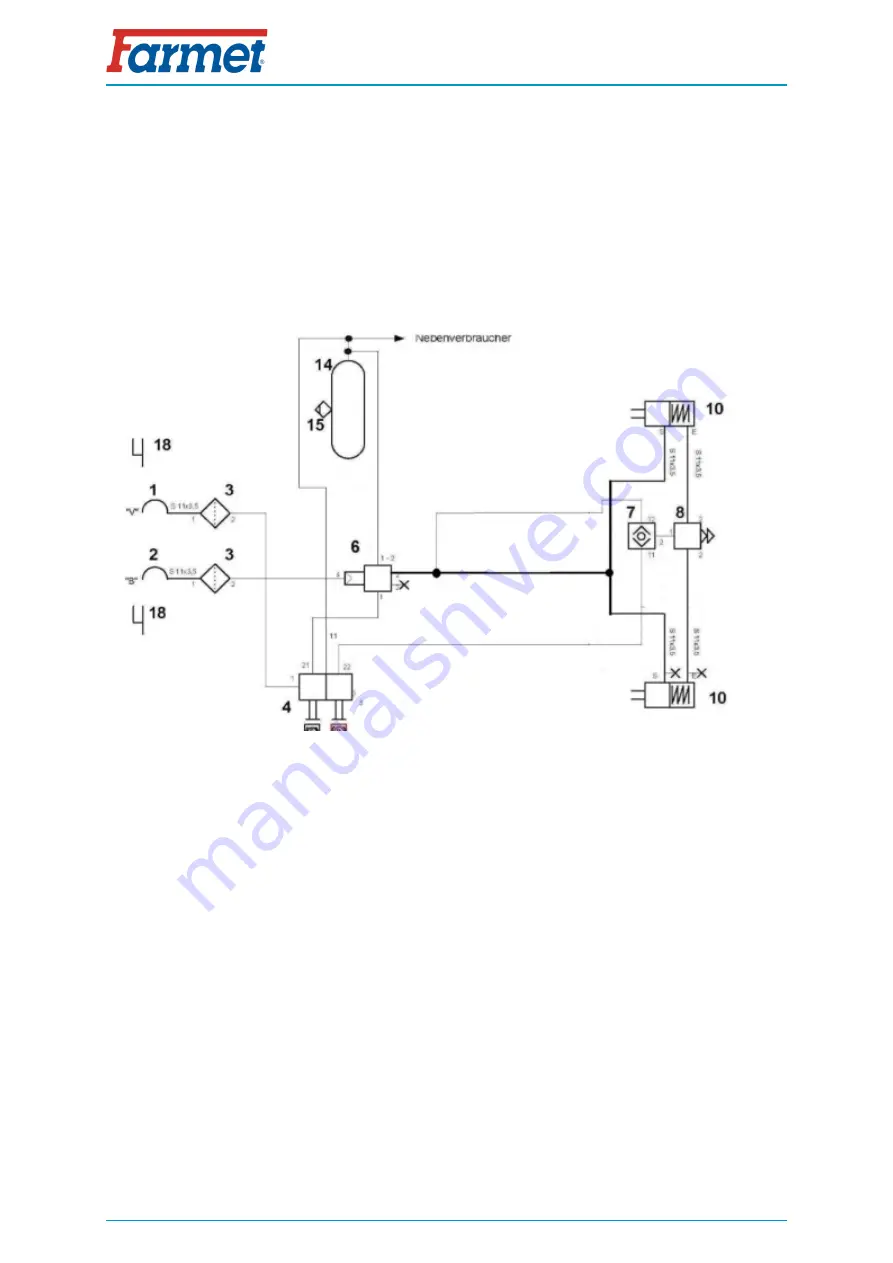
8.4 Brake distribution of the machine
•
The standard version of the machine includes a single-circuit two-line braking system by
KNORR BREMSE.
•
Braking is provided by spring brake cylinders – the parking brake is implemented inside and it is
automatic (controlled by a button, see below).
•
ATTENTION !!! The parking brake is activated automatically when there is a leak of air from the
system and physical brake release is only possible mechanically, see below.
Brake distribution diagram
1.
Quick-coupler – red line
8.
Jettisoning valve
2.
Quick-coupler – yellow line
10.
Combined membrane brake cylinder Type 24/30
3.
Air filter
14.
Air tank 40 l
4.
Control valve of the manual brake
15.
Bleeding valve
6.
Brake valve
18.
Quick-coupler holder
7.
Two-way valve
35
|
59
Summary of Contents for FANTOM 1050 PRO
Page 2: ...2 59 Prepared by Technical Department Farmet a s on 11 7 2019 changes reserved ...
Page 4: ...PREFACE 4 59 IMPORTANT READ CAREFULLY BEFORE USE KEEP FOR FUTURE REFERENCE ...
Page 16: ...WORK SAFETY LABELS FANTOM 1250 PRO 16 59 ...
Page 30: ...COMMISSIONING Machine position for folding Machine position for unfolding 30 59 ...