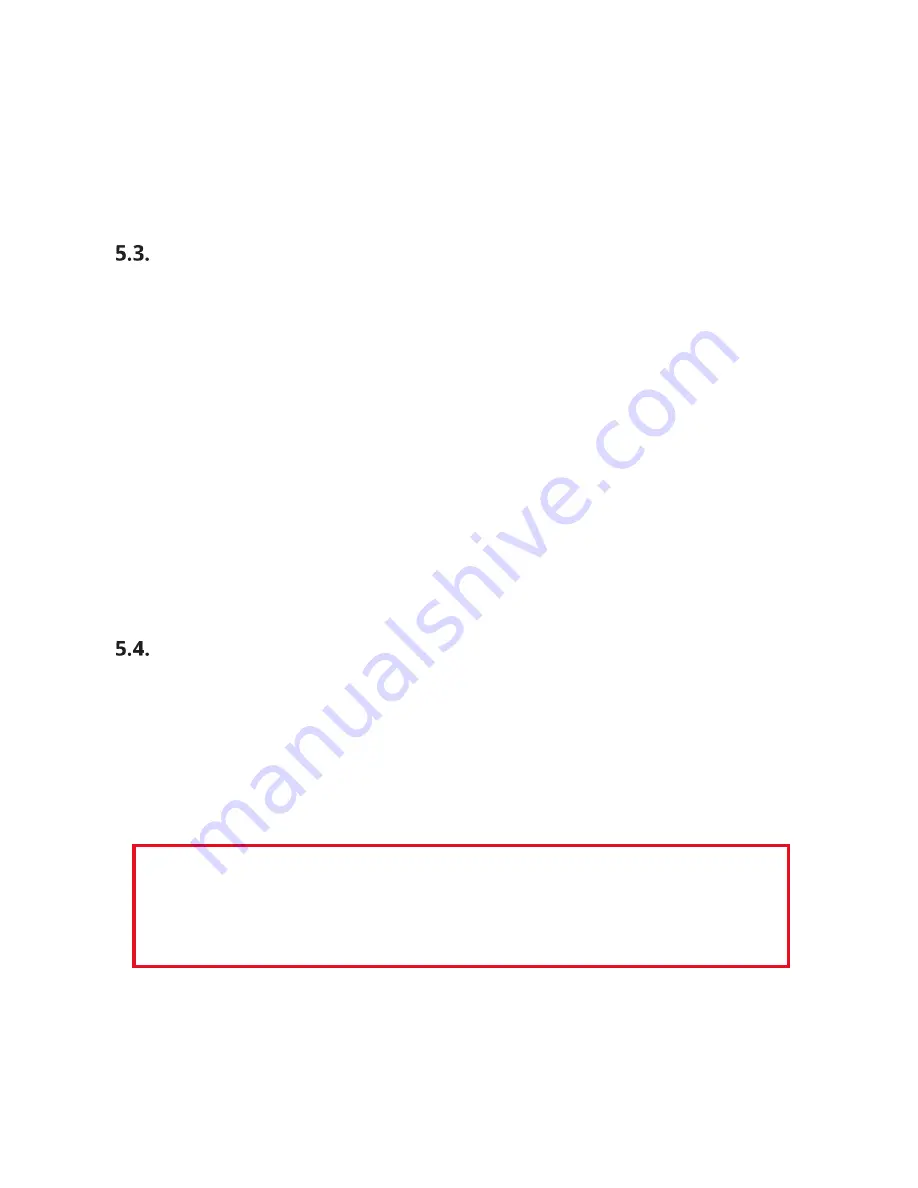
Original notice – User’s manual
14
1. Check that the load capacity of the van is sufficient for the device weight.
2. It is advisable to use the supplied backplates for fixing to the floor (eg: a plate
with a thickness of 5 mm or more). It is necessary to fix the device to the 6
fixing points.
3. Use M10 anchor screws and check that the floor has sufficient strength.
Ventilation
Ventilation must be installed in the van and must have adequate opening to
ensure evacuation of heat. It must have a flow rate of 15 to 20% greater than the
amount of air required for the overall cooling of all installed components.
For a good ventilation of the system in a van, it is necessary to provide two
ventilation grids:
Air intake: 400 x 400 mm located at the height and in the axis of the air intake
of the compressor on the flywheel side of the compressor block
Air extraction: 2 solutions depending on use:
o
400 mm x 300 mm being in the high position of the same side and in the
axis of the preceding one
o
To ensure optimum performance and performance, forced ventilation (eg:
fan motor) must be installed on the roof of the truck to extract heat if it is
used for more than 30°C outside.
Exhaust
In order to extract all the exhaust gases in a truck, an exhaust hose must be
installed.
The exhaust hose and exhaust pipe delivered with the device must be used. This
hose must take the shortest way to get out of the truck. To do this, it is obligatory
to drill a hole on the floor of the truck in order to cross with this hose through the
pipe.
DANGER
Ensure that the exhaust hose is not directed towards flammable materials.
Remove covers such as crates, containers, etc. Because the compressor
inevitably suffers damage during service. In addition, the risk of fire is very
high.