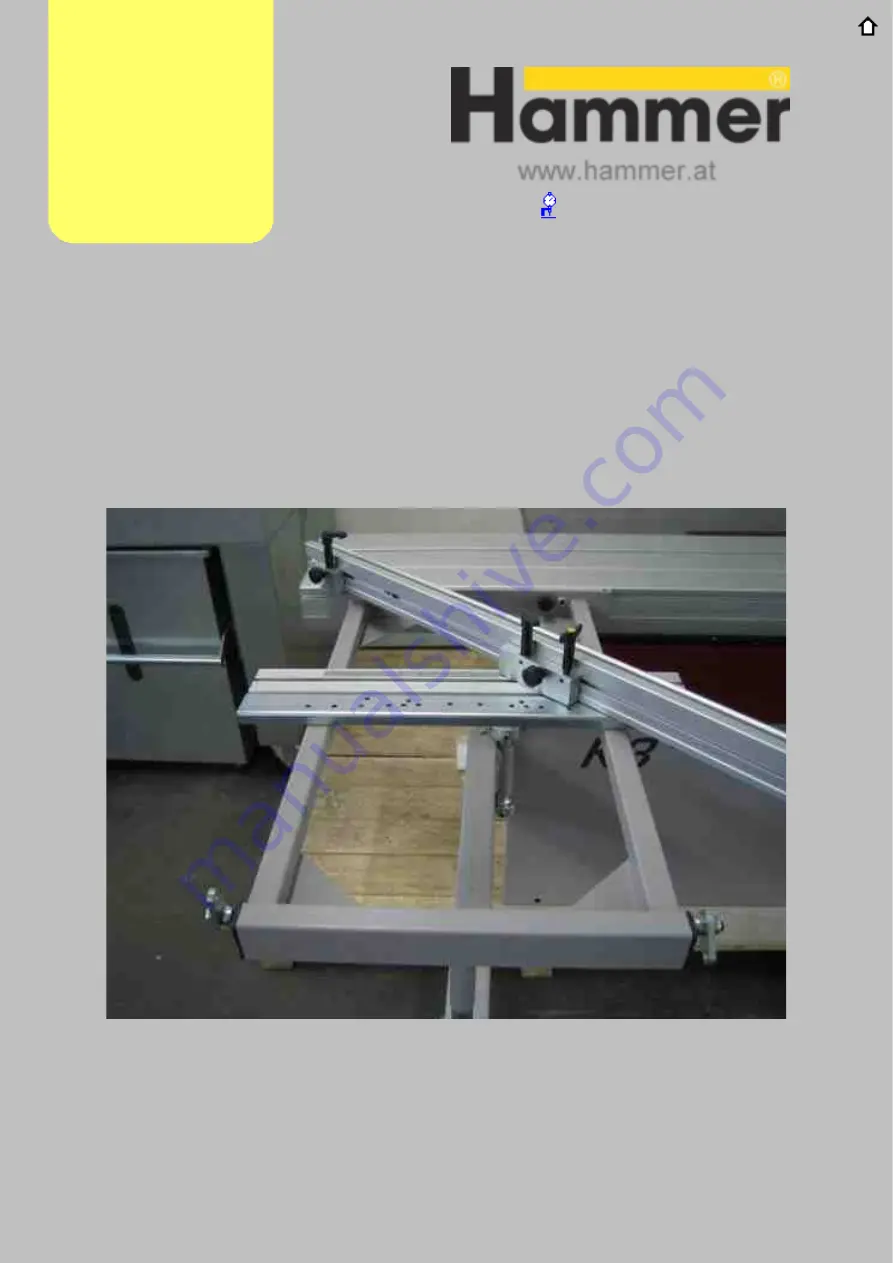
To adjust the angled cut from the outrigger, you can use a dial indicator and a large
45° angle. However, this can be done without the 45° Angle. You will need a
workpiece (say, 3ft x 10”, with at least 1 straight edge), an angle gauge and a 5mm
Allen key.
The first step would be to move the crosscut fence into the 45°position, from the front
of the outrigger (Figure SS08.1). Lock it down and proceed to make a cut through the
workpiece.
Figure SS08.1 From the front of the outrigger
When the cut is made, bring the angle gauge into place along the side previously
against the fence and the new cut side. The offcut can also be used if the angle
gauge does not permit internal 45° measurements of this size. Be sure to use the
same edges (Fenced surface and cut surface). Figure SS08.2 shows the correct
angles to check. Unless you can be certain the two edges are completely parallel, it
is best to check this way so as not to combine errors.
Adjust
ments
Continued…
SS0
8 Angled Cut From Outrigger
Summary of Contents for Hammer
Page 1: ...Machine Setup Guide InstallVersion1 09...
Page 5: ...15 Completion You re Good To Go 16 FAQ s 17 Links Contact Details Contents 3...
Page 32: ...The rip fence side is complete 11 Assembly...
Page 74: ...Figure SS03 2 End position 2 Adjustments Alignme nt Link SS03 continued...
Page 79: ...Figure SS07 3 Crosscut stop and block adjustment Adjustments Alignme nt Link SS07 continued...