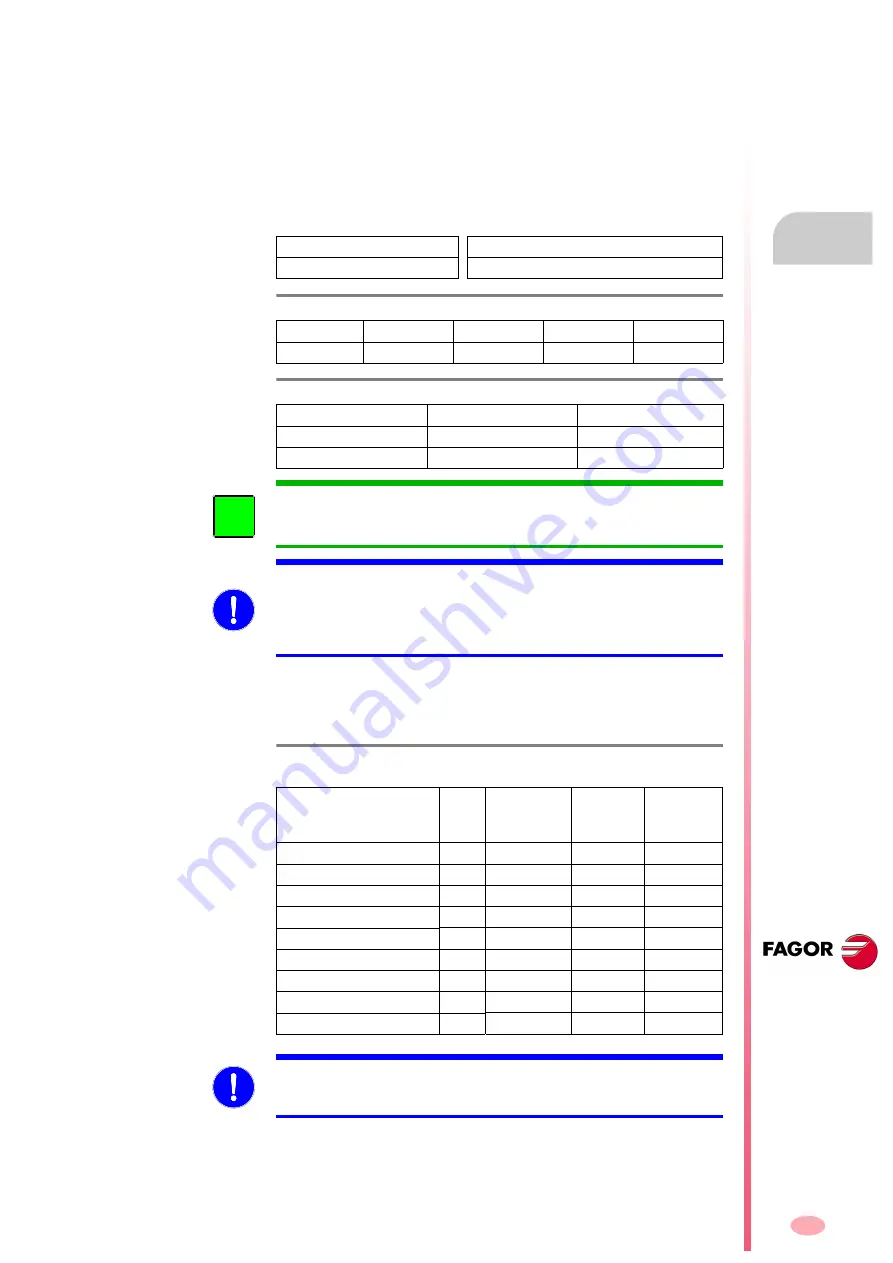
Cables
CABLES
Powe
r
cab
le. Motor-dri
ve
co
nnectio
n
7.
249
DDS
HARDWARE
Ref.1310
7.2 Power cable. Motor-drive connection
Table
and table
show the range of power cables supplied
by FAGOR to connect a motor and a drive.
