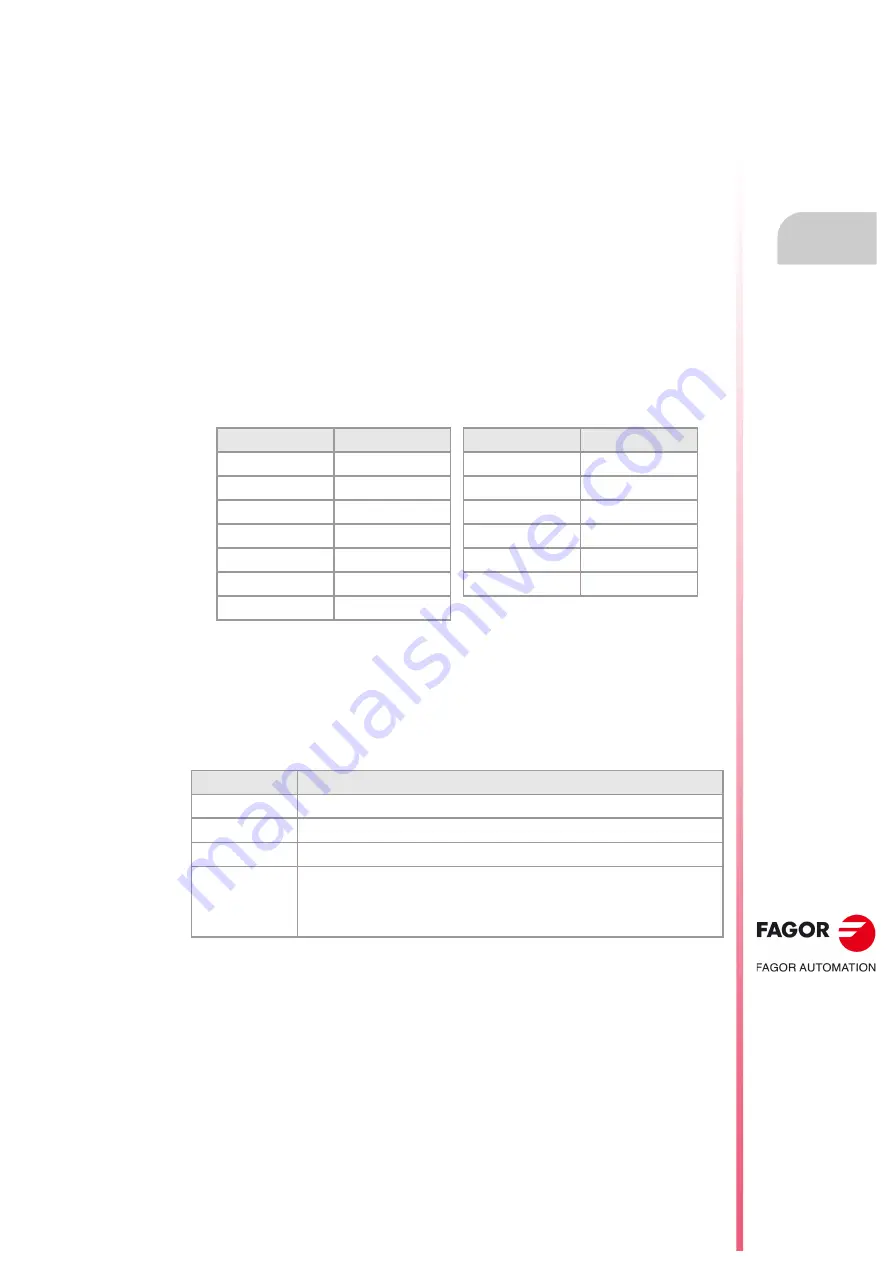
Hardware configuration.
CNC 8070
CEN
T
RAL UNIT + MONITOR (Q7-A
PLATFORM).
6.
Conn
ecti
ons.
·133·
(R
EF
: 1911)
Identification of the first and last elements of the bus. Line
terminating resistor.
In the CAN bus, it is necessary to use a line terminating resistor to identify which are the
elements that occupy the ends of the bus; i.e. the first and last physical element in the
connection. For the central unit, the terminating resistor is factory installed because the CNC
is always at one end of the bus.
Bus type selector: CANfagor / CANopen.
At the CNC, the type of CAN bus is selected by means of the machine parameters (parameter
CANMODE),
Selection of the cable length of the CANfagor bus cable.
When using the CANfagor protocol, the transmission speed at the bus is defined at the CNC
(parameter CANLENGTH). The transmission speed depends on the total length of the cable.
Use the following approximate values. Assigning other values may cause communication
errors due to signal distortion.
Selecting the speed for the CANopen bus.
When using the CANopen protocol, the transmission speed at the bus is defined in each node
and they all must run at the same speed. The transmission speed depends on the total length
of the bus. Using the following illustrative values; assigning other values may cause
communication errors due to signal distortion.
Selecting the speed at the CNC.
At the CNC, the transmission speed is selected by means of the machine parameters
(parameter CANOPENFREQ).
Speed
Length of the CAN bus.
1000 kHz
Up to 20 meters.
800 kHz
From 20 to 40 meters.
500 kHz
From 40 to 100 meters.
250 kHz
From 100 to 500 meters.
The speed of 250 kHz is only available to communicate with the keyboards and
RIOW and RIOR series remote modules; this speed is not available for the RIO5
series remote modules.
Length (m)
Speed (KHz)
20
1000
30
888
40
800
50
727
60
666
70
615
80
571
Length (m)
Speed (KHz)
90
533
100
500
110
480
120
430
130
400
> 130
250
Summary of Contents for CNC 8070
Page 1: ...Ref 1911 8070 CNC Hardware configuration...
Page 8: ...BLANK PAGE 8...
Page 14: ...BLANK PAGE 14...
Page 18: ...BLANK PAGE 18...
Page 22: ...BLANK PAGE 22...
Page 24: ...BLANK PAGE 24...
Page 26: ...BLANK PAGE 26...
Page 28: ...Hardware configuration CNC 8070 1 PREVIOUS INFORMATION 28 REF 1911...
Page 94: ...Hardware configuration CNC 8070 6 CENTRAL UNIT MONITOR Q7 A PLATFORM 94 REF 1911 C70 15AT...
Page 273: ...Hardware configuration CNC 8070 273 User notes REF 1911...
Page 274: ...Hardware configuration CNC 8070 274 User notes REF 1911...
Page 275: ...Hardware configuration CNC 8070 275 User notes REF 1911...