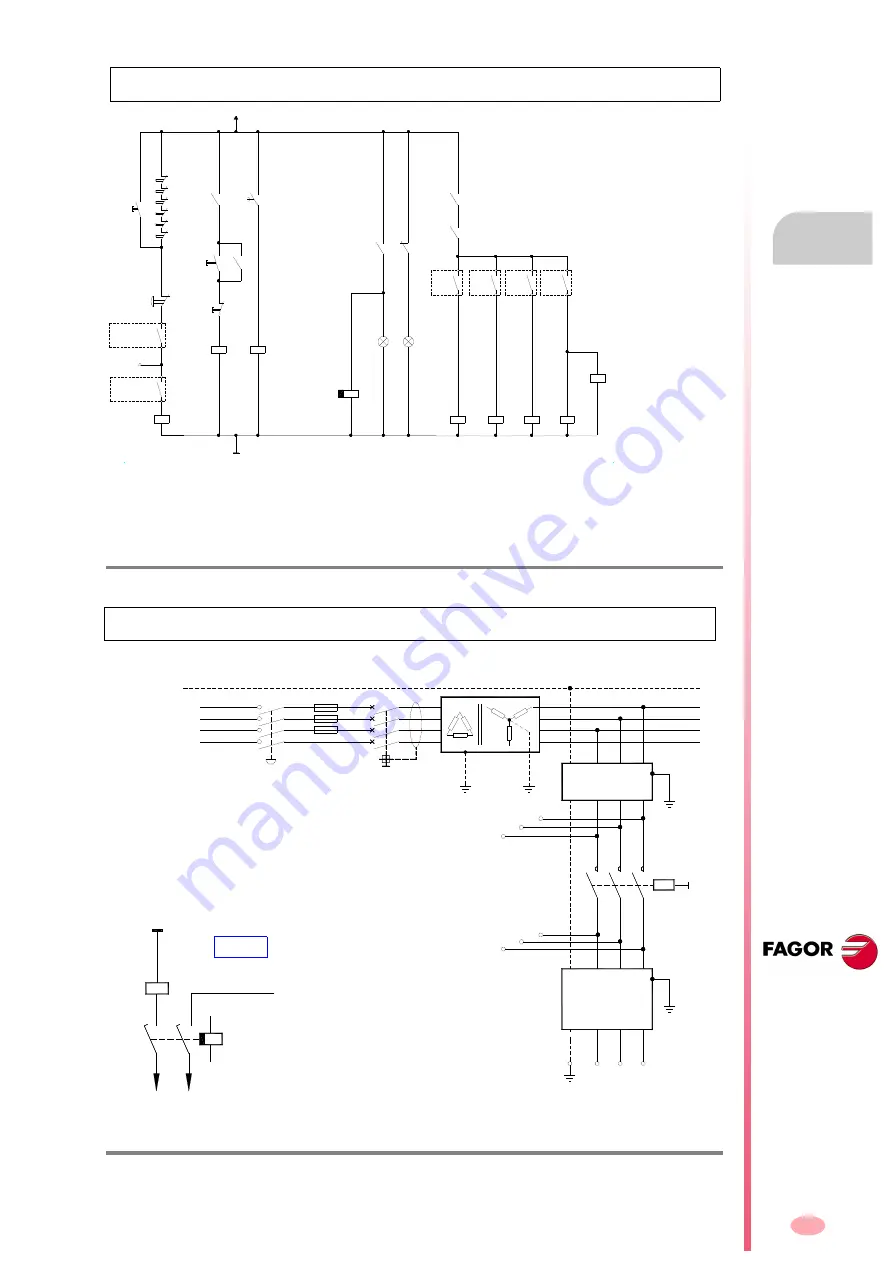
Connection diagrams
CON
N
ECTION DIAGRAMS
Di
agrams with an RPS-XX
p
ower supp
ly
10.
345
DDS
HARDWARE
Ref.1310
F. H10/19
System with RPS power supply. Diagram of the maneuver.
F. H10/20
System with RPS power supply. General diagram.
+24VDC
KA3,1
KA1
X+
X-
Y+
Y-
Z+
Z-
ON
KA2
OFF
-KA2
-KM1
SYSTEM
SPEED
ENABLE
EMERG.
STOP
RPS
SYSTEM OK
I1 PLC
CNC EMERG.
