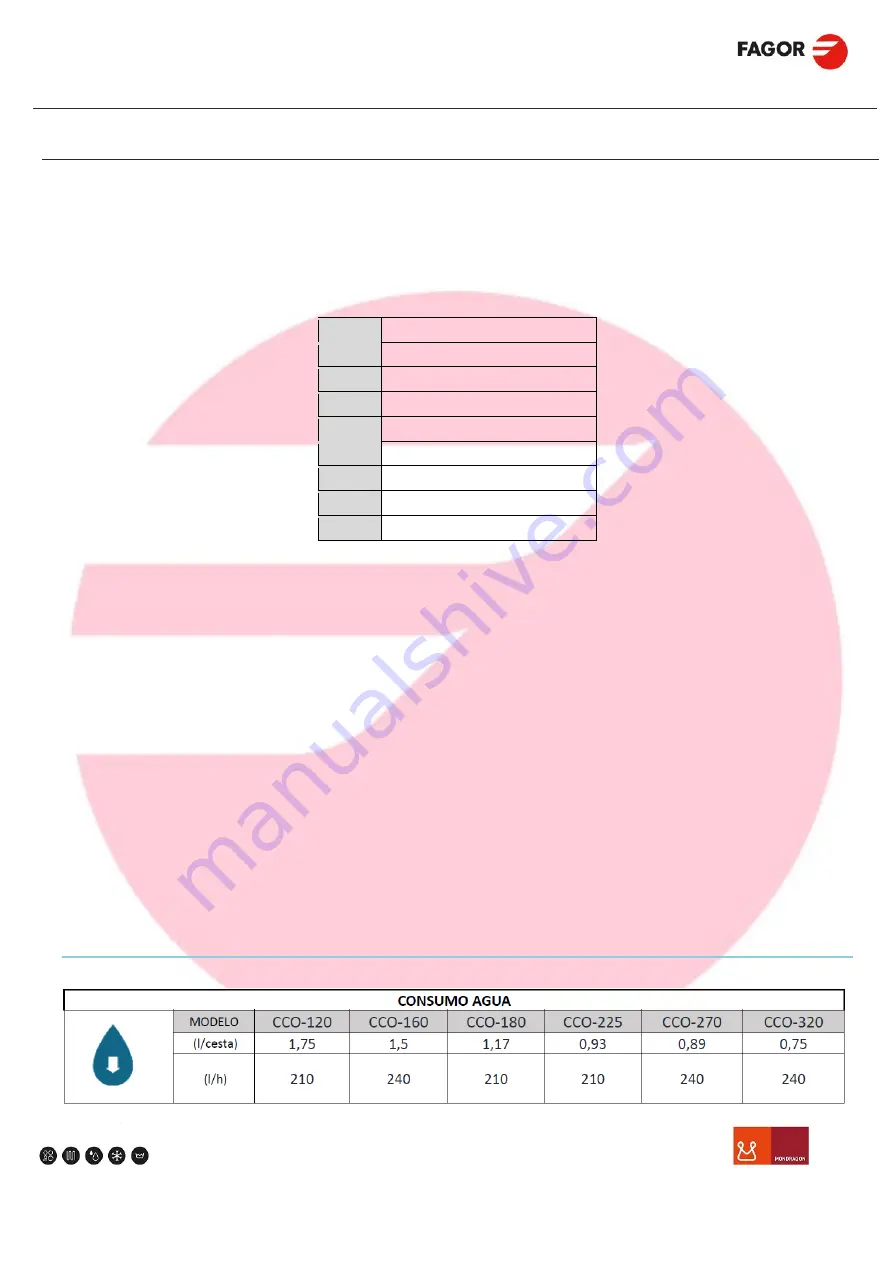
02/05/2020
32
SERVICE MANUAL
CONVEYOR BELT
DISHWASHERS
water inlet hose to
A+F.
•
Install a shut-off valve on the water supply close to the machine in an accessible position.
•
A filter must be installed after the shut-off valve and before the appliance and should be easily accessible
for cleaning.
•
Check that the mains pressure is within the range indicated above.
•
Check that there are no leaks.
The hydraulic circuit guarantees a stable consumption in the event of changes in pressure in the mains. The water
input pressure to the machine should be 2 to 4 bar. Therefore, the rinse water control pressure must be adjusted to the
following pressures:
CCO-120 -> 0.7 bar -> 210 L/h
CCO-160 -> 0.9 bar -> 240 L/h
CCO-180 -> 0.7 bar -> 210 L/h
CCO-225 -> 0.7 bar -> 210 L/h
CCO-270 -> 0.9 bar -> 240 L/h
CCO-320 -> 0.9 bar -> 240 L/h
In the ECO models, the rinse water flow must be adjusted with the following flows:
CCO-120 ECO -> 210 L/h
CCO-160 ECO -> 240 L/h
CCO-180 ECO -> 210 L/h
CCO-225 ECO -> 210 L/h
CCO-270 ECO -> 240 L/h
CCO-320 ECO -> 240 L/h
19.5.
WATER CONSUMPTION
S
Water shut-off valve
FE
Exterior filter
RP
Pressure reducer
M
Manometer
BP
Pressure pump
H
Water inlet hose
A+F
Water inlet and filter
EV
Electrovalve
DH
Drainage hose
Summary of Contents for CCO-180
Page 1: ...CONVEYOR DISHWASHERS Service Manual SERVICE MANUAL CONVEYOR DISHWASHERS 02 05 2020 ...
Page 13: ...02 05 2020 12 SERVICE MANUAL CONVEYOR BELT DISHWASHERS 11 USE ...
Page 19: ...02 05 2020 18 SERVICE MANUAL CONVEYOR BELT DISHWASHERS 15 TECHNICAL DATA ...
Page 20: ...02 05 2020 19 SERVICE MANUAL CONVEYOR BELT DISHWASHERS ...
Page 57: ...02 05 2020 56 SERVICE MANUAL CONVEYOR BELT DISHWASHERS ...
Page 67: ...02 05 2020 66 SERVICE MANUAL CONVEYOR BELT DISHWASHERS ...
Page 71: ...02 05 2020 70 SERVICE MANUAL CONVEYOR BELT DISHWASHERS ...
Page 75: ...02 05 2020 74 SERVICE MANUAL CONVEYOR BELT DISHWASHERS 36 ELECTRICAL DIAGRAM ...
Page 76: ...02 05 2020 75 SERVICE MANUAL CONVEYOR BELT DISHWASHERS ...