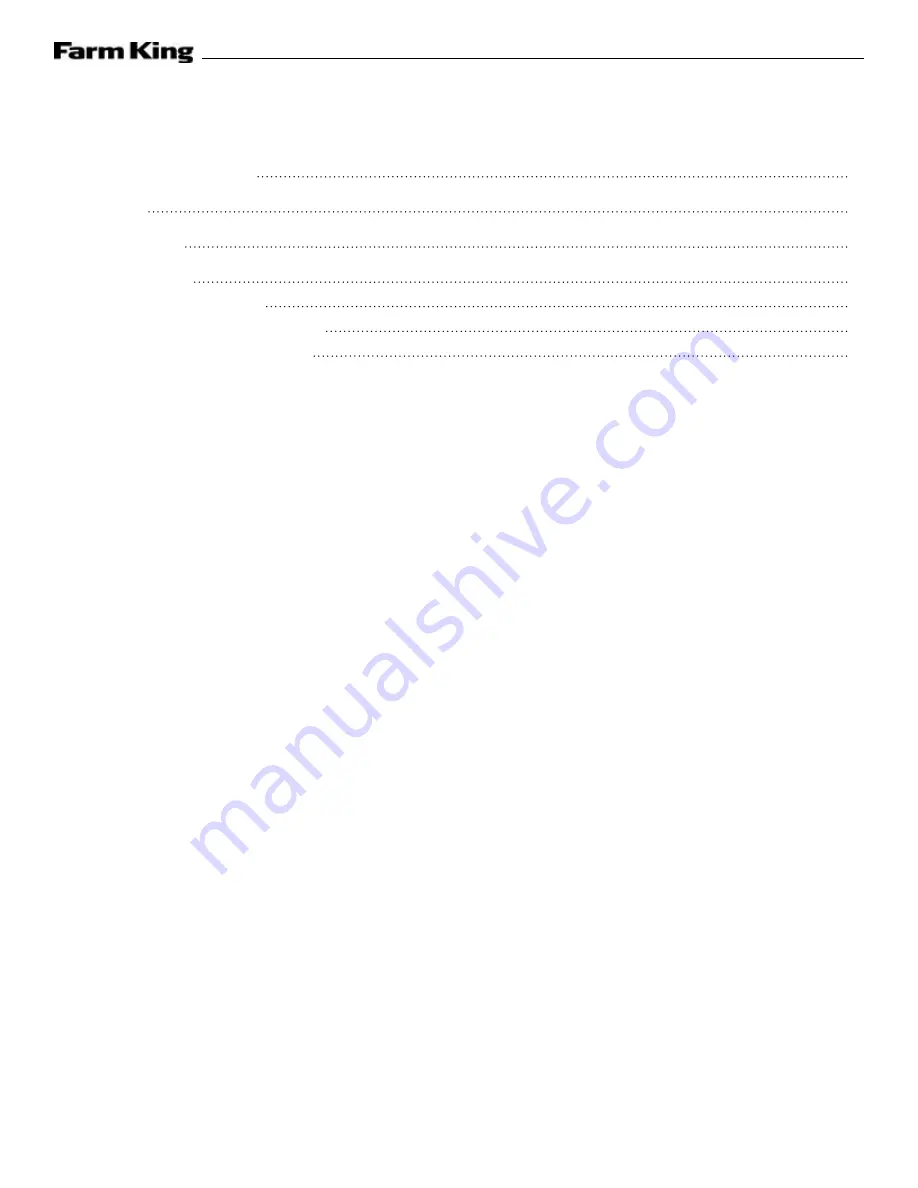
Assembly - 500, 600, 660
21
Assembly
Hydraulic Spout Deflector (Option)
Summary of Contents for 500
Page 1: ...032016 FK311 OPERATOR AND PARTS MANUAL Snowblower Model 500 600 660 ...
Page 2: ......
Page 6: ...Warranty Registration Form 500 600 660 4 ...
Page 8: ...Introduction 500 600 660 6 ...
Page 12: ...Introduction 500 600 660 10 ...
Page 14: ...Safety 500 600 660 12 ...
Page 24: ...Assembly 500 600 660 22 ...
Page 30: ...Assembly 500 600 660 28 ...
Page 32: ...Operation 500 600 660 30 ...
Page 44: ...Operation 500 600 660 42 ...
Page 46: ...Maintenance 500 600 660 44 ...
Page 52: ...Maintenance 500 600 660 50 ...
Page 54: ...Parts Identification 500 600 660 52 ...
Page 66: ...Specifications And Shipping Kit Numbers 500 600 660 64 ...
Page 68: ...Specifications And Shipping Kit Numbers 500 600 660 66 HardwareTorque Values Metric Chart ...
Page 69: ...Specifications And Shipping Kit Numbers 500 600 660 67 Imperial Chart ...
Page 70: ...Specifications And Shipping Kit Numbers 500 600 660 68 ...
Page 72: ...Warranty 500 600 660 70 ...
Page 75: ......