O1 PLC
-KA1
EMERGENCY LINE
GND
ON
OFF
TO SPEED ENABLES
KA1
KA2,3
KA2,1
KA2,2
ON
Green
OFF
Red
DELAY OFF
-KA3
DRIVE
ENABLES
-KA7
-KA4
-KA5
-KA6
BRAKE
CONTROL
BRK
(See GP9)
CNC
ENABLE
S
CNC
ENABLE
X
CNC
ENABLE
Y
CNC
ENABLE
Z
t seconds
(See GP9)
Note.
CNC EMERG. will always be assigned to I1/O1 of the PLC with an 8055/55i CNC. With an 8070
CNC, it may be assigned to any I/O of the PLC. The contacts associated with relays - KA2, - KA3, - KA4,
- KA5, - KA6 and - KA7 are shown inside a circle in figure
and the contactor - KM1 in figure
OPERATION DIAGRAM. RPS-XX
Important.
The relay - KA3 acts simultane-
ously upon contact KA3,1 to excite the coil of
contactor - KM1 and upon the auxiliary contact
KA3,2 (see previous figure) associated with
the PWN ENABLE (pin 4 of X6) of the RPS
power supply. Make sure that the time t used
to program the delay of relay - KA3 associated
with contacts KA3,1 and KA3,2 is
greater
than
the braking time (full stop) to permit returning
all the excess energy to mains while braking.
The delay disconnec-
tion time “t” to be pro-
grammed at relay - KA3
must be GREATER
THAN the total amount
o f ti m e r eq u ir e d to
brake the motor to a full
stop.
PE
- S1
- F3
- F4
- F5
MAINS FILTER XXA
CHOKE RPS-XX
w1
v1
u1
w2
v2
u2
L2
L1
L2
L3
TO THE X1 CONNECTOR
RPS-XX POWER SUPPLY
TO THE 1 POWER CONNECTOR
RPS-XX POWER SUPPLY
3x400-460 VAC
3x400-460 VAC
TO CONNECTOR 2 OF THE
RPS-XX POWER SUPPLY
- FEEDBACK CONNECTOR OF THE
AUXILIARY SIGNAL LINE-
3x400-460 VAC
R
S
T
R
S
T
CONTACTOR
KM1
L1
L3
R
S
T
N
INDUCTANCE
- Q1
WARNING.
When using an isolating transformer, the secondary must be
connected in star and its middle point must be connected to GND.
IT A MUST TO USE FUSES
POWER MAINS
MECHANICAL
MAIN SWITCH
DIFFERENTIAL
BREAKER
ASSOCIATED RELAY,
TWO NORMALLY OPEN
CONTACTS WITH
DELAYED SWITCH-OFF
AT PIN 4 OF X6
24VDC
-KA3
PWM ENABLE
24VDC
-KM1
GND
KA3,1
KA3,2
GENERAL DIAGRAM. RPS-XX
Note 1.
Observe that having the main switch - S1
closed, although the power contactor - KM1 is
open, the internal auxiliary power supply remains
connected to the unit through its connector X1 to
feed the control circuits of the drive.
See fig.a
fig.a
Summary of Contents for DDS
Page 1: ...DRIVE DDS Hardware manual Ref 1310...
Page 6: ...I 6 DDS HARDWARE Ref 1310...
Page 9: ......
Page 10: ......
Page 11: ......
Page 12: ......
Page 16: ...16 Ref 1310 DDS HARDWARE...
Page 30: ...1 DESCRIPTION 30 Description DDS HARDWARE Ref 1310...
Page 94: ...2 POWER SUPPLIES 94 Power supplies DDS HARDWARE Ref 1310...
Page 188: ...3 DRIVE MODULES 188 Drive modules DDS HARDWARE Ref 1310...
Page 204: ...4 AUXILIARY MODULES 204 Auxiliary modules DDS HARDWARE Ref 1310...
Page 232: ...SELECTING CRITERIA 5 232 Selection criteria DDS HARDWARE Ref 1310...
Page 266: ...7 CABLES 266 Cables DDS HARDWARE Ref 1310...
Page 312: ...8 INSTALLATION 312 Installation DDS HARDWARE Ref 1310...
Page 326: ...9 FUNCTIONAL SAFETY 326 Functional safety DDS HARDWARE Ref 1310...
Page 354: ...10 CONNECTION DIAGRAMS 354 Connection diagrams DDS HARDWARE Ref 1310...
Page 378: ...12 SALES REFERENCES 378 Sales references DDS HARDWARE Ref 1310...
Page 384: ...13 COMPATIBILITY 384 Compatibility DDS HARDWARE Ref 1310...
Page 385: ......