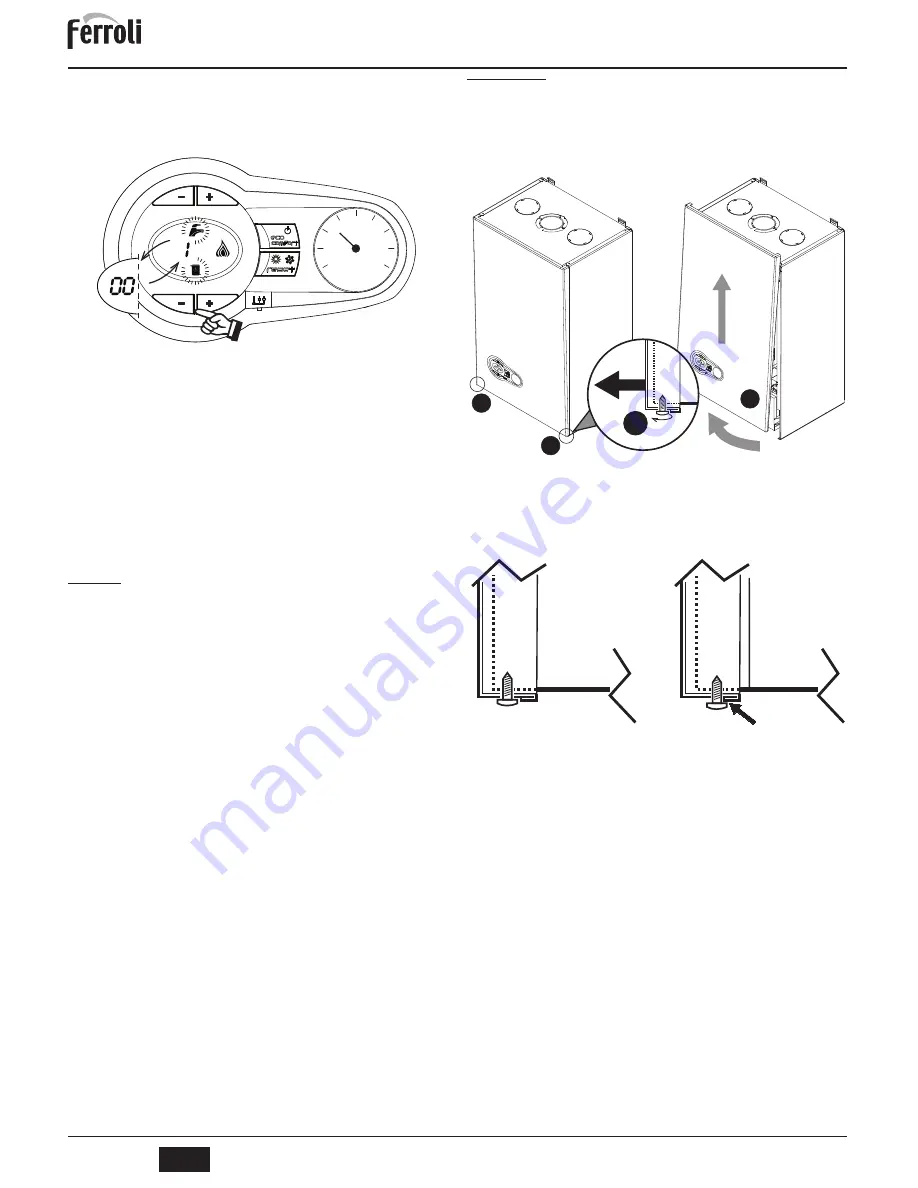
BLUEHELIX TECH C
36
EN
TEST mode activation
Press the heating buttons (details 3 and 4 - fig. 1) together for 5 seconds to activate the
TEST
mode. The boiler lights at the maximum heating power set as described in the fol-
lowing section.
The heating and DHW symbols (fig. 23) flash on the display; the heating power will ap-
pear alongside.
fig. 23 - TEST mode (heating power = 100%)
Press the heating buttons (details 3 and 4 - fig. 1) to increase or decrease the power
(Min.=0%, Max.=100%).
