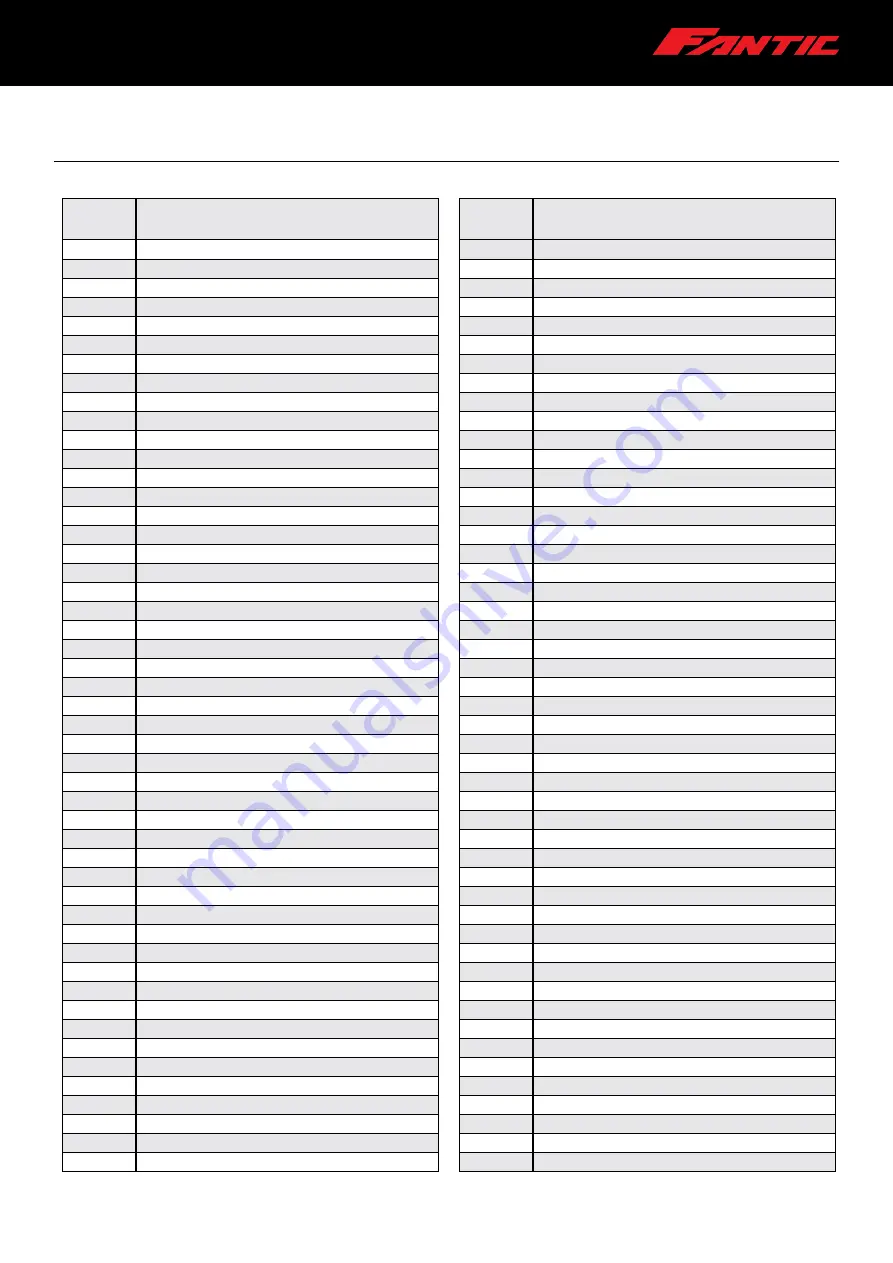
85
WORKSHOP MANUAL
TL 250
CHAPTER 15
ELECTRICAL DEVICES
11 Diagnostics
114
WORKSHOP MANUAL
CHAPTER 11
DIAGNOSTICS
250 Rev00 / 2019
ERROR
CODE
ERROR
P2288
Injector Control Pressure Too High
P2289
Injector Control Pressure Too High - Engine Off
P228A
Fuel Pressure Regulator 1 - Forced Engine Shutdown
P228B
Fuel Pressure Regulator 2 - Forced Engine Shutdown
P228C
Fuel Pressure Regulator 1 Exceeded Control Limits - Pressure Too Low
P228D
Fuel Pressure Regulator 1 Exceeded Control Limits - Pressure Too High
P228E
Fuel Pressure Regulator 1 Exceeded Learning Limits - Too Low
P228F
Fuel Pressure Regulator 1 Exceeded Learning Limits - Too High
P2290
Injector Control Pressure Too Low
P2291
Injector Control Pressure Too Low - Engine Cranking
P2292
Injector Control Pressure Erratic
P2293
Fuel Pressure Regulator 2 Performance
P2294
Fuel Pressure Regulator 2 Control Circuit/Open
P2295
Fuel Pressure Regulator 2 Control Circuit Low
P2296
Fuel Pressure Regulator 2 Control Circuit High
P2297
Oxygen Sensor Out of Range During Deceleration (Bank 1 Sensor 2)
P2298
Oxygen Sensor Out of Range During Deceleration (Bank 2 Sensor 1)
P229A
Fuel Pressure Regulator Exceeded Control Limits - Pressure Too Low
P229B
Fuel Pressure Regulator Exceeded Control Limits - Pressure Too High
P229C
Fuel Pressure Regulator Exceeded Learning Limits - Too Low
P229D
Fuel Pressure Regulator Exceeded Learning Limits - Too High
P2300
Ignition coils
P2301
Ignition coils
P2302
Ignition Coil A Secondary Circuit
P2303
Ignition Coil B Primary Control Circuit Low
P2304
Ignition Coil B Primary Control Circuit High
P2305
Ignition Coil B Secondary Circuit
P2306
Ignition Coil C Primary Control Circuit Low
P2307
Ignition Coil C Primary Control Circuit High
P2308
Ignition Coil C Secondary Circuit
P2309
Ignition Coil D Primary Control Circuit Low
P2310
Ignition Coil D Primary Control Circuit High
P2311
Ignition Coil D Secondary Circuit
P2312
Ignition Coil E Primary Control Circuit Low
P2313
Ignition Coil E Primary Control Circuit High
P2314
Ignition Coil E Secondary Circuit
P2315
Ignition Coil F Primary Control Circuit Low
P2316
Ignition Coil F Primary Control Circuit High
P2317
Ignition Coil F Secondary Circuit
P2318
Ignition Coil G Primary Control Circuit Low
P2319
Ignition Coil G Primary Control Circuit High
P2320
Ignition Coil G Secondary Circuit
P2321
Ignition Coil H Primary Control Circuit Low
P2322
Ignition Coil H Primary Control Circuit High
P2323
Ignition Coil H Secondary Circuit
P2324
Ignition Coil I Primary Control Circuit Low
P2325
Ignition Coil I Primary Control Circuit High
P2326
Ignition Coil I Secondary Circuit
P2327
Ignition Coil J Primary Control Circuit Low
ERROR
CODE
ERROR
P2235
Heated oxygen sensor heater (HO2S) Bank 2 Sensor 2
P2236
Heated oxygen sensor heater (HO2S) Bank 2 Sensor 3
P2237
Heated oxygen sensor current (bank 1 sensor 1)
P2238
Heated oxygen sensor current (bank 1 sensor 1)
