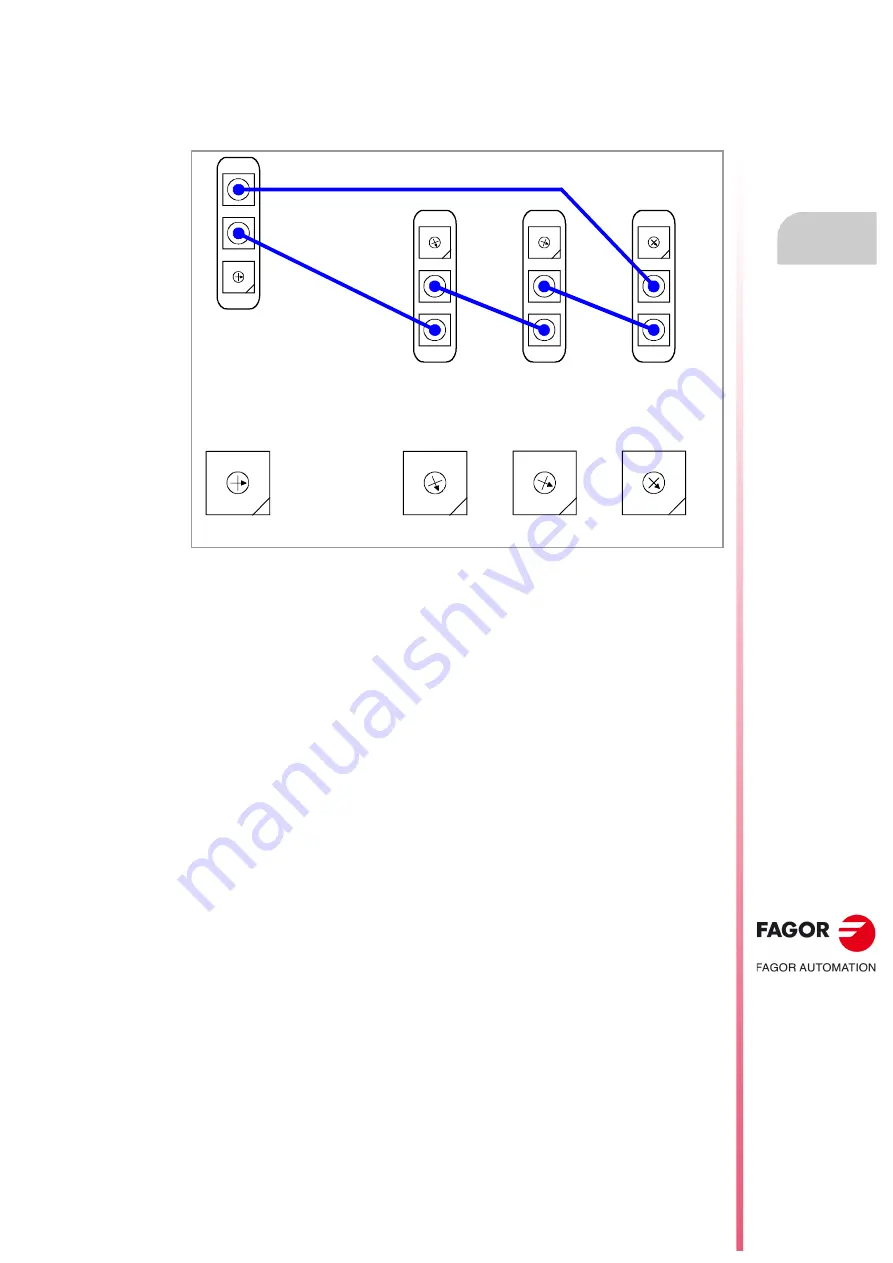
Hardware configuration.
CNC 8070
CENTRAL
UNIT + MONITO
R (ETX PLATFORM).
5.
Conn
ecti
ons.
·91·
(R
EF
: 1911)
Interconnection of modules.
The Sercos connection is carried out in a ring using fiber optic cable by joining an OUT
terminal with an IN terminal. The drawing shows the Sercos connection of the CNC with
Fagor spindle drives and the X, Y axes.
Data exchange via Sercos.
The data exchange between the CNC and the drives takes place at every position loop. The
more data is exchanged, the more overloaded the Sercos transmission will be. These
registers should be limited leaving only the ones absolutely necessary after the setup.
There is data that must necessarily be transmitted in every position loop (velocity commands,
feedback, etc.) and other data that may be transmitted in several loops (monitoring, etc.).
Since the CNC must know the priority of those transmissions, there must be two separate
transmission channels.
Cyclic channel (fast).
The data is transmitted in every position loop. It contains the commands, feedback, etc. Each
variable read or written at the drive is included in this information package. In order not to
overload the interface, you must limit the number of drive variables involved to the minimum
necessary.
Indicate the type of data to be transmitted. The data to be sent to the drives must be placed
in certain particular registers of the PLC and the data to be read from the drives is received
in other registers of the PLC.
Service channel (slow).
The data is transmitted in several position loops. It contains monitoring data, etc.
This channel can only be accessed through high-level blocks in the part-program or from
the PLC channel.
4
0
F
E
D
C
B
A
9
8
7 6 5 3 2
1
OUT
IN
4
0
1
F
E
D
C
B
A
9
8
7 6 5 3 2
Node = 0
CNC
C
4
0
F
E
D
B
A
9
8
7 6 5 3 2
1
Node = 3
SPINDLE
4
0
F
E
D
C
B
A
9
8
7 6 5 3 2
1
Node = 1
X AXIS
4
0
F
E
D
C
B
A
9
8
7 6 5 3 2
1
Node = 2
Y AXIS
4
8
5
0
F
E
D
C
B
A
9
7 6
3 2
1
45
C
3
0
F
E
D
B
A
9
8
7 6
2 1
4
0
F
C
5
3
1
E
D
B
A
9
8
7 6
2
OUT
IN
OUT
IN
OUT
IN
Summary of Contents for CNC 8070
Page 1: ...Ref 1911 8070 CNC Hardware configuration...
Page 8: ...BLANK PAGE 8...
Page 14: ...BLANK PAGE 14...
Page 18: ...BLANK PAGE 18...
Page 22: ...BLANK PAGE 22...
Page 24: ...BLANK PAGE 24...
Page 26: ...BLANK PAGE 26...
Page 28: ...Hardware configuration CNC 8070 1 PREVIOUS INFORMATION 28 REF 1911...
Page 94: ...Hardware configuration CNC 8070 6 CENTRAL UNIT MONITOR Q7 A PLATFORM 94 REF 1911 C70 15AT...
Page 273: ...Hardware configuration CNC 8070 273 User notes REF 1911...
Page 274: ...Hardware configuration CNC 8070 274 User notes REF 1911...
Page 275: ...Hardware configuration CNC 8070 275 User notes REF 1911...