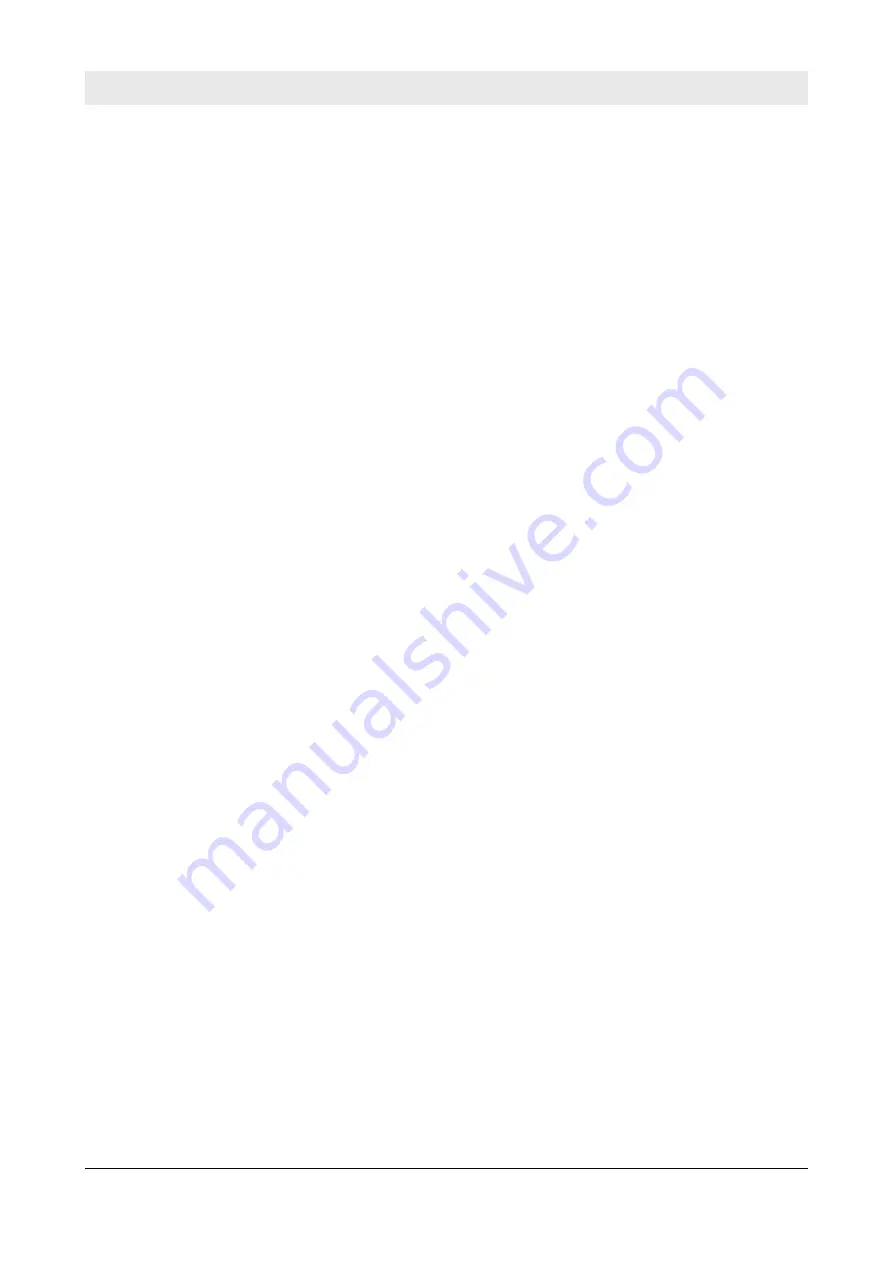
3.7 Operation
3.7.1 Persons in the danger area
Before taking up work, also after breaks, you should always con-
vince yourself that the danger zone is free of persons or obstruc-
tions.
Give warning signals, if necessary. Stop work immediately if per-
sons remain in the danger zone, despite the warning.
3.7.2 Operation
Steer the machine only be the steering bow.
Guide the machine so hat your hands do not hit against solid
objects.
Watch out for unusual noises and development of smoke. Perform
trouble shooting and have the fault corrected.
3.7.3 Parking the machine
Park the machine on horizontal, level, firm ground.
Before leaving the machine:
n
Shut down the engine,
n
Secure the machine against accidental tipping over,
n
Secure the machine against unauthorized use.
Mark machines, which could be in the way, with a clearly visible
sign.
Concerning your safety – Operation
BP 25/50
29
Go
to
Discount-Equipment.com
to
order
your
parts