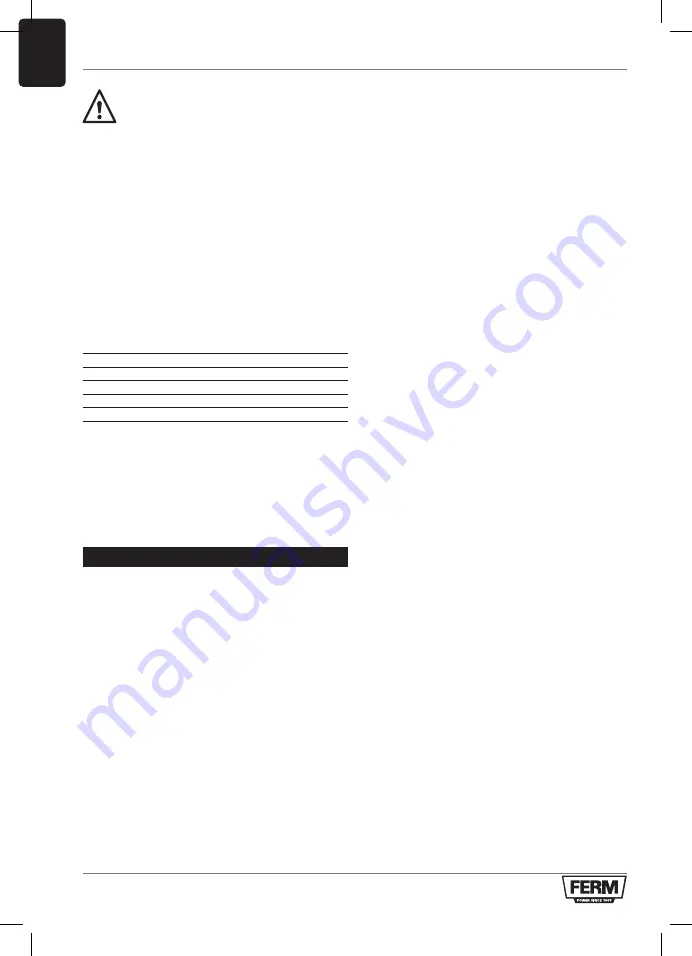
8
EN
Keep the V-belt cover closed during use.
Fig. C & D
If you have shifted the V-belt, you must tighten it
again by means of the motor plate (17) with the
fastening button (18). The tension is correct when
the V-belt can be pressed in by approximately 1
cm. The motor pulley must be aligned horizontally,
so that early wear and loosening of the V-belt can
be prevented. For this purpose the motor pulley
(15) on the motor can be slid along the motor axle,
after loosening the socket head screw.
Spindle speeds
Fig. E
Position V-belt
Revolutions/min
1 600
2 900
3 1300
4 1800
5 2650
The number of revolutions of the drill spindle of
the V-belt combinations can be read from the
illustration and the table.
Test the V-belt tension before you connect the
machine to the electricity mains.
4. OPERATION, HINTS AND TIPS
Depth stop
Fig. A-1
The drill spindle is provided with a depth stop (2).
It can be adjusted using the nut. The drill depth
can be read on the scale division.
Clamping the drill
Fig. F
In the drill head of the bench drill, drills and other
tools with a cylindrical shank can be clamped.
The moment of rotation is transferred to the drill
by means of the tension of the three clamping
jaws. To prevent the drill from sliding away, it must
be clamped using the toothed ring wrench. If the
drill slides away in the drill holder, a slight burr
occurs on the drill shank, which makes centric
clamping impossible. A burr which occurs in this
way must in any case be removed by grinding.
Clamping the workpiece
Fig. G
The drill bench and the footplate of the bench drill
are provided with grooves for fastening clamping
tools. Always clamp the workpiece in the machine
clamp or other clamping tools. In this way you will
prevent accidents and even increase the drilling
accuracy because the workpiece is in a fixed
position.
Adjusting the bench
The drill bench is fastened to the drill column
and can be adjusted in height after loosening the
fastening handle (6). Adjust the bench in such a
way that there is still enough space between the
top of the workpiece and the point of the drill. You
can also swivel the bench sideways, if you wish to
clamp a workpiece directly onto the footplate.
Fig. I
For slanted drilling and with a slanted supporting
surface of the workpiece the bench can be
swivelled. For this purpose loosen the hexagonal
screw (20) on the hinge point of the bench and
remove the centring. Swivel the bench (19) to the
desired position. Then screw down the hexagonal
screw (20) properly using a wrench.
Number of revolutions, speed of rotation, supply
The supply - the feed motion of the drill - takes
place by hand on the 3-armed drill lever. The
speed of rotation is determined by the number of
revolutions of the drill spindle and by the diameter
of the drill. The correct choice of supply and the
number of revolutions of the drill spindle are the
deciding factors for the lifespan of the drill. The
following applies as a basic rule: with a larger
diameter of the drill the number of revolutions
must be adjusted lower; the greater the firmness
of the workpiece, the greater the cutting pressure
must also be.
In order not to overheat the drill in this case, the
supply and speed of rotation must be lowered
at the same time. In addition, the drill must be
cooled with drill oil. For thin plates, quite large
drillings must be carried out carefully with little
supply and little cutting pressure, so as to get
a precise result and so that the drilling remains
the correct size. For deep drilling (larger than 2 x
the diameter of the drill) the discharge of chips is
more difficult and the temperature of the drill is