They are supplied without
connectors
because the power connector will usually be different de-
pending on the motor it will be connected to. The number of meters avail-
able upon request. It is available in lengths of 5, 10, 15, 20, 30, 40, 50,
75, 100, 150, 200, 250 and 300 meters for sections up to 10 mm² (includ-
ed) and 5, 7, 10, 12, 15, 20, 25, 30, 35, 40, 45, 50, 75 and 100 for sec-
tions of up to 50 mm
2
(included). Their sales reference is:
Power terminals. Mechanical characteristics
The mechanical characteristics of the terminals (U, V, W, PE) on modular
drives are:
For further details on the connector that must be mounted at the end of
the MPC cable and connected at the motor end, see the manual of the
corresponding motor.
MPC-4
x
to connect motors without brake
MPC-4
x
+(2
x
)
to connect motors with brake
T. H7/4
Range of cables to connect a motor (without brake) and a drive.
MPC-4x1.5
MPC-4x4
MPC-4x10
MPC-4x25
MPC-4x50
MPC-4x2.5
MPC-4x6
MPC-4x16
MPC-4x35
MPC-4x70
T. H7/5
Range of cables to connect a motor (with brake) and a drive.
MPC-4x1.5+(2x1)
MPC-4x6+(2x1)
MPC-4x25+(2x1)
MPC-4x2.5+(2x1)
MPC-4x10+(2x1)
MPC-4x4+(2x1)
MPC-4x16+(2x1.5)
INFORMATION.
Remember that when a motor is mentioned here, it re-
fers to any motor of the FAGOR catalog, both synchronous and asynchro-
nous.
MANDATORY.
In order for the system to comply with the European Di-
rective on Electromagnetic Compatibility, the cable hose that carries 6 or
4 cables, depending on whether the motor has a brake or not, must be
shielded and connected at both ends; i.e. both at the drive end and a the
motor end. This condition is a must.
i
T. H7/6
Mechanical characteristics of the power connectors of the modular
drives.
Module
Gap
(mm)
Max. tight-
enin torque
(N·m)
Max. hole
section
(mm²)
Min. cable
section
(mm²)
AXD/SPD/MMC 1.08/1.15
7.62
0.6
4
2.5
AXD/SPD/MMC 1.25
7.62
0.8
6
6
AXD/SPD/MMC 1.35
10.16
1.5
6
6
AXD/SPD/MMC 2.
10.16
1.8
16
16
SPD 2.85
10.16
1.8
16
16
AXD/SPD/MMC 3.100
-
8
50
25
AXD/SPD/MMC 3.150
-
8
50
50
SPD 3.200
-
20
95
70
SPD 3.250
-
20
95
95
MANDATORY.
The cable wires connected at the motor end must be kept
inside their corresponding connector. The connector will be different de-
pending on the user's motor.
Summary of Contents for DDS
Page 1: ...DRIVE DDS Hardware manual Ref 1310...
Page 6: ...I 6 DDS HARDWARE Ref 1310...
Page 9: ......
Page 10: ......
Page 11: ......
Page 12: ......
Page 16: ...16 Ref 1310 DDS HARDWARE...
Page 30: ...1 DESCRIPTION 30 Description DDS HARDWARE Ref 1310...
Page 94: ...2 POWER SUPPLIES 94 Power supplies DDS HARDWARE Ref 1310...
Page 188: ...3 DRIVE MODULES 188 Drive modules DDS HARDWARE Ref 1310...
Page 204: ...4 AUXILIARY MODULES 204 Auxiliary modules DDS HARDWARE Ref 1310...
Page 232: ...SELECTING CRITERIA 5 232 Selection criteria DDS HARDWARE Ref 1310...
Page 266: ...7 CABLES 266 Cables DDS HARDWARE Ref 1310...
Page 312: ...8 INSTALLATION 312 Installation DDS HARDWARE Ref 1310...
Page 326: ...9 FUNCTIONAL SAFETY 326 Functional safety DDS HARDWARE Ref 1310...
Page 354: ...10 CONNECTION DIAGRAMS 354 Connection diagrams DDS HARDWARE Ref 1310...
Page 378: ...12 SALES REFERENCES 378 Sales references DDS HARDWARE Ref 1310...
Page 384: ...13 COMPATIBILITY 384 Compatibility DDS HARDWARE Ref 1310...
Page 385: ......