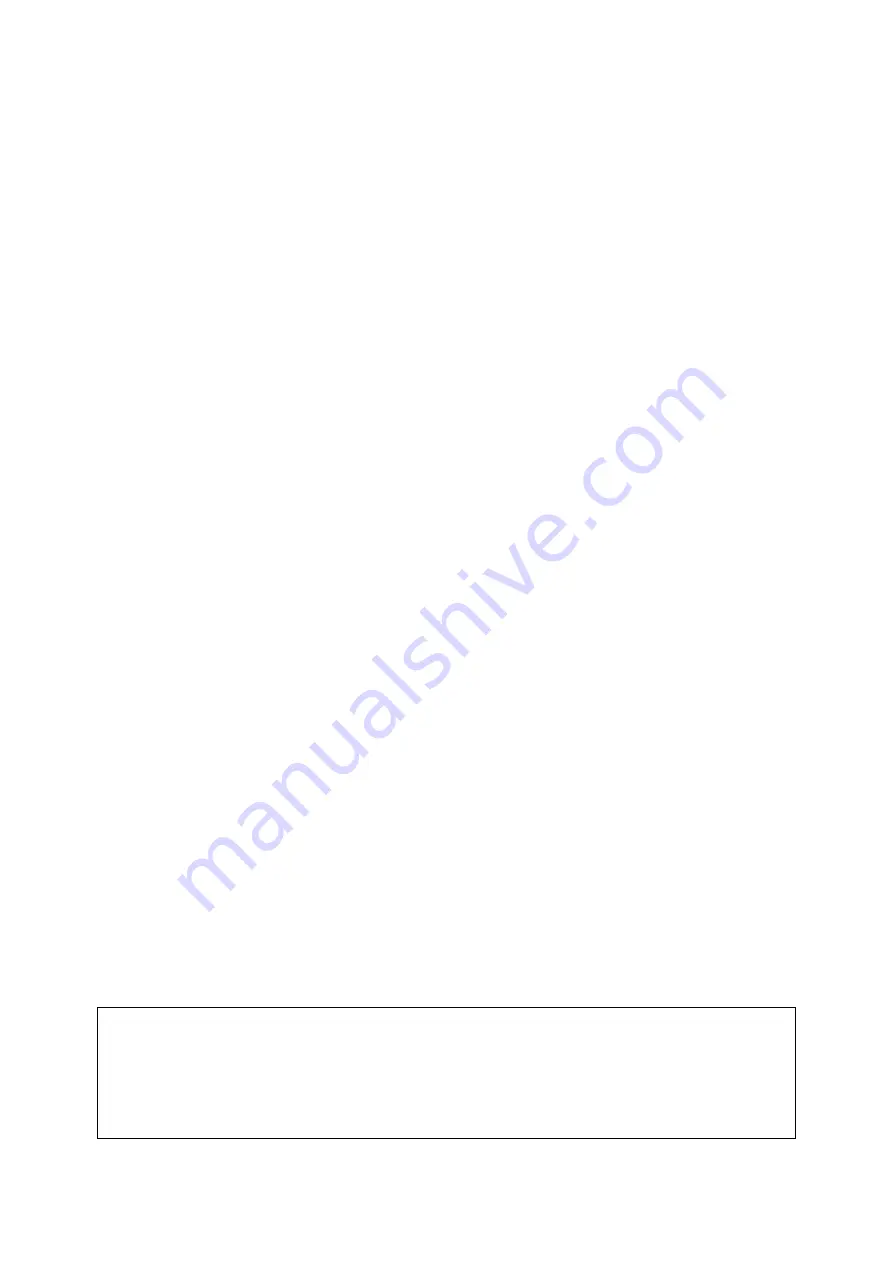
7
-Between 1750-3140 W/m³ specific load the room must be ventilated to another room by 2 pcs. of
non-lockable vents. The cross section of these must be at least 1510 cm² and there must be a
minimum of 1,8 m vertical distance between them. In this case the next parameters have to be
realized:
-total specific load must be under than 1250W/m³.
-total cross section (of door or window) opening to open air or staircase must be 1,3m².
-a card prohibiting covering of vents is to be placed in the room. Under 1750W/m³ specific load
there is no need for airing if the room has a door opening to open air or a window bigger than
1,3 m² or the door opens to a room having this kind of window. Otherwise ventilation is to be
realized according to points a) and b). (The shut-off device must not be leakproof).
With the exception of bedroom and rooms for constant stay the appliance can be installed in
any kind of room if the following conditions are realized in case of an opened combustion
chamber:
-maximum vertical distance between the boiler and the chimney is 0,2 m.
-vertical distance of lower edge of the boiler from the floor must be 0,4-1,4 m.
-operation and repairability must be ensured. A space of 0,1 m on the sides and 0,8 m on
the front must be left.
-the boiler can only be mounted on a wall made of non-burnable materials (thickness of
wall must be a min. of 0,1 m.)
-gas equipments must not be installed above each other.
-two gas equipments (in one room) can be joined the same chimney provided the vertical
distance of their connections is min. 0,3 m and neither of the appliances exceeds 35 kW
nominal heating capacity.
-it is recommended to make between the upper edge or the deflector of the appliance a
chimney intake, which length is triple of the diameter of the chimney.
-if the boiler is placed into a cabinet, then it is to be built from floor to ceiling, its walls and
door must be made of non-burnable material. If possible, its door should be gridded.
2.4. Flue gas piping
Designing, implementing, method of connecting, dimensioning chimneys are specified by standards of
building. The appliances can be connected to a chimney permitted by the chimney-sweeping
companies. The chimney has to be gas-proof.
A boiler can be installed even in a cellar provided the room is damp-proof and has a solid floor.
-smoke tube must be resistant against mechanical effects (aluminium tube is suitable).
- smoke tube is to be resistant against temperature of flue-gas and accompanying
condensation.
-max. horizontal piping of smoke-tube is 2m.
-diameter of smoke-tube can not be smaller than the connection stub of deflector.
-cross section of quadrangular chimneys must be 10% more than the connection stub of
the appliance.
-above deflector there must be a min. of 3D long straight section. (Hungarian standard).
-material of smoke-pipe should be aluminium sold in trade.
Placement of boilers operated by PB gas
The appliance must not be placed in:
-a cellar if all of its walls and its floor are under ground level.
-a building made of panel units.
-a residential building if there is a cellar or subground floor in it.
-specific weight of PB gas is higher than of air so the general rule is that gas should not be able to set
in druses and canals because it may explode.
Attention
The boiler has got a flue-gas backflow sensor. When it starts operation the boiler stops automatically.
Restart can only be made by manual ignition of pilot flame.
Disabling, damaging and/or demounting of safety system is prohibited!
In case of repeated failures a skilled serviceman must check the chimney.
The producer is not liable for damages caused by faults of installation, incorrect use, changes
made in the appliance or neglecting manufacturer's instructions and valid regulations.