By pressing the DHW
“-”
button (detail 1 - fig. 1), boiler output is immediately adjusted
to min. (0%). By pressing the DHW
“+”
button (detail 2 - fig. 1), boiler output is immedi-
ately adjusted to max. (100%).
If the TEST mode is activated and enough hot water is drawn to activate the DHW mode,
the boiler remains in TEST mode but the 3-way valve goes to DHW.
To deactivate the TEST mode, press the heating buttons (details 3 and 4 - fig. 1) together
for 5 seconds.
The TEST mode is automatically deactivated in any case after 15 minutes or on stopping
of hot water drawing (if enough hot water has been drawn to activate the DHW mode).
Heating power adjustment
To adjust the heating power, switch the boiler to TEST mode (see sec. 4.1). Press the
heating buttons (details 3 and 4 - fig. 1) to increase or decrease the power (min. = 00 -
max. = 100). Press the RESET button within 5 seconds and the max. power will remain
that just set. Exit TEST mode (see sec. 4.1).
4.2 Startup
Before lighting the boiler
•
Check the seal of the gas system.
•
Check correct prefilling of the expansion tank.
•
Fill the water system and make sure all air contained in the boiler and the system
has been vented.
•
Make sure there are no water leaks in the system, DHW circuits, connections or boiler.
•
Check correct connection of the electrical system and efficiency of the earthing system.
•
Make sure the gas pressure for heating is that required.
•
Make sure there are no flammable liquids or materials in the immediate vicinity of
the boiler
Checks during operation
•
Switch the unit on.
•
Check the tightness of the fuel circuit and water systems.
•
Check the efficiency of the flue and air/fume ducts while the boiler is working.
•
Check the correct tightness and efficiency of the condensate removal system and trap.
•
Make sure the water is circulating properly between the boiler and systems.
•
Make sure the gas valve modulates correctly in heating and domestic hot water pro-
duction.
•
Check proper lighting of the boiler by turning it on and off several times with the room
thermostat or remote control.
•
Make sure the fuel consumption indicated on the meter matches that given in the
technical data table on cap. 5.
•
Make sure that with no heating demand the burner correctly lights on opening a hot
water tap. Check that the heating circulating pump stops on opening a hot water tap
during heating operation and there is a regular production of hot water.
•
Check correct programming of the parameters and carry out any required customi-
sation (compensation curve, power, temperatures, etc.).
4.3 Maintenance
Opening the front panel
To open the boiler casing:
1.
Partially undo the screws
A
(see fig. 24).
2.
Pull the panel
B
outwards and release it from the upper fastenings.
B
Before carrying out any operation inside the boiler, disconnect the power and
close the gas cock upstream
fig. 24 - Front panel opening
B
On this unit, the casing also acts as a sealed chamber. After any opera-
tion involving opening the boiler, carefully check the correct refitting of
the front panel and its seal.
Proceed in reverse order to refit the front panel. Make sure it is correctly hooked to the
upper fastenings and is correctly positioned at the sides. When tightened, the head of
screw "A" must not be below the lower fold (see fig. 25).
fig. 25 - Correct position of front panel
Periodical check
To ensure correct operation of the unit over time, have qualified personnel carry out a
yearly check, providing for the following:
•
The control and safety devices (gas valve, flow meter, thermostats, etc.) must func-
tion correctly.
•
The fume exhaust circuit must be perfectly efficient.
•
The sealed chamber must be tight.
•
The air/fume terminal and ducts must be free of obstructions and leaks
•
The burner and exchanger must be clean and free of deposits. Do not use chemical
products or wire brushes to clean.
•
The electrode must be properly positioned and free of scale.
•
The gas and water systems must be tight.
•
The water pressure with system cold must be approx. 1 bar; otherwise bring it to that value.
•
The circulating pump must not be blocked.
•
The expansion tank must be filled.
•
The gas flow and pressure must match that given in the respective tables.
•
The condensate removal system must be efficient, with no leaks or obstructions.
•
The trap must be full of water.
0
1
4
2
3
A
A
B
A
OK
NO
cod. 3541C00
-
5HY
Summary of Contents for BLUEHELIX TECH C
Page 78: ......
Page 79: ......
Page 80: ...FERROLI S p A Via Ritonda 78 a 37047 San Bonifacio Verona ITALY www ferroli it ...