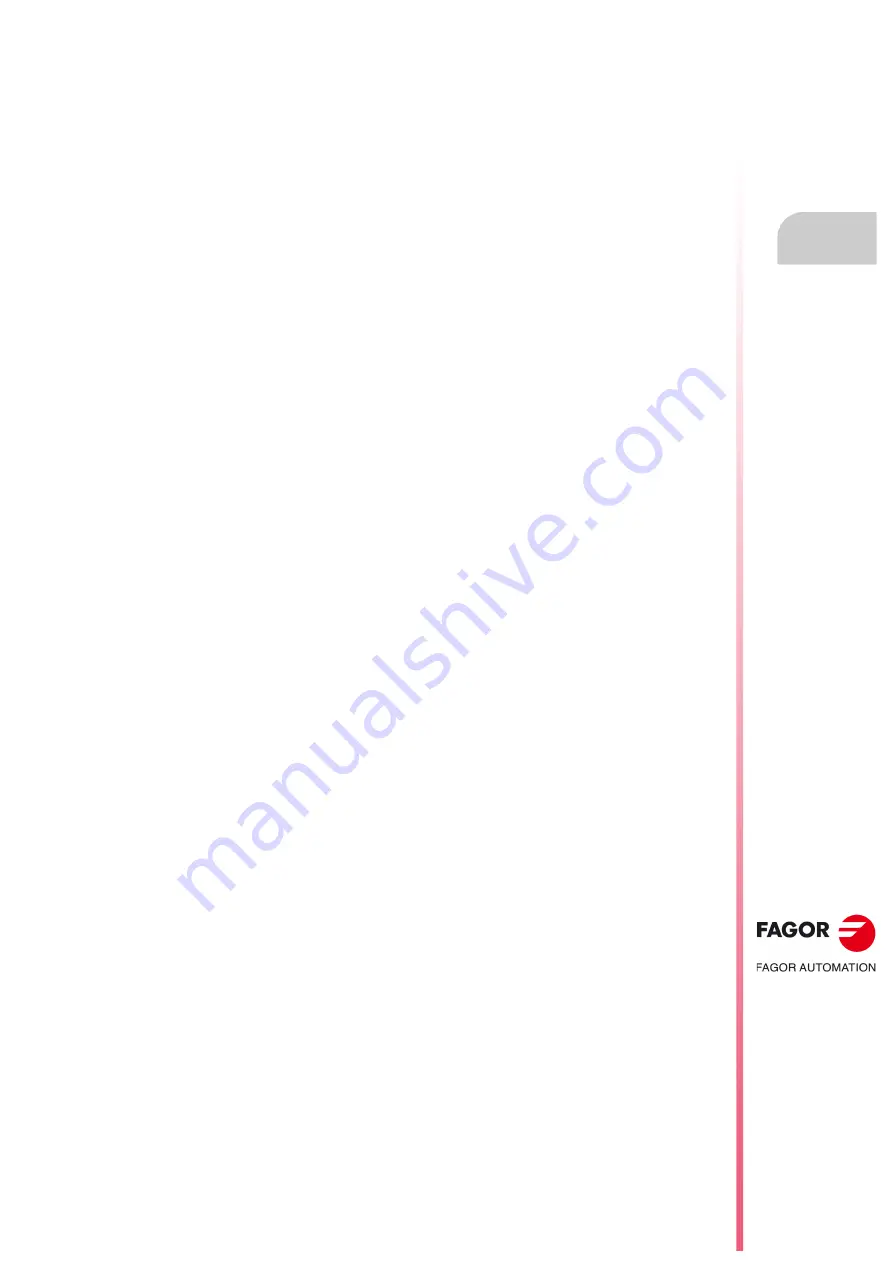
Hardware configuration.
CNC 8070
·11·
(R
EF
: 1911)
SOFT C AXIS
C axis.
It activates the kinematics for working with the C axis and
the associated canned cycles. The CNC can control
several C axes. The parameters of each axis indicate if it
will function as a C axis or not, where it will not be
necessary to activate another axis for the machine
parameters.
SOFT TANDEM AXES
Tandem axes.
A tandem axis consists in two motors mechanically
coupled (slaved) and making up a single transmission
system (axis or spindle). A tandem axis helps provide the
necessary torque to move an axis when a single motor is
not capable of supplying enough torque to do it.
When activating this feature, it should be kept in mind that
for each tandem axis of the machine, another axis must be
added to the entire configuration. For example, on a large
3-axis lathe (X Z and tailstock), if the tailstock is a tandem
axis, the final purchase order for the machine must
indicate 4 axes.
SOFT SYNCHRONISM
Synchronization of axes and spindles.
The axes and ballscrews may be synchronized in two
ways: in terms of speed or position. The CNC
configuration takes into consideration the synchronization
of 2 axes or 2 spindles. Once synchronized, only the
master displays and programs the element.