P2239
Heated oxygen sensor current (bank 1 sensor 1)
P2240
Heated oxygen sensor current (bank 2 sensor 1)
P2241
Heated oxygen sensor current (bank 2 sensor 1)
P2242
Heated oxygen sensor current (bank 2 sensor 1)
P2243
Oxygen sensor reference voltage circuit (Bank 1 sensor 1)
P2244
Oxygen sensor reference voltage, Performance - Bank 1, Sensor 1
P2245
Oxygen sensor reference voltage circuit low - Bank 1, Sensor 1
P2246
Oxygen sensor reference voltage circuit, high - Bank 1 Sensor 1
P2247
Oxygen sensor reference voltage circuit, open - Bank 2, Sensor 1
P2248
Oxygen sensor reference voltage, Performance - Bank 2, Sensor 1
P2249
Oxygen sensor reference voltage circuit, low- Bank 2 Sensor 1
P224F
Barometric pressure sensor “B” circuit
P2250
Oxygen sensor reference voltage circuit, high - Bank 2 Sensor 1
P2251
Heated oxygen sensor current (bank 1 sensor 1)
P2252
Heated oxygen sensor current (bank 1 sensor 1)
P2253
Heated oxygen sensor current (bank 1 sensor 1)
P2254
Heated oxygen sensor current (bank 2 sensor 1)
P2255
Heated oxygen sensor current (bank 2 sensor 1)
P2256
Heated oxygen sensor current (bank 2 sensor 1)
P2257
Secondary Air Injection System Control A Circuit Low
P2258
Secondary Air Injection System Control A Circuit High
P2259
Secondary Air Injection System Control B Circuit Low
P2260
Secondary Air Injection System Control B Circuit High
P2264
Water in Fuel Sensor Circuit
P2265
Water in Fuel Sensor Circuit Range/Performance
P2266
Water in Fuel Sensor Circuit Low
P2267
Water in Fuel Sensor Circuit High
P2268
Water in Fuel Sensor Circuit Intermittent
P2269
Water in Fuel Condition
P226A
Water in Fuel Lamp Control Circuit
P2270
Oxygen Sensor Signal Biased/Stuck Lean (Bank 1 Sensor 2)
P2271
Oxygen Sensor Signal Biased/Stuck Rich (Bank 1 Sensor 2)
P2272
Oxygen Sensor Signal Biased/Stuck Lean (Bank 2 Sensor 2)
P2273
Oxygen Sensor Signal Biased/Stuck Rich (Bank 2 Sensor 2)
P2274
Oxygen Sensor Signal Biased/Stuck Lean (Bank 1 Sensor 3)
P2275
Oxygen Sensor Signal Biased/Stuck Rich (Bank 1 Sensor 3)
P2276
Oxygen Sensor Signal Biased/Stuck Lean (Bank 2 Sensor 3)
P2277
Oxygen Sensor Signal Biased/Stuck Rich (Bank 2 Sensor 3)
P2278
Oxygen Sensor Signals Swapped (Bank 1 Sensor 3)
P2279
Intake Air System Leak
P2283
Injector Control Pressure Sensor Circuit
P2284
Injector Control Pressure Sensor Circuit Range/Performance
P2285
Injector Control Pressure Sensor Circuit Low
P2286
Injector Control Pressure Sensor Circuit High
P2287
Injector Control Pressure Sensor Circuit Intermittent
Summary of Contents for TL 250
Page 1: ...1 WORKSHOP MANUAL E N...
Page 3: ...WORKSHOP MANUAL TL 250...
Page 11: ...11 WORKSHOP MANUAL TL 250...
Page 30: ...30 WORKSHOP MANUAL TL 250 CHAPTER 6 DASHBOARD 39 GENERAL CONTENT AND CONSULTATION ENGLISH...
Page 49: ...49 49 WORKSHOP MANUAL TL 250...
Page 51: ...51 CHAPTER 15 ELECTRICAL DEVICES 51 WORKSHOP MANUAL TL 250...
Page 136: ...136 136 WORKSHOP MANUAL TL 250...