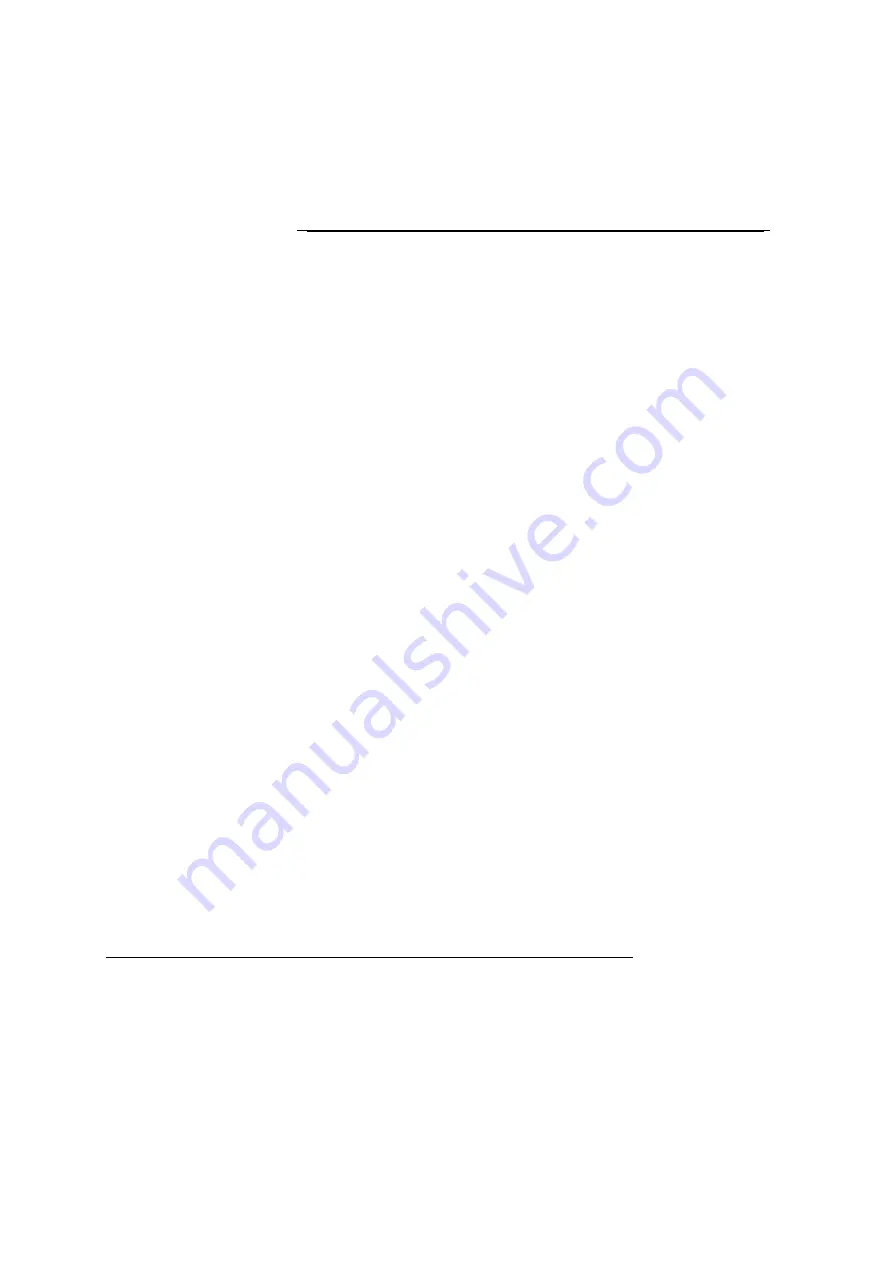
Footwear Machine Manufacturers
FALAN
Instruction Manual
(
ENGLISH - Translation from Italian Original Language
)
for Electronic Two-Thread Lockstitch Sewing Machine for Soles model F525 N
MODEL
: F525 N
SERIAL N.
: ...............
YEAR OF CONSTRUCTION : ...............
Manual Revision Number :
3
Builder Company and authorized to supply the Technical Documentation :
FALAN s.r.l.
Via Buscaglia, 14 - 27029 VIGEVANO (ITALIA)
Tel. +39 0381 346373
Fax +39 0381 346375
Codice fiscale/Partita I.V.A. 00293540183
INTERNET: http://www.falan.it
E-mail: info@falan.it
Generated by Foxit PDF Creator © Foxit Software
http://www.foxitsoftware.com For evaluation only.