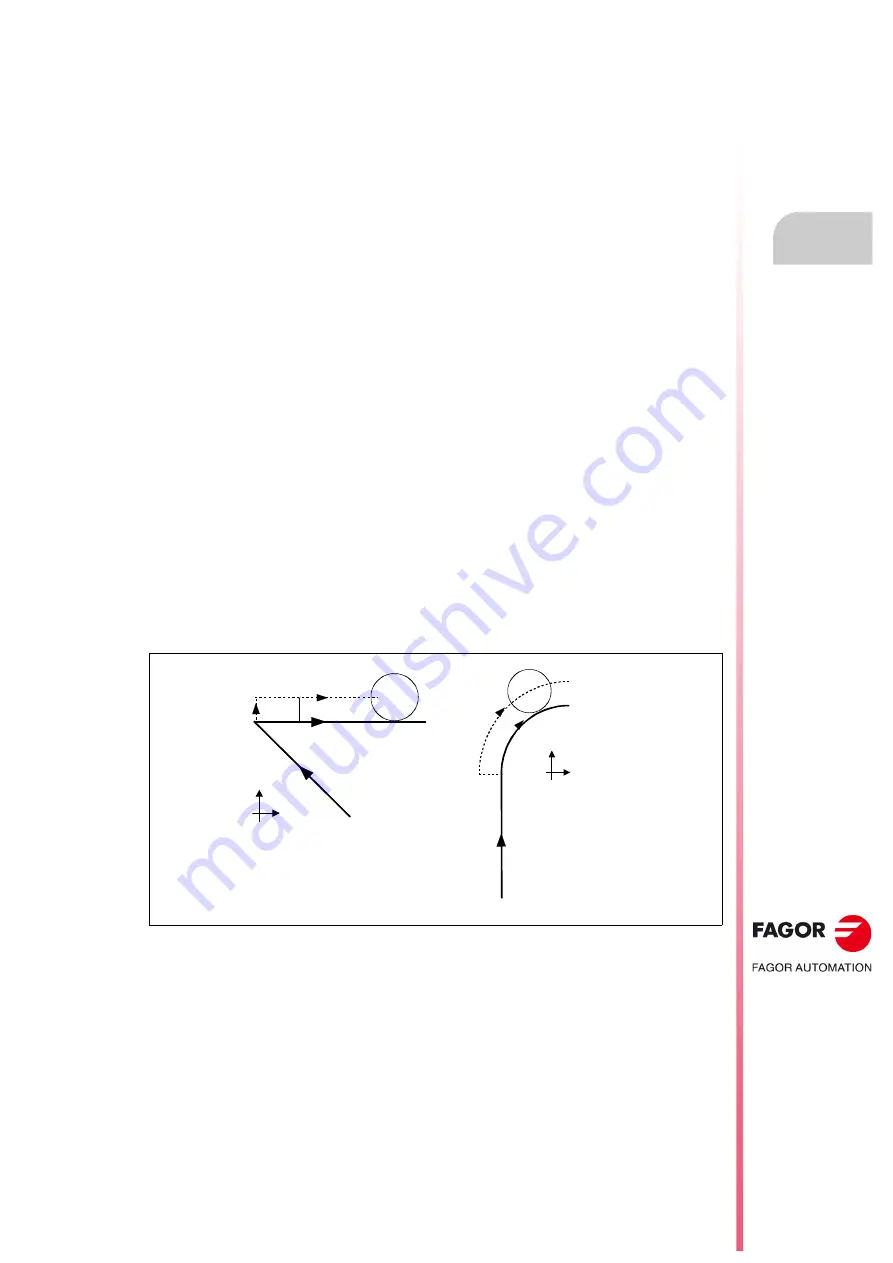
Programming manual
CNC 8055
CNC 8055i
TOOL COMPENSATION
8.
·M· & ·EN· M
ODELS
S
OFT
: V02.2
X
·133·
Too
l
ra
dius compe
n
sation (G40,
G41
, G4
2)
8.1.1
Beginning of tool radius compensation
Once the plane in which tool radius compensation has been selected (via G16, G17, G18, or G19),
functions G41 or G42 must be used to activate it.
G41: Left-hand tool radius compensation.
G42: Tool radius compensation to the right of the part.
In the same block (or a previous one) in which G41 or G42 is programmed, functions T, D, or only
T must be programmed so that the tool offset value to be applied can be selected from the tool offset
table. If no tool offset is selected, the CNC takes D0 with R0 L0 I0 K0.
When the new selected tool has function M06 associated with it and this, in turn, has an associated
subroutine, the CNC will first process the motion block of that subroutine as the starting block of
the compensation.
If in that subroutine, a block is executed that contains function G53 (programming in machine
coordinates), the previously programmed G41 or G42 is canceled.
The selection of tool radius compensation (G41 or G42) can only be made when functions G00 or
G01 are active (straight-line movements).
If the compensation is selected while G02 or G03 are active, the CNC will display the corresponding
error message.
The following pages show different cases of starting tool radius compensation, in which the
programmed path is represented by a solid line and the compensated path with a dotted line.
Beginning of the compensation without programmed movement
After activating the compensation, it could happen that the plane axes do not get involved in the first
motion block either because they have not been programmed or because the same point as the tool
position has been programmed or because a null incremental move has been programmed.
In this case, the compensation is applied in the current tool position; depending on the first movement
programmed in the plane, the tool moves perpendicular to the path on its starting point.
The first movement programmed in the plane may be either linear or circular.
· · ·
G90
G01 Y40
G91 G40 Y0 Z10
G02 X20 Y20 I20 J0
· · ·
(X0 Y0)
Y
X
· · ·
G90
G01 X-30 Y30
G01 G41 X-30 Y30 Z10
G01 X25
· · ·
(X0 Y0)
Y
X
Summary of Contents for 8055 EN
Page 1: ...CNC 8055 M EN Programming manual Ref 1711 Soft V02 2x...
Page 8: ...8 Programming manual CNC 8055 CNC 8055i SOFT V02 2X...
Page 12: ...12 CNC 8055 CNC 8055i Declaration of conformity and Warranty conditions...
Page 16: ...16 CNC 8055 CNC 8055i Version history...
Page 22: ...22 CNC 8055 CNC 8055i Returning conditions...
Page 24: ...24 CNC 8055 CNC 8055i Additional notes...
Page 26: ...26 CNC 8055 CNC 8055i Fagor documentation...
Page 448: ......
Page 464: ...464 Programming manual CNC 8055 CNC 8055i D M EN MODELS SOFT V02 2X Key code...
Page 466: ...466 Programming manual CNC 8055 CNC 8055i D M EN MODELS SOFT V02 2X Key code MC operator panel...
Page 467: ...Programming manual CNC 8055 CNC 8055i D M EN MODELS SOFT V02 2X 467 Key code...
Page 468: ...468 Programming manual CNC 8055 CNC 8055i D M EN MODELS SOFT V02 2X Key code...
Page 471: ...Programming manual CNC 8055 CNC 8055i D M EN MODELS SOFT V02 2X 471 Key code 11 LCD Monitor...
Page 472: ...472 Programming manual CNC 8055 CNC 8055i D M EN MODELS SOFT V02 2X Key code...
Page 478: ...478 Programming manual CNC 8055 CNC 8055i F M EN MODELS SOFT V02 2X Maintenance...
Page 479: ...Programming manual CNC 8055 CNC 8055i F SOFT V02 2X 479...
Page 480: ...480 Programming manual CNC 8055 CNC 8055i F SOFT V02 2X...
Page 481: ......