SOFT HSSA II MACHINING SYSTEM
HSSA-II machining system.
This is the new version of algorithms for high speed
machining (HSC). This new HSSA algorithm allows for
high speed machining optimization, where higher cutting
speeds, smoother contours, a better surface finishing and
greater precision are achieved.
SOFT TANGENTIAL CONTROL
Tangential control.
"Tangential Control" maintains a rotary axis always in the
same orientation with respect to the programmed tool
path. The machining path is defined on the axes of the
active plane and the CNC maintains the orientation of the
rotary axis along the entire tool path.
SOFT DRILL CYCL OL
Drilling ISO cycles for the OL model.
Drilling ISO cycles for the OL model (G80, G81, G82,
G83).
SOFT PROBE
Probing canned cycles.
The CNC may have two probes; usually a tabletop probe
to calibrate tools and a measuring probe to measure the
part.
This option activates the functions G100, G103 and G104
(for probe movements); probe canned cycles are not
included.
SOFT THIRD PARTY I/Os
Third-party CANopen.
Enables the use of non-Fagor CANopen modules.
SOFT FVC STANDARD
SOFT FVC UP TO 10m3
SOFT FVC MORE TO 10m3
Volumetric compensation.
5-axis machines are generally used during the
manufacturing of large parts. The accuracy of the parts is
limited by the machine manufacturing tolerances and is
effected by temperature variations during machining.
In sectors such as the aerospace industry, machining
demands mean that classic compensation tools are
becoming suboptimal. Volumetric compensation FVC
comes in to complement the machine adjusting tools.
When mapping the total work volume of the machine, the
CNC knows the exact position of the tool at all times. After
applying the required compensation, the resulting part is
made with the desired precision and tolerance.
There are 3 options, which depend on the size of the
machine.
• FVC STANDARD: 25-point compensation on each
axis. Quick calibration (time), but less precise than the
other two, but sufficient for the desired tolerances.
• FVC UP TO 10m3: Volume compensation up to 10 m³.
More accurate than FVC STANDARD, but requires a
more accurate calibration using a Tracer or Tracker
laser).
• FVC MORE TO 10m3: Volume compensation greater
than 10 m³. More accurate than FVC STANDARD, but
requires a more accurate calibration using a Tracer or
Tracker laser.
SOFT 60 PWM CONTROL
Pulse-Width Modulation.
This function is only available for Sercos bus controlled
systems. It is mostly oriented toward laser machines for
the cutting of very thick sheets, where the CNC generates
a series of PWM pulses to control the power of the laser
when drilling the starting point.
This feature is essential for cutting very thick sheets and
it requires two quick digital outputs located on the central
unit. With this new feature, the OEM does not need to
install or program any external device, which reduces
machine costs and installation times. The end user also
benefits, since the “Cutting with PWM ” feature is much
easier to use and program.
SOFT 60 GAP CONTROL
Gap control.
This is mostly oriented toward laser machines. Gap
control makes it possible to maintain a set distance
between the laser nozzle and the surface of the sheet. This
distance is calculated by a sensor connected to the CNC,
so that the CNC offsets the sensor variations on the
distance programmed with additional movements in the
axis programmed for the gap.
SOFT DMC
Dynamic Machining Control.
DMC adapts the feedrate during machining to maintain the
cutting power as close as possible to ideal machining
conditions.
SOFT FMC
Fagor Machining Calculator.
The FMC application consists of a database of materials
to be machined and machining operations (milling and
turning) with an interface to choose suitable cutting
conditions for these operations.
SOFT FFC
Fagor Feed Control.
During the execution of a canned cycle of the editor, the
FFC function makes it possible to replace the feedrate and
speed programmed in the cycle with the active values of
the execution, which are acted upon by the feed override
and speed override.
SOFT 60/65/70 OPERATING TERMS
Temporary user license.
The "Operating Terms" option activates a temporary user
license for the CNC, which is valid until the date
determined by the OEM.
Summary of Contents for CNC 8070
Page 1: ...Ref 1911 8070 CNC Hardware configuration...
Page 8: ...BLANK PAGE 8...
Page 14: ...BLANK PAGE 14...
Page 18: ...BLANK PAGE 18...
Page 22: ...BLANK PAGE 22...
Page 24: ...BLANK PAGE 24...
Page 26: ...BLANK PAGE 26...
Page 28: ...Hardware configuration CNC 8070 1 PREVIOUS INFORMATION 28 REF 1911...
Page 94: ...Hardware configuration CNC 8070 6 CENTRAL UNIT MONITOR Q7 A PLATFORM 94 REF 1911 C70 15AT...
Page 273: ...Hardware configuration CNC 8070 273 User notes REF 1911...
Page 274: ...Hardware configuration CNC 8070 274 User notes REF 1911...
Page 275: ...Hardware configuration CNC 8070 275 User notes REF 1911...