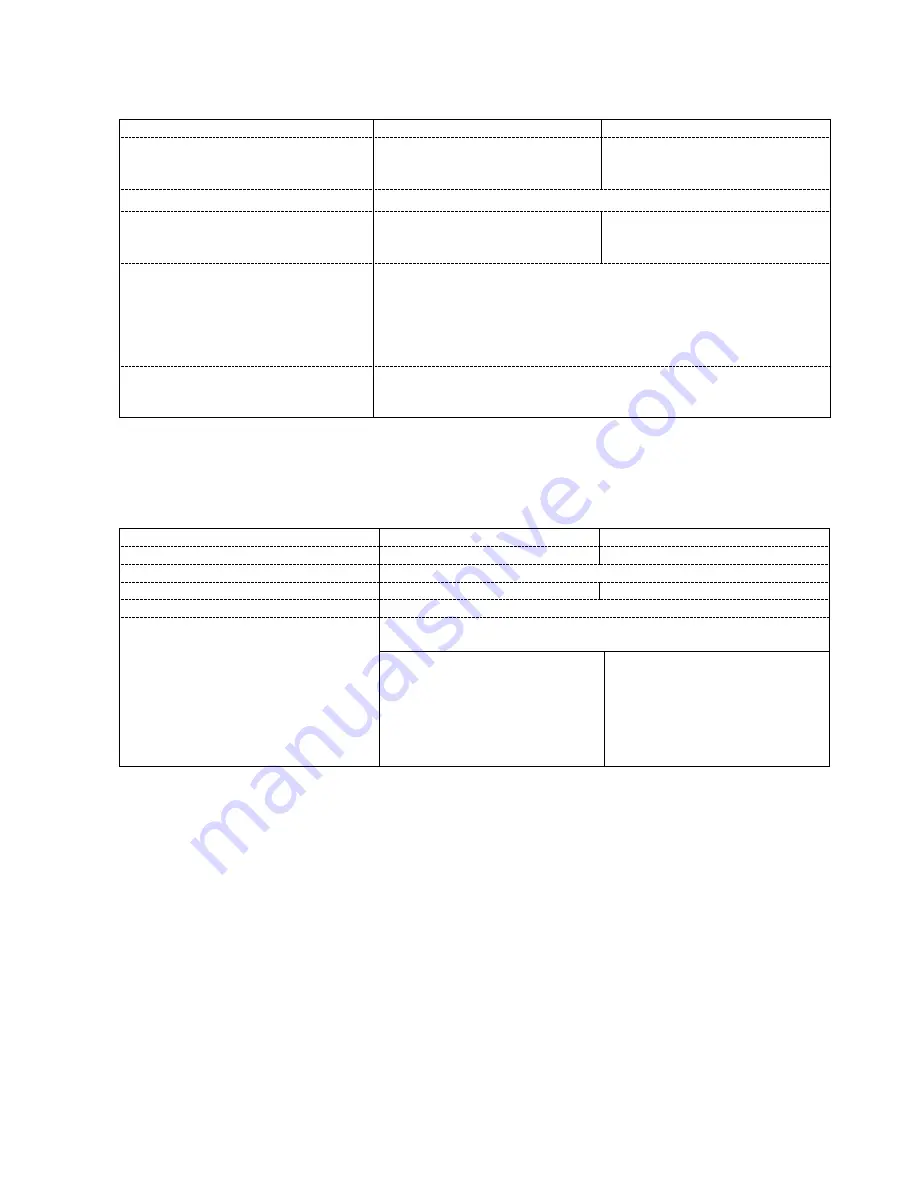
17
2.10.
Tractor weight.
Weight of tractor in running order,
kg
3585 kg
3308 kg
Weight distribution on axle, kg:
front
rear
1470 kg
2115 kg
1204 kg
2104 kg
Maximum permissible tractor weight kg
6000 kg
Weight distribution on axle kg:
front
rear
1650 kg
4350 kg
1500 kg
4500 kg
Maximum mass of the trailer
kg:
Unbraked trailer towable mass
Unbraked agricultural implement
Inertia braked towable mass
Independently braked towable mass
Towable mass fitted with air braking
1500 kg
3000 kg
5000 kg
5000 kg
12500 kg
Ballast weights
Front axle
6 x 22 + 1 x 40 = 172 kg
Rear axle
2 x 39 + 4 x 32 = 206 kg
2.11. Tractor dimensions.
Overall length, mm
3725
4190 mm
3710
4185 mm
Overall width, mm
1939
2375 mm
1950
2350 mm
Overall height, mm
2490
2505 mm
Wheelbase, mm
2314 mm
2413mm
Ground clearance, mm
390
405 mm
Minimum turning circle without
independent braking, mm:
to the left
front drive engaged
front drive disengaged
to the right
front drive engaged
front drive disengaged
With wheel track:
front
– 1560; rear – 1508
10100 mm
9350 mm
9900 mm
9150 mm
7710 mm
7600 mm