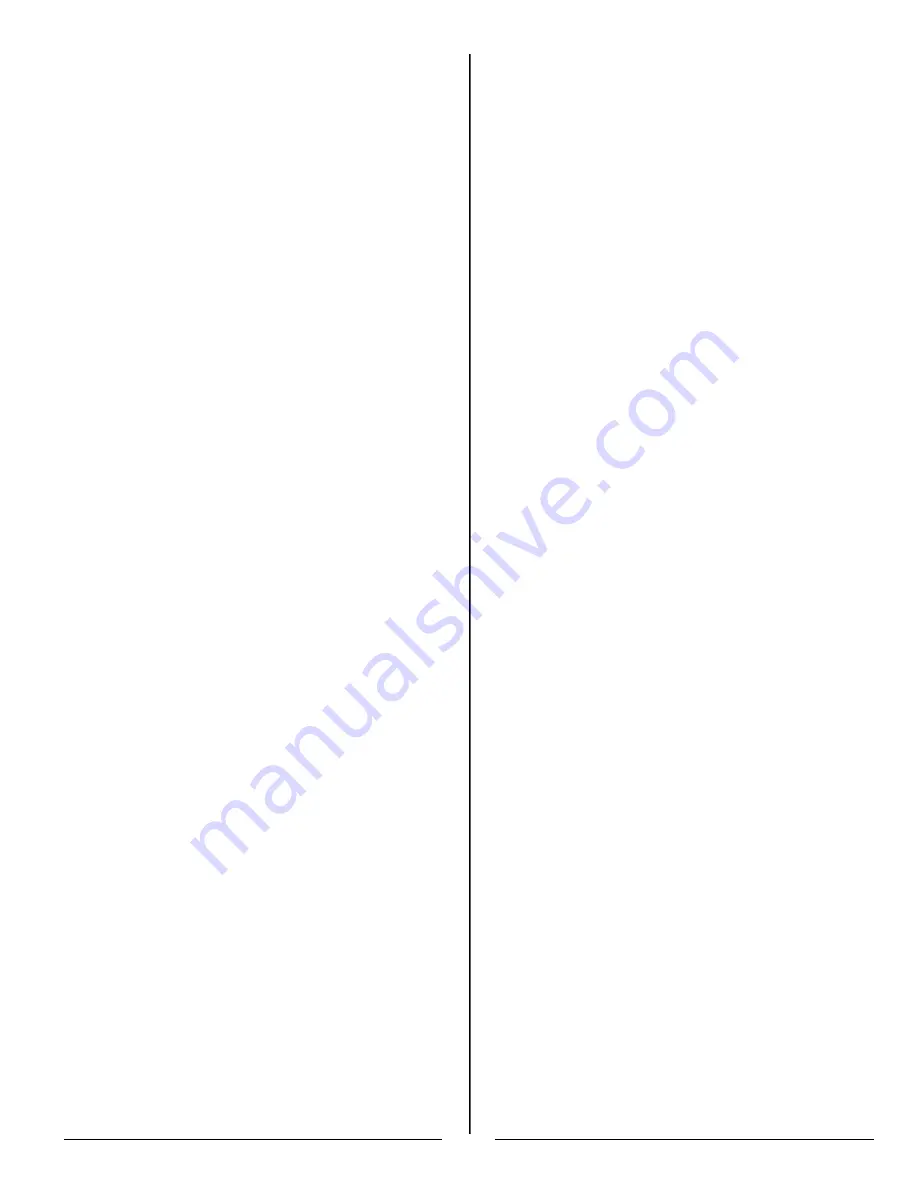
11
2. Safety
^
YOU
are responsible for the
SAFE
operation and
maintenance of your Fast Manufacturing, Inc. Sprayer.
YOU must ensure that you and anyone else who is going
to operate, maintain or work around the Sprayer be familiar
with the operating and maintenance procedures and related
SAFETY
information contained in this manual. This manual
will take you step-by-step through your working day and
alerts you to good safety practices that should be adhered
to while operating the sprayer.
Remember,
YOU
are the key to safety. Good safety practices
not only protect you but also the people around you. Make
these practices a working part of your safety program.
Be certain that
EVERYONE
operating this equipment is
familiar with the recommended operating and maintenance
procedures and follows all the safety precautions. Most
accidents can be prevented. Do not risk injury or death by
ignoring good safety practices.
• Sprayer owners must give operating instructions
to operators or employees before allowing them to
operate the unit, and at least annually thereafter per
OSHA regulation 1928.57.
• The most important safety device on this equipment is a
SAFE
operator. It is the operator’s responsibility to read
and understand
ALL
Safety and Operating instructions
in the manual and to follow these. All accidents can be
avoided.
•
A person who has not read and understood all operating
and safety instructions is not qualified to operate the
machine. An untrained operator exposes himself and
bystanders to possible serious injury or death.
• Do not modify the equipment in any way. Unauthorized
modification may impair the function and/or safety and
could affect the life of the equipment.
• Think SAFETY! Work SAFELY!
2.1 Safety Alert Symbol And Signal
Words
This symbol means ATTENTION! BECOME ALERT! YOUR
SAFETY IS INVOLVED!
^
The level of risk is indicated by the following signal words:
^
DANGER
DANGER - Indicates a hazardous situation,
which, if not avoided, WILL result in death or
serious injury.
^
WARNING
WARNING - Indicates a hazardous situation,
which, if not avoided, could result in death or
serious injury.
^
CAUTION
CAUTION - Indicates a hazardous situation,
which, if not avoided, could result in minor or
moderate injury.
NOTICE
NOTICE
- Indicates a situation that could
result in damage to the equipment or other
property.
Summary of Contents for BW750
Page 18: ...18...
Page 19: ...19 Decal A Decal B Decal C Decal D...
Page 20: ...20 Decal E Decal F Decal G Decal H Decal I Decal J...
Page 21: ...21 Decal K Decal L...
Page 36: ...36 9 6 Spray Tip Wear...
Page 43: ...43 9 8 TeeJet Air Induction Spray Tips 9 8 1 20 Inch Spacing At Various Speeds And Pressures...
Page 81: ...81 12 3 Raven Console Calibration Information...
Page 83: ...83 Notes...