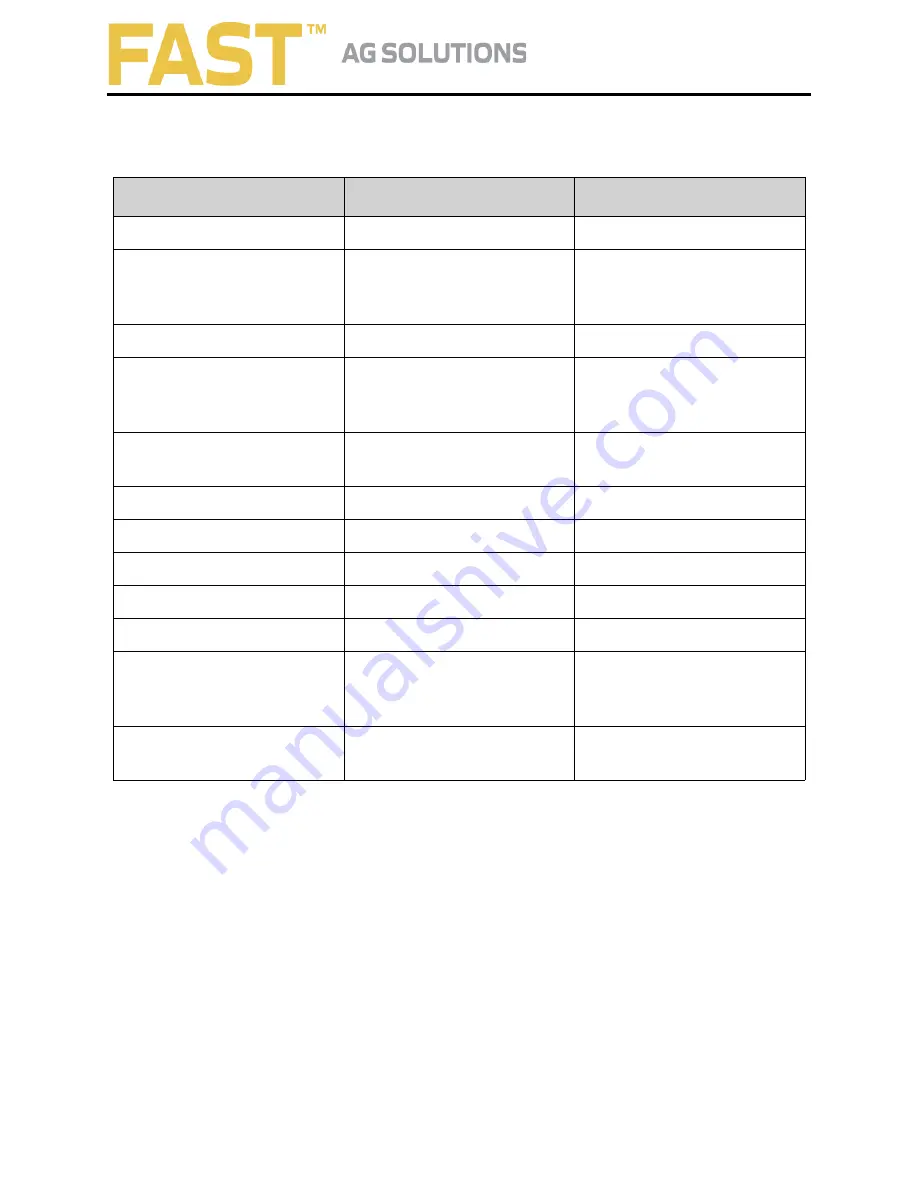
TROUBLESHOOTING
PAGE 72
TROUBLESHOOTING
Problem
Cause
Solution
Sprayer pressure too high
Return hose plugged.
Clean or replace hose.
Wrong agitation value set-
ting.
Open agitation valve
slightly until pressure goes
to required range.
Sprayer pressure too low
Return hose plugged.
Clean or replace hose.
Wrong agitation valve set-
ting.
Close agitation valve
slightly until pressure goes
to required range.
High spray drift
Boom set too high.
Lower boom.
Too windy.
Wait for wind to calm.
Boom is bouncing
Traveling too fast.
Slow down.
Main wing wobbles
Clutch too loose.
Tighten clutch bolts.
Gas shock malfunctioning. Replace gas shock.
Main wing slams hard into
folded or unfolded posi-
tion.
Gas shock malfunctioning. Replace gas shock.
Flip wing bounces in trans-
port or field position.
Gas shock malfunctioning. Replace gas shock.
Summary of Contents for UT3P
Page 1: ...820037 FAST UT3P Sprayer 9 20 2018 FAST UT3P Sprayer OPERATION AND MAINTENANCE MANUAL...
Page 2: ...820037 FAST UT3P Sprayer 9 20 2018...
Page 5: ...UT3P DELIVERY INSPECTION CHECKLIST PAGE 2 This page intentionally left blank...
Page 19: ...MAJOR COMPONENTS PAGE 16 This page intentionally left blank...
Page 45: ...OPERATION PAGE 42 This page intentionally left blank...
Page 61: ...PAGE 58 This page intentionally left blank...
Page 83: ...820037 9 20 2018...
Page 84: ...820037 9 20 2018...