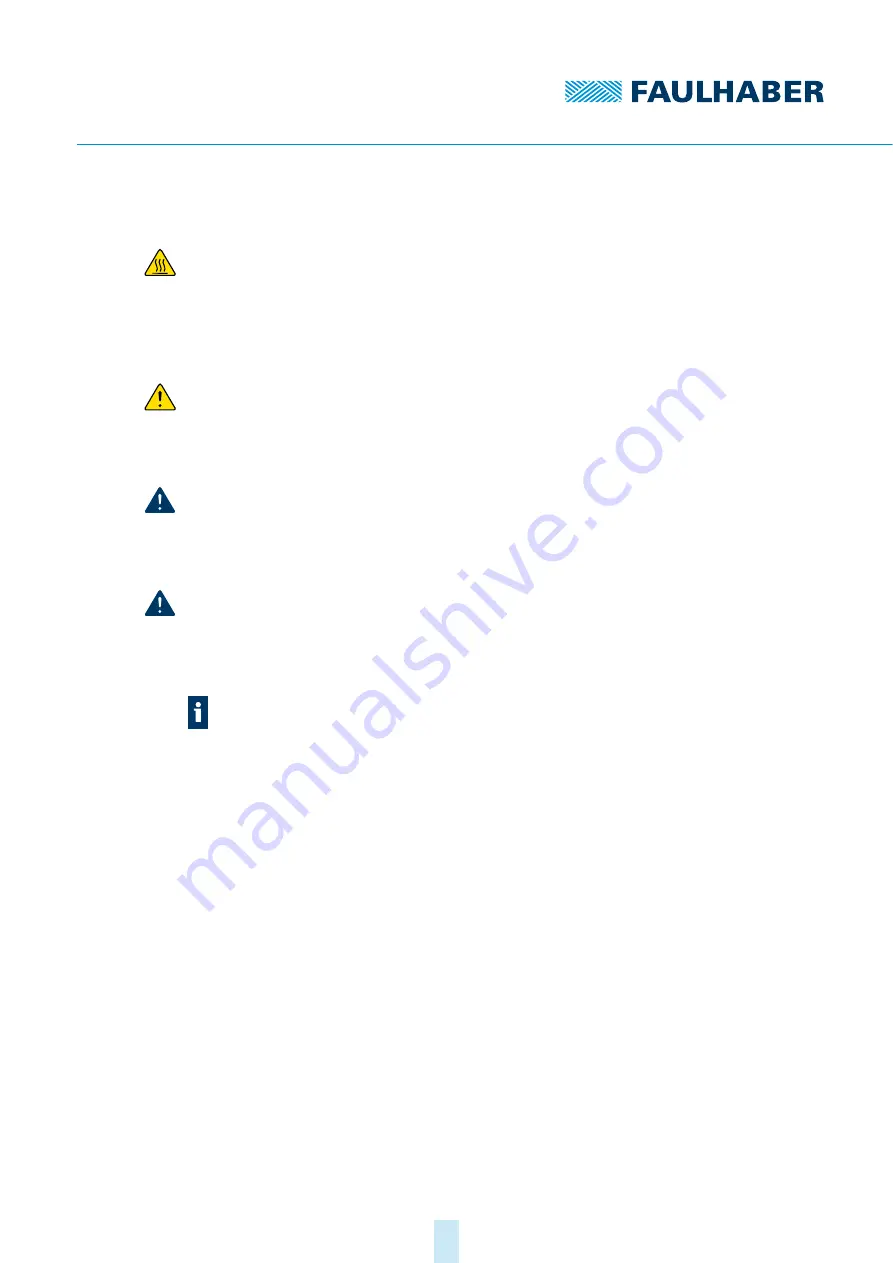
2nd edition, 31-03-2020
7000.05061, 2nd edition, 31-03-2020
7000.05061
Commissioning
38
6
Commissioning
CAUTION!
Hazards due to hot surfaces.
Depending on the load and ambient temperature, the motor can overheat.
Allow the motor to cool down after operation.
Be sure to wear protective gloves when touching the motor shortly after operation.
CAUTION!
Risk of injury caused by protruding, rotating or moving parts of the driven mechanical
units.
Attach suitable guards.
NOTICE!
Damage to the motor and/or Speed Controller as a result of incorrectly set control parame-
ters.
Before commissioning, check and if necessary adjust the configured parameters.
NOTICE!
Rapid, repeated switching of the motor's direction of rotation (reversing operation) can
damage the electronics.
Do not use the Speed Controller for reversing operation.
Controller parameters are preset at the factory. The controller can optionally be optimised
for specific applications. In this case, the digital controller operates at a sampling rate of
500
μ
s. Controller optimisation performed when commissioning the motor is described
below.
Motor is mounted as per the specifications (see chap. 4, p. 14).
Motor is electrically connected as per the specifications (see chap. 4.2.2, p. 18).
Connected mechanical components are mounted in such a way that they cannot
become jammed.
Shaft load (axial, radial, torque) is within the specified values.
1. Set the initial configuration.
2. Increase the controller gain (proportional component V).
3. Increase the speed jump from 1/3 of the maximum speed to 2/3 speed.
4. Set the speed jump from 2/3 of the maximum speed to 1/3 and monitor the motor's
behaviour.
5. Repeat steps 2 to 4 until the controller becomes unstable.
The connections U
P
and U
mot
can be supplied with power from the same power supply
unit.
Make sure that the output of the power supply unit is sufficient for supplying power to
the Speed Controller and the connected motor.